
More than 60 years ago, Dr. Gilbert Wanninger, an engineer at Waldrich Siegen Gmbh, a machine tool manufacturer, invented a simple device to improve cable management and lengthen cable life in moving applications. This initial design of the cable carrier kicked off a whole industry, with Tsubaki Kabelschlepp being the original designer of steel link cable carriers.
Cable carriers are designed to house cables, and are usually made of plastic, steel, or a metal alloy. These structures are used to protect cables and hoses on moving machinery, by preventing tangling. In addition, they help prevent cables and hoses from getting caught in any moving parts of a machine.
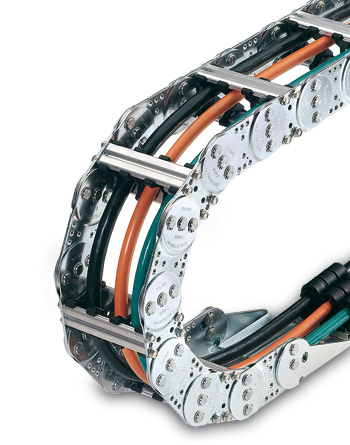
Cable carriers can be used in a variety of applications, especially in systems that require a great deal of movement, such as robotics and machine tool and large off-road and industrial machinery. They are suitable to these applications because they can support the heavy weight of numerous cables and hoses, without sagging or putting stress on the cabling. They also make managing and routing the cables through a machine or factory much simpler and provide easy access for troubleshooting or maintenance as well.
60*150 mm MT open type nylon flexible both side openable cable chain
Cable carrier styles can be either open or closed. Open varieties allow for easy access to the cables and visible access as well, whereas closed carriers seal off the cables from the environment to protect them from environmental contaminants such as metal filings.
Steel and other metal alloy carriers are best suited for heavy mechanical loads that run long distances carrying large cables and hose. Steel cable carriers are designed to handle harsh environments with ease; even long-term temperatures above 600° without negative impact. Through the use of stainless steel and/or corrosion-resistant coatings, a metallic cable carrier can have a much higher resistance to many of the chemicals that damage nylon reinforced carriers, although some specially designed polymers offer this resistance as well.

While a metallic cable carrier might have a higher up-front cost over a nylon carrier, the metallic cable carrier’s ability to eliminate costly guide channels and support trays make them very cost effective against a nylon cable carrier in certain applications.
Because they don’t require maintenance or lubrication, steel cable carriers are ideal in tough environments, such as heavy-duty machinery found in foundries, mills, refining, offshore, construction, and mining applications.

Plastic cable carriers, made from high-performance polymer or nylon, are less expensive than their metal counterparts and offer reduced weights while being corrosion resistant in hostile environments. They are usually used in more light- and medium-duty applications. Some designs made of the polymers can resist seawater and mineral oils, making them suitable to similar applications as metal designs.
Featuring a modular design, plastic cable carriers are easy to maintain and replace damaged or broken links. They can be opened and disassembled by popping them open with a screwdriver or special tool to “unzip” the links. Plastic cable carriers feature a modular design, allowing them to be highly configurable to any application, as well as easy to maintain. Damaged or broken links can simply be removed and substituted with a new link; the design allows for quick assembly and disassembly with a standard screwdriver at the OEM, or on the floor where the repair is immediately required. Some plastic carriers can even be opened by hand.
You must know several details before you can decide if steel or plastic will be a better option for your application. You must know the types and sizes of all cables and hoses to be housed in the carrier. Then, you must calculate the minimum cavity height and width of the largest cable or hose. Knowing the cable and hose’s bend radius will help you determine the carrier’s bend radius. Also, it is critical to know the machine’s total travel distance.
There are several design considerations to take into account in the cable carrier selection process. Keep in mind, a best practice is to size the carrier to the cables, rather than trying to force a cable bundle into a pre-selected carrier. The most important factors when designing a cable carrier system are:

• Sizes and types of electrical, fiber optic, hydraulic, pneumatic, and media lines
• Additional cable and hose loading
• Speed of the system
• Maximum acceleration and deceleration values
• Operating window size constraints
• Total travel distance/stroke length
Finally, you must consider load, speed and unsupported travel lengths when sizing and specifying a cable carrier. The load not only takes into account the total weight of the cables and hoses in the carrier, but also the weight of any fluids in such hoses, in lb-ft. Remember, metal carriers are best suited to unsupported loads.