Understanding the Functionality and Applications of Synchronous Belts in Mechanical Systems
What is a Synchronous Belt?
A synchronous belt, also known as a timing belt, is a type of drive belt used in various machinery and automotive applications to transmit power between rotating shafts with precision. Unlike traditional V-belts or flat belts, synchronous belts are designed with teeth along their inner surface, which interlock with the teeth on the corresponding pulleys. This interlocking mechanism allows for synchronous operation, where the rotation of one pulley drives the other in perfect time, thus maintaining a constant speed ratio.
Construction and Materials
The construction of a synchronous belt typically consists of a core material that provides tensile strength, reinforced with fibers such as glass or aramid to prevent elongation during operation. The outer surface is often made of durable rubber or polyurethane, which offers resistance to wear and environmental factors like oil, heat, and abrasives. The internal teeth are precisely molded to ensure compatibility with the matching pulley system, which can vary in pitch (distance between teeth) and profile (shape of teeth) based on specific applications.
Applications
Synchronous belts are widely used in automotive engines, where they connect the crankshaft to the camshaft, ensuring that the valves open and close at the correct times. This synchronization is crucial for the engine's operation, preventing misfires and maintaining optimal efficiency. Beyond automotive use, synchronous belts are also employed in various industrial applications, including automation systems, textile machinery, conveyor systems, and robotics. Their ability to maintain precise timing makes them ideal for applications where accurate positioning and speed control are essential.
Advantages
what is a synchronous belt
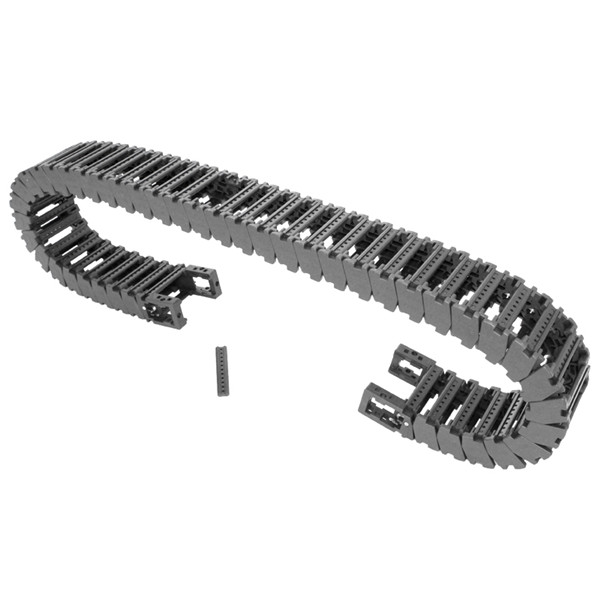
One of the primary advantages of using synchronous belts is their ability to provide a high level of accuracy and reliability. Because the teeth prevent slippage, synchronous belts transmit power more efficiently than traditional belts, which may experience slippage and require regular tension adjustments. This feature not only enhances performance but also prolongs the lifespan of the belt and the associated machinery.
Moreover, synchronous belts operate more quietly than chain drives, making them suitable for applications where noise reduction is critical. They are also lighter than many other power transmission systems, which can contribute to overall equipment efficiency. Additionally, synchronous belts require less maintenance compared to chains or other mechanical drive systems, as they do not need lubrication and have fewer wear points.
Disadvantages
While synchronous belts offer numerous advantages, they are not without disadvantages. One of the primary concerns is their sensitivity to misalignment. If the pulleys are not aligned correctly, it can lead to rapid wear and potential belt failure. Furthermore, if a synchronous belt is subjected to excessive loads, it may break or become damaged, necessitating immediate replacement. Regular inspection and proper alignment are crucial to mitigate these issues.
Conclusion
In summary, a synchronous belt is a vital component in many mechanical systems, providing efficient and reliable power transmission with precise synchronization. From automotive engines to industrial machinery, their robust design and engineering make them an essential choice for applications demanding high performance and minimal maintenance. Understanding their construction, advantages, and potential drawbacks can help users make informed decisions when selecting the appropriate drive system for their needs.