loom tubing split
The Role of Loom Tubing Split in Modern Manufacturing
In the continuously evolving landscape of modern manufacturing, efficiency and precision are paramount. One of the crucial components that significantly impacts both of these factors is loom tubing split. This term refers to the division of loom tubing used in machinery that creates textile products, particularly in weaving and knitting processes. Understanding loom tubing split is essential for manufacturers striving to enhance production techniques and improve product quality.
Loom tubing is designed to guide and control the yarn as it moves through various stages of the weaving process. The design and mechanics of loom tubing can vary significantly depending on the type of textile being produced, the production volume, and the specific requirements of the machinery used. As a result, manufacturers often encounter situations where a single piece of loom tubing is insufficient. This is where loom tubing split comes into play.
Loom tubing split involves cutting or segmenting the loom tubing into smaller, more manageable sections or splits. This segmentation allows for better customization and adaptability, enabling manufacturers to configure their machines to optimize performance based on specific production needs. There are several advantages to adopting loom tubing split in manufacturing processes.
Firstly, one of the most significant benefits is enhanced flexibility. Different fabric types require various thread tensions and paths through the machinery. By implementing a segmented loom tubing system, manufacturers can easily adjust the configuration according to the requirements of the fabric being processed. This flexibility reduces downtime associated with changing setups and increases the overall throughput of the manufacturing process.
loom tubing split
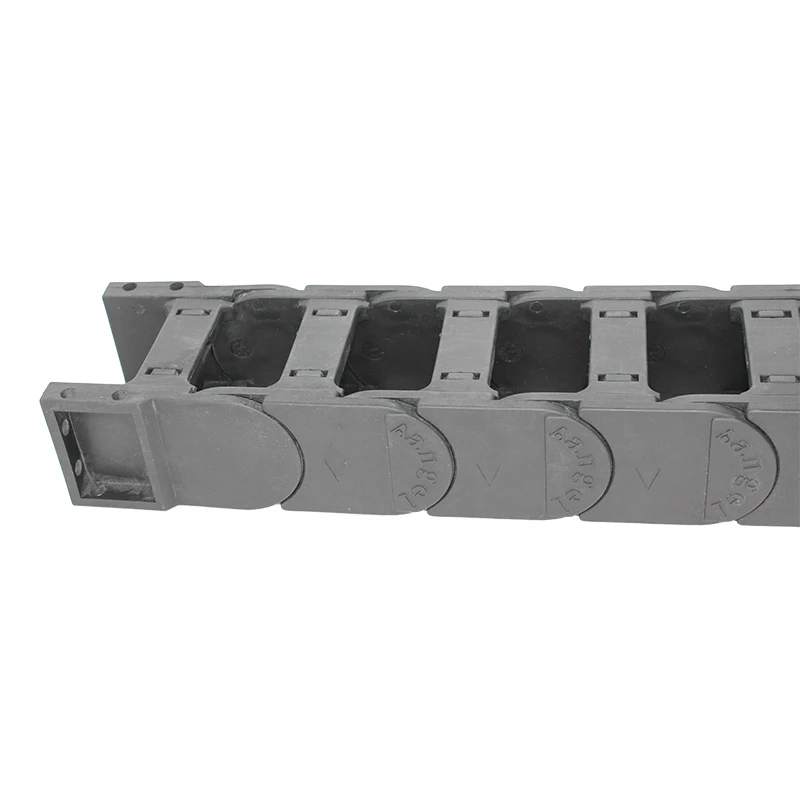
Secondly, loom tubing split can contribute to improved precision. When loom tubing is split into various sections, each section can be tailored for specific functions, ensuring that the yarn moves seamlessly through the machine. This precision minimizes the risk of yarn breakage or tangling during operation, which is crucial for maintaining high-quality standards in textile production. Furthermore, the ability to fine-tune individual sections of tubing allows for better control over the textile production process, resulting in more consistent and reliable outputs.
Another notable advantage of loom tubing split is improved maintenance and repair capabilities. In traditional systems where tubing is longer and single-piece, replacing or repairing malfunctioning sections can be cumbersome and time-consuming. However, with segmented systems, manufacturers can quickly isolate and replace only the affected section, thereby significantly reducing maintenance time and costs.
Cost efficiency is an additional factor that makes loom tubing split an attractive option for manufacturers. By customizing and segmenting their loom tubing, companies can often reduce material waste. Instead of replacing entire tubes or systems, manufacturers can replace only specific segments, thus optimizing their resource usage. Moreover, improved efficiency in the production process can lead to higher output without a corresponding rise in costs, further enhancing profitability.
In terms of implementation, adopting loom tubing split requires a careful analysis of machinery requirements, production goals, and existing processes. Collaboration between engineers, production managers, and textile experts is essential to effectively design a segmented loom tubing system that meets a company’s specific needs. Furthermore, training operators on the new systems and processes is critical to ensure a smooth transition and to maximize the potential benefits of loom tubing split.
In conclusion, loom tubing split represents a significant innovation in the textile manufacturing industry. By allowing for enhanced flexibility, improved precision, simplified maintenance, and cost efficiency, this approach to loom tubing can transform production processes. As manufacturers continue to strive for efficiency in the face of increasing global competition, the adoption of technologies like loom tubing split will likely play a crucial role in shaping the future landscape of textile manufacturing. With these advancements, manufacturers are not only boosting their operational capabilities but also contributing to the sustainability and quality of the products they deliver to consumers.