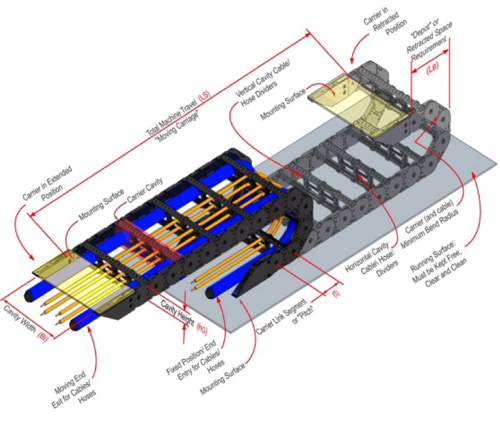
Of all the machine design details to worry about, cable carriers probably don’t top your list. Yet if you care about the reliability and uptime of moving machines, it pays to devote extra engineering attention to cable carriers and the components within them. A well-designed cable carrier will dramatically extend the life of cables and fluid power supply lines—by protecting them from damaging bends, crimping, abrasive wear and crushing.
Unfortunately, not all cable carriers are well designed. Their internal cavities may be too small for the components they carry. They may be too long or short. They may be made from the wrong materials for the job. Or they may lack internal dividers. These poorly designed carriers can trigger the very same cable and supply line failures they were supposed to prevent, causing expensive machine downtime.
Fortunately, the potential for failures can largely be avoided by following a collection of simple carrier design guidelines that have been field tested.
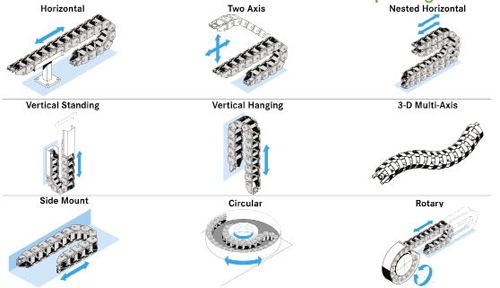
Get the right size
Job one in cable carrier design is to determine the minimum bend radius and clearances of all the components that will fill the carrier. The following rules of thumb will help:
Minimum Bend Radius. For power and signal cables, use the minimum bend radius assigned by the cable manufacturer. For hoses, minimum bend radius is 5x diameter. For hydraulic lines, minimum bend radius is 7.5x diameter. The largest cable or hose diameter should dictate the carrier bend radius, and it’s a good idea to put a 10% safety factor on the bend radius to account for any unreleased tension in the cables or hoses.
Clearance Safety Factors. Always add clearance safety factors to the outside diameters of all the carrier components. For cables, add 10%. For air hoses, add 15%. And for hydraulic lines, add 20%.
Cavity Dimensions. The inner cavity height should be based on the largest carrier component plus its safety factor. To determine cavity width, sum all the cable and line diameters along with their safety factors.
Σ all Φ = Σ cΦ + sf + Σ pnΦ + sf + Σ hydΦ + sf
Where:
c Φ = cable OD
pn Φ = pneumatic lines OD
hyd Φ = hydraulic lines OD
sf = safety factor.
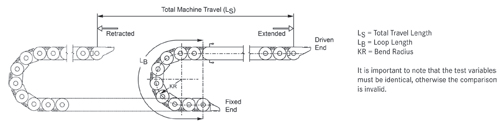
Distribute the weight
Uneven stresses will shorten carrier life, so you should carefully distribute the weight of the fill components within the carrier. To do that, take the time to calculate the weights of individual components, and place the heaviest components on the outside of the carrier.
60*150 mm MT open type nylon flexible both side openable cable chain
Calculate length and mounting pivots
Another crucial design task relates to the determination of carrier length and location of the fixed mounting points. Rather than guessing, you can use the above formulas to calculate exactly how long the carrier should be.
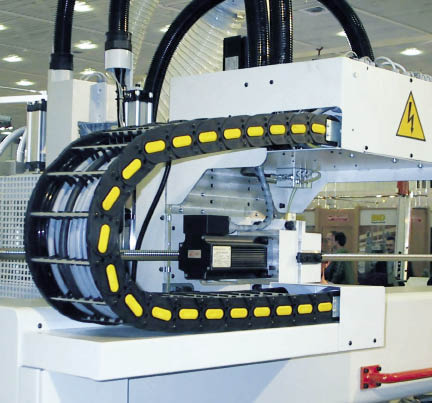
Pick the right materials
Most automation systems today run with nylon carriers—and for good reason. Nylon minimizes the carrier’s costs and weight while maximizing flexibility and providing good chemical resistance. Plastic also reduces the carrier noise substantially.
However, there are times when zinc-plated steel carriers are a better choice. Metal carriers require less support than their nylon counterparts, which can eliminate installation hardware and cost. Metal carriers can also withstand much higher operating temperatures— 750°F for an all-steel system vs. 265 °F for a carrier with nylon parts. Metal carriers additionally tolerate more aggressive chemical exposures than nylon carrier. When the service environment involves weld splash, solvent exposure or abrasive conditions, steel carriers are the best option.
Divide the carrier
Even if the carrier has not been overfilled, cables and hoses can come into contact with one another or twist within the carrier. Premature wear results. That’s why it’s a good idea to divide the carrier into separate cavities so the cables and hose can all move independently of one another.
Engineers all to often skip the dividers or don’t use enough of them for a given carrier length. We recommend using them every other link whenever the carrier contains more than three conductors—which means in the vast majority of populated carrier applications. Dividers come in many styles, but the type of divider selected is less important than making sure they are included in the carrier design.
Seek help
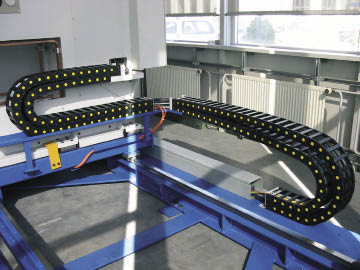
The guidelines presented in this paper represent a good start when it comes to designing serviceable cable carriers. For the best results, involve your cable and carrier vendors in the design process. They work with carriers every day and can offer additional engineering expertise that will help you design a carrier that will go the distance.
The Populated Carrier Alternative
Engineers with the right experience can successfully design populated cable carriers from individual components. With complex carriers, however, they shouldn’t bother.
It often makes more sense to buy fully populated carriers that contain all the cables, connectors, supply lines and connectors required by a given application. These populated carriers offer compelling technical and economic advantages, including:
Improved performance and life cycle. The engineers who specialize in populated carriers have expertise and engineering tools that allow them to maximize carrier performance and life cycle.
Cost reduction. A typical carrier can contain dozens of components, all of which must be specified, purchased and inventoried. The carrier will also require design engineering hours and assembly labor before it can be bolted on the machine. A populated carrier, by contrast, arrives on your shop floor as a single bill-of-materials item, ready for installation. The savings can be substantial. Populated carriers can cost as much as 25% less than a comparable component-built carrier if you account for the supply chain, engineering and assembly costs.