Exploring the Benefits and Applications of Screw Type Chip Conveyors in Industrial Settings
Understanding Screw Type Chip Conveyors Efficiency in Metalworking
In the realm of metalworking, the management of metal chips and shavings is a critical aspect of maintaining productivity and efficiency. One innovative solution that has gained immense popularity is the screw type chip conveyor. This system offers a reliable method of moving metal chips generated during machining processes, helping manufacturers streamline operations and enhance workplace safety.
What is a Screw Type Chip Conveyor?
A screw type chip conveyor, often referred to as a screw conveyor or auger conveyor, is a mechanical device designed to transport bulk materials, in this case, metal chips, from one location to another. The fundamental design consists of a helical screw blade, which rotates around a central shaft within a trough. As the screw turns, it moves the chips in a consistent and controlled manner, allowing for efficient transportation to collection bins or disposal areas.
Key Advantages of Screw Type Chip Conveyors
1. Space Efficiency One of the most significant benefits of screw type chip conveyors is their compact design. Unlike traditional belt conveyors, which require extensive floor space, screw conveyors can be installed in tighter environments, minimizing the overall footprint of the conveyor system. This is particularly advantageous in busy machine shops where space is at a premium.
2. Versatility Screw type chip conveyors can handle a wide range of materials, including metallic, plastic, and composite chips. This versatility makes them suitable for various applications in industries such as automotive, aerospace, and heavy machinery. Additionally, they can be configured to operate at different angles, allowing for customized installation according to specific workshop layouts.
3. Reduced Downtime By effectively transporting metal chips away from machining operations, screw type conveyors help prevent machining interruptions that can lead to delays. This efficient removal of waste not only enhances the speed of production but also reduces the likelihood of machine wear, thereby extending equipment life.
screw type chip conveyor
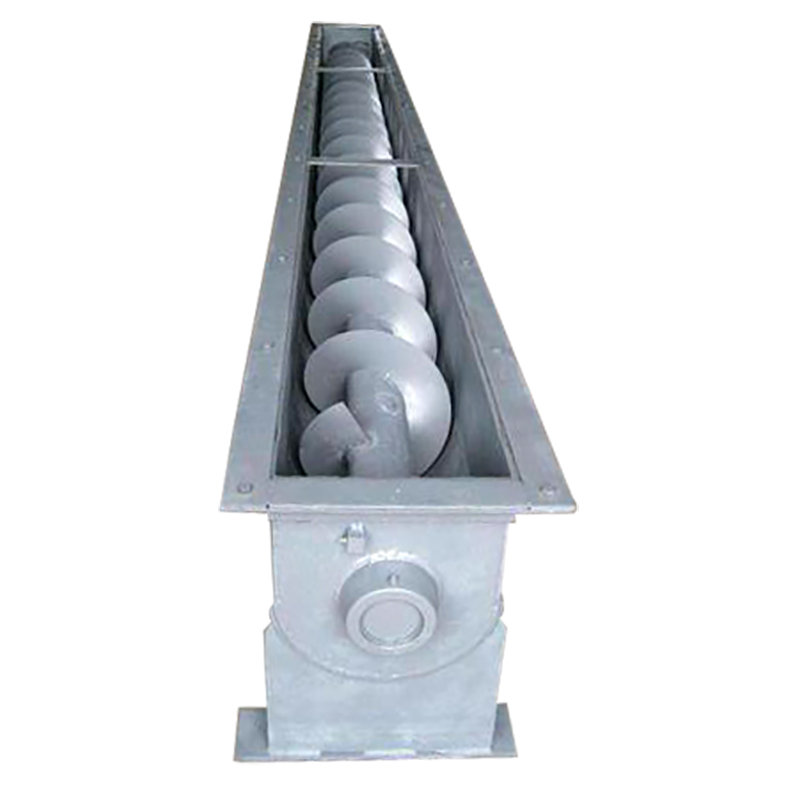
4. Improved Workplace Safety Accumulated metal chips on the shop floor can pose hazards, including slips and falls, along with potential fire risks. A screw type chip conveyor mitigates these risks by continuously transporting waste material away from work areas, thus ensuring a cleaner and safer working environment.
5. Maintenance and Durability Screw conveyors are designed for durability, often made from high-strength materials to withstand the rigors of heavy-duty applications. Their straightforward design also means that maintenance is typically minimal, reducing manual labor and downtime associated with repairs.
Installation and Operation
Installing a screw type chip conveyor involves careful planning and consideration of the workflow in a manufacturing facility. Factors such as the location of machining operations, the type of materials being processed, and the specific requirements for chip disposal must all be taken into account. Once installed, the system operates with minimal supervision, allowing operators to focus on more critical aspects of production.
As the chip conveyor system operates, the rotating screw not only transports chips but also aids in the cooling and drying of materials, depending on the design and application. Regular monitoring and occasional maintenance, such as checking for wear on the screw blades and lubricating moving parts, ensure long-term reliability.
Conclusion
In conclusion, screw type chip conveyors represent a vital component of modern metalworking environments. Their ability to efficiently handle the byproducts of machining processes enhances productivity, supports workplace safety, and contributes to the overall effectiveness of manufacturing operations. As industries continually seek ways to improve efficiency and reduce waste, the adoption of screw type chip conveyors will undoubtedly play a key role in shaping the future of metalworking.