loom tubing split
Understanding Loom Tubing Split A Comprehensive Overview
In the realm of textile production and manufacturing, the term loom tubing split has garnered considerable attention. It signifies a specialized process that enhances efficiency and quality in weaving. To understand its relevance, we must explore the components of loom operation, the significance of tubing in the weaving process, and the implications of splitting loom tubing in production.
The Basics of Loom Operation
Looms are intricate machines that serve as the backbone of the textile industry. They are designed to interlace threads, known as the warp and weft, to create fabric. The efficiency of this process is paramount for manufacturers, as it directly impacts production time, cost, and fabric quality. Traditional looms can operate with a certain level of efficiency; however, advancements in technology continue to refine and elevate operational capabilities.
The Role of Tubing
In weaving, tubing is introduced primarily as a means of guiding and protecting yarns as they traverse the loom. Tubes help manage tension, reduce friction, and streamline the passage of threads, ensuring that yarns are organized and do not tangle or snag during the weaving process. The use of optimal tubing materials can significantly affect the performance of the loom, influencing everything from speed to the texture of the final product.
What is Loom Tubing Split?
The term loom tubing split refers to a situation in which the tubing used in loom operations is designed or altered into two separate channels or paths. This split allows for the independent control of different yarns as they are fed through the loom. By separating the pathways for various threads, manufacturers can achieve a more precise and versatile weaving process. This innovation can lead to an expanded range of patterns, improved tension management, and the ability to layer multiple threads together seamlessly.
loom tubing split
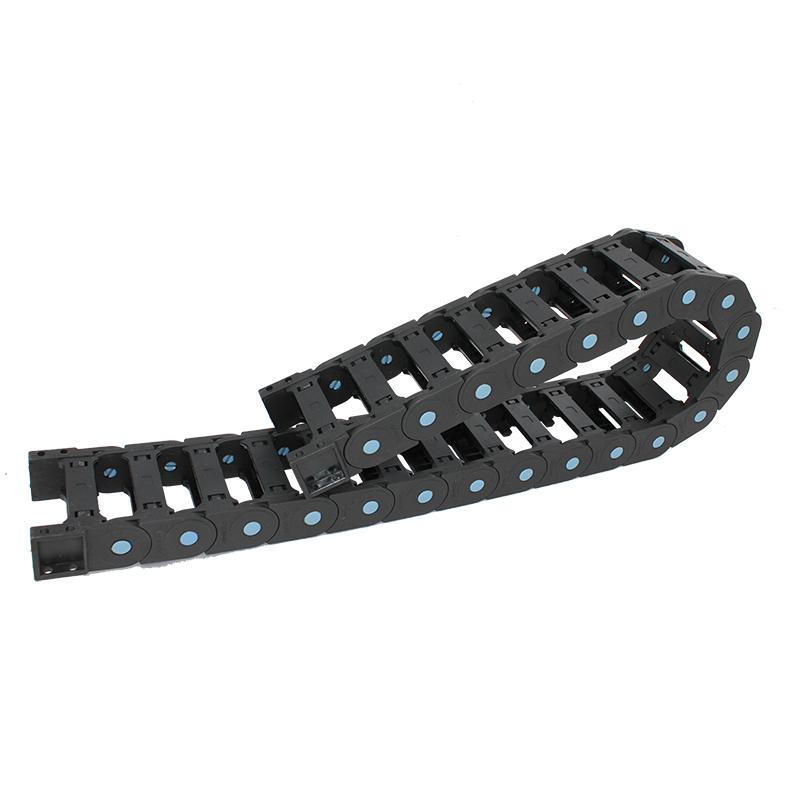
Implications of Loom Tubing Split
1. Enhanced Production Efficiency One of the primary advantages of loom tubing split is its ability to increase throughput. With separate channels for different threads, looms can operate at higher speeds without compromising quality. The reduction in tangles and snags leads to less downtime for maintenance and corrections, ultimately streamlining production schedules.
2. Improved Fabric Quality With better control over threading, the loom can produce fabrics with higher precision. This allows manufacturers to create complex designs and textures that would be difficult, if not impossible, to achieve with traditional weaving methods. The split also minimizes the risk of uneven tension, which can lead to flaws in the fabric.
3. Greater Flexibility in Design Loom tubing split allows for a wider variety of materials to be used simultaneously in the weaving process. For example, various types of yarn—such as cotton, polyester, or blends—can be woven together in a single operation. This flexibility is vital in meeting the diverse demands of the textile market.
4. Cost-effectiveness While there may be an initial investment in upgrading loom equipment to accommodate split tubing, the long-term savings in labor, maintenance, and material waste can be significant. Manufacturers can maximize their output and reduce costs associated with fabric defects or rework, enhancing overall profitability.
5. Sustainability Considerations Because split loom tubing can lead to more efficient production processes, it aligns with the industry's move towards sustainability. By maximizing material use and reducing processes that generate waste, manufacturers can contribute to a more environmentally friendly approach to textile production.
Conclusion
In conclusion, loom tubing split is not merely a technical adjustment; it represents a significant advancement in the weaving process. By separating the pathways for yarns, this innovation enhances operational efficiency, improves fabric quality, offers design flexibility, reduces costs, and aligns with sustainability goals. As the textile industry continues to evolve, embracing such innovations will be crucial for manufacturers aiming to thrive in a competitive market. The future of weaving looks promising with tools like loom tubing split leading the way.