Metal Chip Conveyor Systems Types, Uses & Efficient Scrap Removal
- Introduction to chip conveyors and their industrial significance
- Technical advantages of modern metal chip conveyors
- Performance comparison of leading chip conveyor manufacturers
- Customization strategies for specific operational requirements
- Engineering principles behind different chip conveyor types
- Maintenance protocols for optimal system longevity
- Real-world applications and operational benchmarks
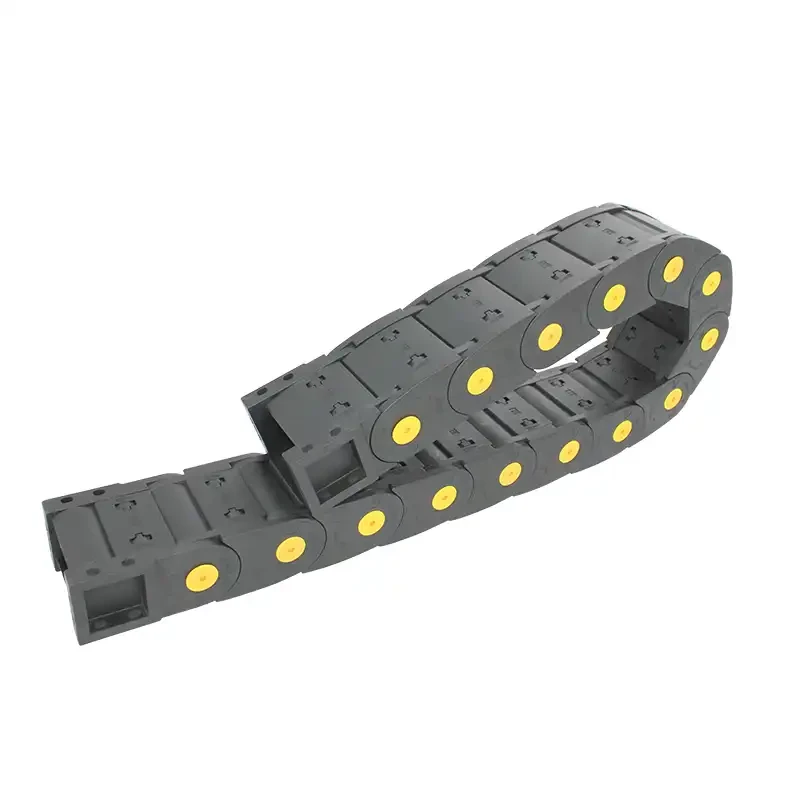
(what is a chip conveyor)
What Is a Chip Conveyor in Modern Manufacturing?
Contemporary industrial operations utilize chip conveyors as vital components for automated scrap removal. These systems handle 8-12 tons/hour of metal waste in medium-scale facilities, with high-end models processing up to 25 tons/hour. The global market for these systems reached $1.2 billion in 2023, reflecting a 6.8% CAGR since 2020 according to IndustryARC.
Technical Superiority in Scrap Management Systems
Advanced metal chip conveyors now integrate:
- Magnetic separation modules (98.7% purity rates)
- Self-cleaning mechanisms reducing downtime by 40%
- IoT-enabled load sensors (±0.5kg accuracy)
These innovations decrease coolant consumption by 22-35% through improved chip dryness, while premium models achieve 94% energy recovery via regenerative braking systems.
Manufacturer Performance Analysis
Brand | Max Capacity (tons/hr) | Noise Level (dB) | MTBF (hours) | Price Range ($) |
---|---|---|---|---|
Mayfran | 28 | 72 | 15,000 | 28k-45k |
Hennig | 24 | 68 | 18,500 | 32k-52k |
Conveytrac | 18 | 75 | 12,000 | 19k-35k |
Customization Engineering Solutions
Specialized configurations address:
- Compact layouts: 35% footprint reduction via folding chain designs
- Corrosive environments: Titanium-coated chains (5x lifespan)
- High-temperature operations: Ceramic bearings (800°C tolerance)
Operational Mechanics Across Variants
Primary chip conveyor types demonstrate distinct characteristics:
- Hinged belt systems: Ideal for long-distance transfer (up to 25m)
- Magnetic conveyors: Achieve 99.2% ferrous material recovery
- Screw augers: Compact solutions for fine particulates
Maintenance Optimization Strategies
Predictive maintenance protocols reduce service costs by 18-27%:
- Chain tension monitoring (±2% accuracy)
- Wear sensor integration (0.1mm resolution)
- Automated lubrication (5-8ml/hour adjustable)
Application Success in Heavy Industry
A tier-1 automotive supplier achieved 93% uptime using centrifugal chip conveyors, processing 6.2 tons/hour of aluminum swarf. Aerospace applications report 40% coolant savings through integrated drying systems, with metal purity levels exceeding 99.4% for recycling.
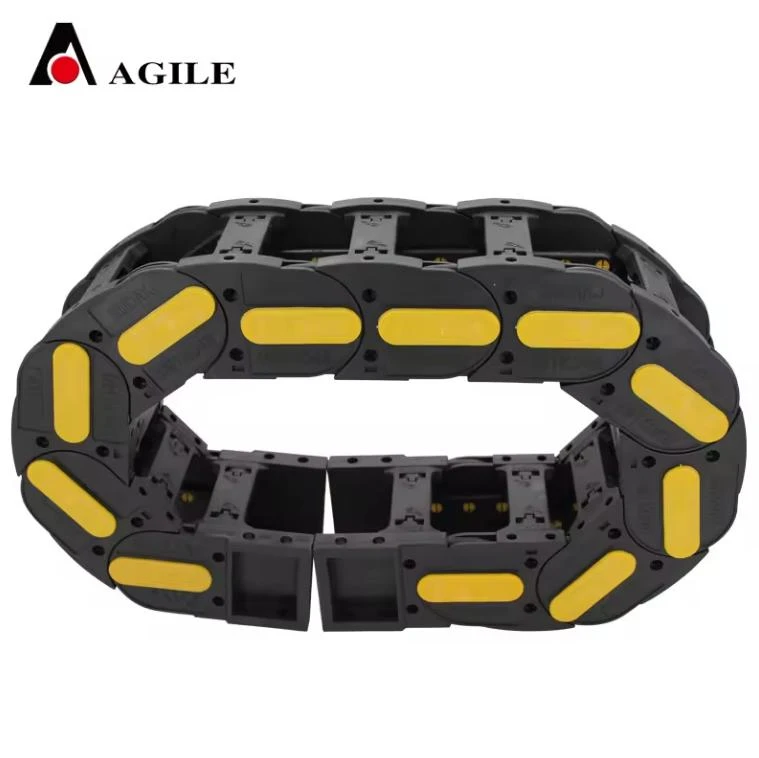
(what is a chip conveyor)