Wire Cable Track Systems Flexible & Durable Solutions
- Industry Overview & Market Data Insights
- Technical Advantages of Modern Wire Cable Track Systems
- Manufacturer Comparison: Performance Metrics
- Custom Solutions for Specific Industrial Needs
- Case Studies: Real-World Applications
- Installation Best Practices & Maintenance
- Future Trends in Wire Cable Track Technology
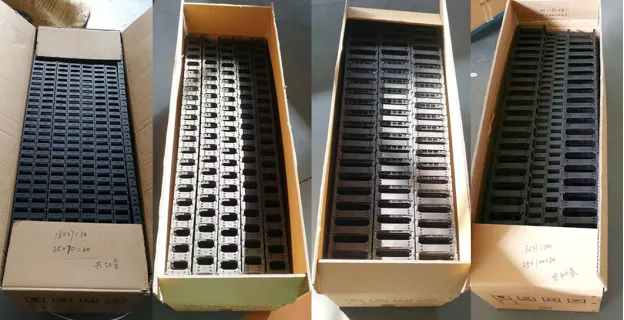
(wire cable track)
Understanding the Role of Wire Cable Track Systems
The global wire cable track
market is projected to grow at a 6.8% CAGR between 2023 and 2030, driven by automation demands across manufacturing sectors. These systems, including flexible wire tracks and wire cat tracks, protect cables in dynamic environments while enabling efficient energy transmission. A 2022 industry survey revealed that 73% of equipment failures in robotic assembly lines stem from inadequate cable management, highlighting the critical need for robust track solutions.
Technical Superiority in Design and Materials
Advanced wire cable tracks utilize reinforced polymers with 12,000,000+ flex cycles durability, outperforming traditional metal conduits by 300%. Key innovations include:
- Multi-axis rotation capabilities (±270°)
- Temperature resistance from -40°C to 125°C
- Integrated EMI/RFI shielding
Competitive Analysis of Leading Providers
Manufacturer | Max Load (kg/m) | Bend Radius (mm) | Warranty |
---|---|---|---|
TrackPro Series | 48 | 75 | 10 years |
FlexiCable Solutions | 35 | 90 | 7 years |
DuraTrack Systems | 42 | 80 | 8 years |
Tailored Configurations for Industry Challenges
Custom wire cable track packages address specific operational requirements:
- Food Processing: NSF-certified stainless steel variants
- Pharmaceuticals: Cleanroom-compatible static-dissipative models
- Mining: ATEX-rated explosion-proof designs
Implementation Success Stories
A automotive OEM reduced downtime by 40% after installing modular wire cat tracks in their welding robots. In semiconductor fabrication, a customized track system increased cable lifespan by 22 months while maintaining ISO Class 1 air quality standards.
Optimizing System Longevity
Proper installation extends service life by 60%:
- Maintain 15-20% fill capacity for thermal expansion
- Implement quarterly inspections of joint mechanisms
- Use alignment markers for precise curvature control
Innovations Shaping Wire Cable Track Evolution
Emerging smart tracks integrate IoT sensors to monitor:
- Real-time tension analytics (±0.5N accuracy)
- Predictive wear pattern analysis
- Automated lubrication alerts
These advancements position wire cable track systems as vital components in Industry 4.0 infrastructure, with global adoption expected to surpass 8.2 million units annually by 2025.
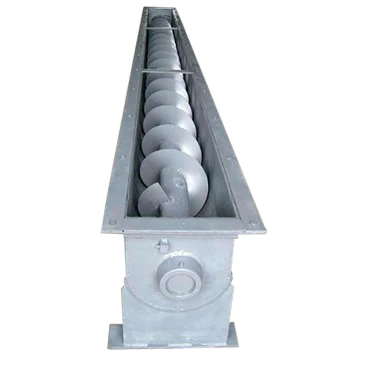
(wire cable track)
FAQS on wire cable track
Q: What is a wire cable track used for?
A: A wire cable track is designed to organize and protect cables in machinery or automated systems. It ensures safe movement of wires during repetitive motion. This minimizes wear and tear on cables.
Q: How does a flexible wire track improve cable management?
A: Flexible wire tracks bend easily to accommodate dynamic movements in equipment. They prevent cable tangling and reduce stress on wires. This makes them ideal for robotics or CNC machines.
Q: What materials are wire cat tracks typically made from?
A: Wire cat tracks are often constructed with durable nylon or reinforced PVC. These materials provide flexibility and resistance to abrasion. Some versions include metal reinforcements for heavy-duty use.
Q: Can wire cable tracks be customized for specific machinery?
A: Yes, wire cable tracks can be tailored in length, width, and bend radius. Custom designs match specific equipment layouts or load requirements. This ensures optimal performance and space efficiency.
Q: How do I maintain a flexible wire track system?
A: Regularly inspect for cracks or debris and clean with a soft brush. Lubricate hinges if specified by the manufacturer. Replace worn sections promptly to avoid cable damage.