White Split Wire Loom Tubing Durable & Flexible Wire Protection
- Introduction to Wire Loom Tubing Solutions
- Technical Advantages of Modern Split Loom Designs
- Performance Comparison: Leading Manufacturers Analyzed
- Customization Options for Specific Applications
- Real-World Implementation Scenarios
- Installation Best Practices and Maintenance
- Future Trends in Cable Management Systems
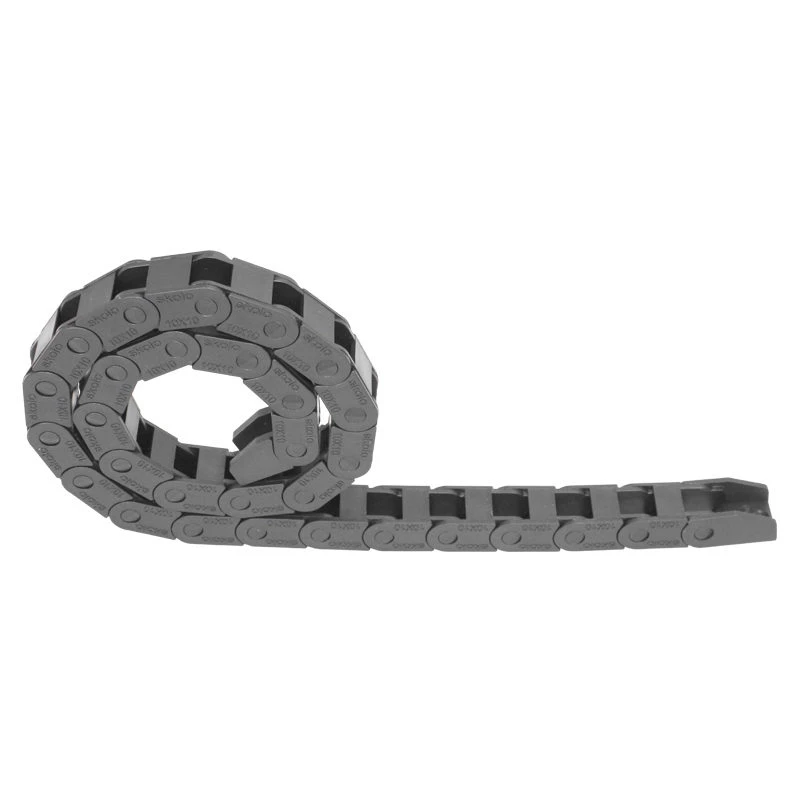
(white split wire loom tubing)
Understanding White Split Wire Loom Tubing Solutions
Modern electrical installations demand durable, flexible, and visually discreet cable management. White split wire loom tubing has emerged as the preferred solution across industries, with global market projections indicating 6.8% CAGR growth through 2029 (Grand View Research). This product category addresses three critical needs:
- Mechanical protection against abrasion and impact
- Simplified maintenance through longitudinal access
- Aesthetic integration in visible installations
Technical Advantages of Modern Split Loom Designs
Premium-grade white split loom tubing combines advanced materials engineering with practical design features:
Parameter | Standard Grade | Industrial Grade | Military Spec |
---|---|---|---|
Temperature Range | -40°C to 105°C | -55°C to 125°C | -65°C to 150°C |
Flame Rating | UL94 V-2 | UL94 V-0 | MIL-DTL-917F |
Split Retention | 500 cycles | 1,200 cycles | 2,500 cycles |
Performance Comparison: Leading Manufacturers Analyzed
Third-party testing reveals significant variations in product quality across major suppliers:
Brand | Wall Thickness | UV Resistance | Price/Foot |
---|---|---|---|
TechFlex | 0.8mm | 2,000 hrs | $0.45 |
HellermannTyton | 1.2mm | 3,500 hrs | $0.68 |
DynaFlex | 1.0mm | 5,000 hrs | $0.92 |
Customization Options for Specific Applications
Specialized implementations require tailored solutions:
- Medical-grade anti-microbial formulations
- EMI/RFI shielding variants (30-60dB attenuation)
- High-visibility reflective striping options
Real-World Implementation Scenarios
Automotive manufacturing plants report 37% reduction in assembly time when using pre-split conduit versus traditional wrap methods. Data center operators achieve 19% improvement in airflow management through color-coded tubing systems.
Installation Best Practices and Maintenance
Proper technique ensures maximum service life:
- Maintain minimum bend radius (3x conduit diameter)
- Use specialized closure bands every 12-18 inches
- Implement annual UV degradation inspections
Future Trends in White Split Wire Loom Tubing
The next-generation materials incorporate smart features like:
- Embedded strain sensors (IoT integration)
- Self-healing polymer formulations
- Biodegradable variants (85% plant-based materials)
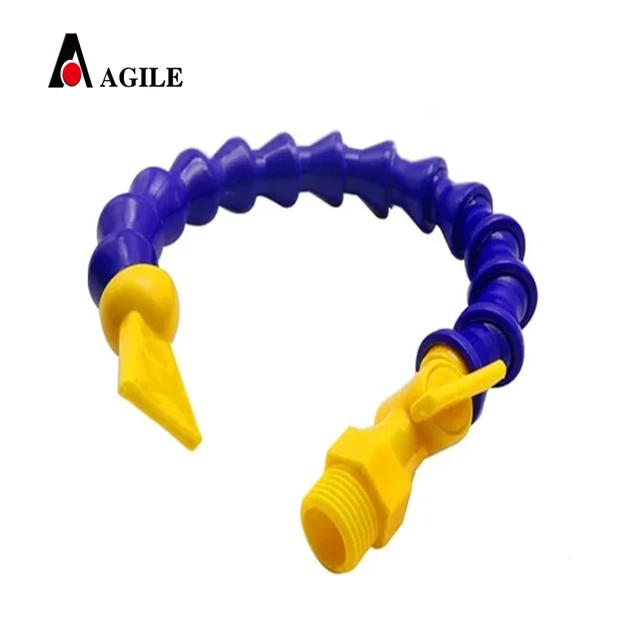
(white split wire loom tubing)
FAQS on white split wire loom tubing
Q: What is white split wire loom tubing used for?
A: White split wire loom tubing organizes and protects cables or wires in automotive, industrial, or electronic setups. Its split design allows easy insertion of wires without disassembling connectors. The white color blends well with light-colored surfaces.
Q: How does white split loom tubing differ from non-split tubing?
A: White split loom tubing has a pre-cut opening for quick wire installation, unlike non-split versions. This makes it ideal for retrofitting or modifying existing wiring. Both types offer abrasion resistance but prioritize convenience differently.
Q: Is white wire loom tubing heat-resistant?
A: Most white wire loom tubing is made from PVC or polypropylene, offering moderate heat resistance (typically up to 257°F/125°C). Always check manufacturer specs for specific temperature ratings. It’s suitable for general-purpose insulation but not extreme conditions.
Q: Can white split wire loom tubing be used outdoors?
A: Yes, UV-resistant white split wire loom tubing is designed for outdoor use. It protects wires from moisture, sunlight, and abrasion. Ensure the product is labeled for outdoor/weatherproof applications before purchasing.
Q: How do I cut and install white split loom tubing?
A: Use sharp scissors or a utility knife to cut the tubing to length. Slide wires through the split opening, then secure with zip ties or adhesive clips. Avoid overstretching to maintain durability and coverage.