Understanding the Importance of Lathe Bellow Covers for Equipment Protection and Performance Enhancement
Understanding Lathe Bellow Covers Importance and Applications
Lathe bellow covers, often referred to simply as bellows, play a crucial role in the maintenance and efficiency of various mechanical systems. These flexible enclosures are primarily used to shield lathe machinery from contaminants, debris, and wear caused by repeated motion. As machinery operates, particularly in industries like manufacturing and metalworking, they are exposed to dust, chips, coolants, and other environmental factors that could impede performance and damage components. This is where lathe bellow covers come into play.
What Are Lathe Bellow Covers?
Lathe bellow covers are protective coverings made from flexible materials, such as rubber, polyurethane, or fabric composites. They are designed to extend and contract in sync with the moving parts of a lathe, providing a seal that prevents the ingress of contaminants. The flexibility of bellows enables them to maintain their protective function without hindering the operation of the machinery. They come in various shapes and sizes, depending on the specific needs of the equipment they are protecting.
Importance of Lathe Bellow Covers
1. Protection from Contaminants The primary function of lathe bellow covers is to protect sensitive components from dirt, chips, and other abrasive materials. By creating a barrier, bellows prevent these contaminants from entering critical areas of the lathe, which can lead to premature wear or failure.
2. Enhanced Longevity of Machinery Regular exposure to contaminants can significantly shorten the lifespan of mechanical components. By using lathe bellow covers, businesses can reduce maintenance costs and downtime associated with repairs, ultimately enhancing the longevity of the machinery.
3. Improved Safety In industrial settings, flying debris can pose a safety risk to workers. Lathe bellow covers help contain this debris, minimizing the risk of injury from projectiles while also ensuring that the work environment remains clean and safe.
4. Reduced Maintenance Costs The investment in lathe bellow covers can lead to substantial savings in maintenance and repair costs over time. When components are protected, there's less risk of malfunction, which translates to fewer service interruptions and lower maintenance expenses.
Applications of Lathe Bellow Covers
Lathe bellow covers are utilized in a wide range of industries and applications, including
lathe bellow cover
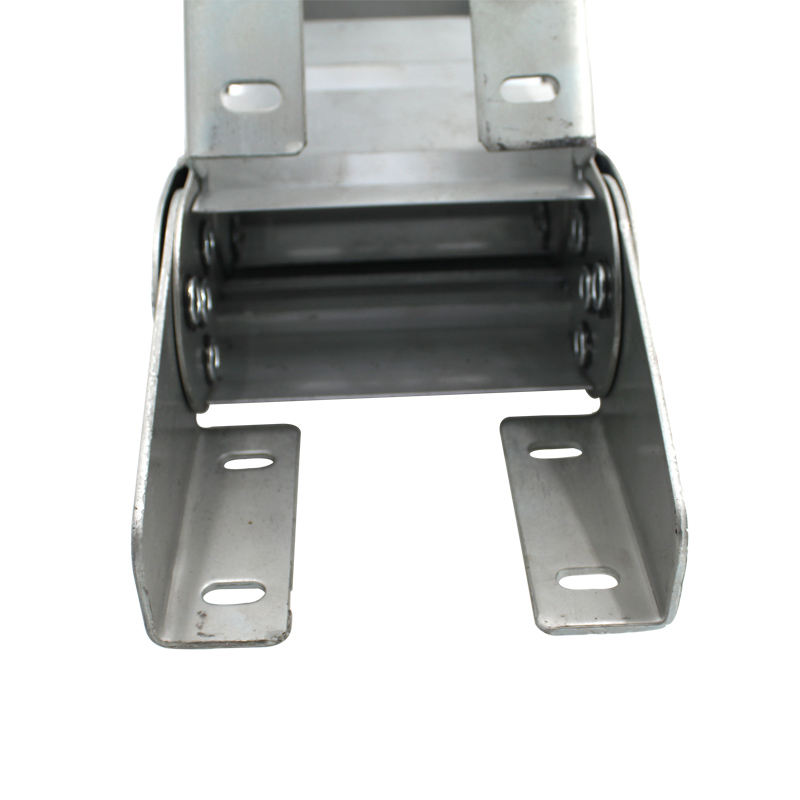
- Metalworking Shops They are commonly used in workshops that deal with milling and turning operations. Protecting critical machine parts ensures high precision and optimal performance.
- Automotive Manufacturing In the production of automotive parts, lathe bellow covers protect the machinery used in the creation of intricate and precise components.
- Aerospace Industry Given the high standards of precision and safety required in aerospace, bellows play a vital role in protecting the machinery that produces parts for flight.
- Robotics and Automation In automated systems, bellow covers help protect sensitive sensors and actuators, ensuring reliable operation in clean and controlled environments.
Choosing the Right Lathe Bellow Cover
When selecting lathe bellow covers, several factors should be considered
1. Material Depending on the application, different materials will offer varying levels of flexibility, temperature resistance, and durability.
2. Size and Shape Customization may be necessary to match the specific dimensions of the machinery being protected.
3. Environmental Factors Consider the operating environment, including exposure to chemicals, extreme temperatures, and humidity levels.
In conclusion, lathe bellow covers are essential components in maintaining the integrity and performance of machinery across various industries. By providing a robust barrier against contaminants and ensuring safety, they prove to be a wise investment for any automated or mechanical system. Understanding their importance and selecting the right type can significantly enhance operational efficiency and machine longevity.