Which cable carrier is right for your application?
Which cable carrier is right for your application?
An explanation of different cable carrier styles
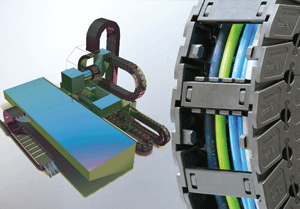
Cable carriers that replace the standard pin-bore connection with a flexible link offer lower vibration and less noise for machine tools.
Cable carriers guide and protect cables and hoses on automated machinery. They prevent cables and hoses from tangling, becoming damaged by debris, or interfering with a machine’s operation. Any application involving constant repetitive motion on moving equipment, such as multiaxis robots, machine tools, press-transfer systems, gantry robots, machining centers, and turning and grinding machines, can benefit from a cable carrier system.
At first glance, a cable carrier may seem like a fairly basic part of an automated system. However, when you consider the trend toward faster speeds, increased accelerations, and heavier loads, the importance of specifying the right cable carrier becomes clear.
Initially the vast number of designs and options available can prove intimidating. For this reason, it’s important to have a basic understanding of the different types of cable carriers available and their various advantages and limitations.
Steel or Plastic?
One fundamental decision is whether to use a steel or plastic cable carrier. The main advantage with steel is that it can withstand high temperatures. Plastic cable carriers can tolerate temperatures between -40 and 260 degrees F, but for temperatures beyond these, a steel cable carrier is the only option.
With this exception, plastic cable carriers can be used in most applications. Moreover, plastic carriers are resistant to corrosion, chemicals, and UV rays and are lightweight, which enables faster speeds, higher cycles, and increased production throughput.
Cable Carrier Types
Another key decision is what cable carrier style is the best solution. The basic nonopening style has crossbars molded directly into the side links. This very simple, cost-effective design is suitable for small applications. However, it is important to note that, once this carrier is installed, there is no quick, easy way to access cables and hoses. Instead, the cables and hoses must be fed in from one end. This can make retrofitting any conduits time-consuming, especially when they have connectors on the end.
The next level of cable carrier features an opening crossbar. Hinged lids (Figure 1) allow crossbars to be opened either from the inside or outside diameter using only a screwdriver and completely removed for full access to cables and hoses. This type of cable carrier tends to have more options when it comes to separators and mounting brackets than those that do not open.
60*150 mm MT open type nylon flexible both side openable cable chain
A different type of cable carrier offers a flexible, split crossbar, which allows conduits to be pushed directly into the cable carrier without using any tools. This saves time when retrofitting cables and hoses. However, the split-crossbar design limits span and load capacity, and it should be used only for lightweight cable packages and travels over less than 10 ft.
Another easy-open design has crossbars that interconnect much like a zipper (Figure 2). These can be removed manually as a separate assembly to enable full access to cables and hoses. This type of cable carrier is ideal for applications with travels less than 6 ft.
When heavier loads are involved, a cable carrier with side links that interlink via a tongue-and-groove design or with vibration-dampening, integrated stop dogs is a good choice. These modular carriers have excellent lateral stability for travel distances over 100 ft.

: Figure 1: Hinged lids mean crossbars can be opened either from the inside or outside diameter for full access to cables and hoses.
Carriers with flexible links instead of the standard pin-bore connections enable low-vibration, low-noise operation. Modular links easily can be added to or removed from these carriers to adjust the overall length, unlike one-piece extruded designs.
Movement
Whether your cable carrier needs to move in linear or rotary motion will affect which cable carrier design you opt for. Some cable carriers move freely through multiple axes and can negotiate complex configurations (Figure 3), such as might be found on a six-axis robot.
Safety and Durability
Plastic cable carriers are made from a flame-retardant polymer. If additional protection is required for cables and hoses, fully enclosed cable carriers are available with lids instead of crossbars. This design is better for applications involving metal chips or hot, flying debris. Some special materials
(Figure 4) can withstand hot metal chips up to 1,500 degrees F and higher. Before these materials were developed, only steel chains could withstand these temperatures.
Other Considerations
In addition to the style of cable carrier used, it’s important to consider other factors, such as which cables and hoses will be installed and their size and weight.
The length of travel, minimum bend radius, environmental factors—debris, heat, or chemicals—and the speeds and accelerations involved are also significant considerations. For example, the length of travel directly affects the size of the chain that should be used. If the cable carrier must travel over distances greater than 50 ft and glide on itself, guide throughs (Figure 5) and built-in rollers often are required.
Follow the Rules
Always adhere to cable distribution rules to determine the proper cable layout and separation within the carrier. Interior separators or shelves are important to ensure proper cable alignment within the cable carrier. The faster and more frequent the movement, the more important exact positioning of the cables becomes. For example, in high-speed applications greater than 1.5 FPS or 10,000 cycles per year, cables should not be laid on top of each other without horizontal separation.
It is also vital to calculate acceleration and push force to ensure the cable carrier is strong enough to support the application in the first place. The force required must be less than the maximum force for the selected cable carrier.
Strain relief is important to keep cables in place at either end of a cable carrier. Sometimes strain relief at just the moving end is sufficient, depending on the application. Improper strain relief is a common cause of cable and hose failure.
Increasing demands in the field of automation require cable carrier systems to withstand higher speeds and accelerations, longer travels, and heavier loads than ever before. Thankfully, innovative cable carrier manufacturers have developed a broad range of options for almost any application.