Understanding the Functionality and Applications of Synchronous Belt Pulleys in Mechanical Systems
The Importance of Synchronous Belt Pulleys in Mechanical Systems
Synchronous belt pulleys play a critical role in the world of mechanical engineering and motion transmission. They are essential components in various machines and devices, where precise timing and synchronization are paramount. This article delves into the functionality, advantages, applications, and maintenance related to synchronous belt pulleys.
Understanding Synchronous Belt Pulleys
A synchronous belt pulley is designed to work with a synchronous belt, which features teeth that mesh with corresponding grooves on the pulley. This interlocking mechanism prevents slippage, ensuring that the belt and the pulley rotate at the same speed. Synchronous belts are typically made from materials like rubber or polyurethane, and the pulleys are crafted from durable metals or engineered plastics to withstand wear and stress.
The design of synchronous belt pulleys allows for efficient power transmission with minimal energy loss. Unlike traditional V-belts, which can slip and create tension variations, synchronous belts provide a fixed ratio between the driver (the pulley connected to the power source) and the driven (the pulley that transmits motion) components. This fixed ratio is critical in applications where precise positioning and timing are required.
Advantages of Using Synchronous Belt Pulleys
1. High Efficiency Synchronous belt systems boast high mechanical efficiency, often exceeding 90%. This efficiency reduces the energy required for operation, which is economical in both energy consumption and operational costs.
2. Reduced Maintenance Unlike chain drives, which require regular lubrication and tension adjustments, synchronous belts operate quietly and require minimal maintenance. This feature is particularly advantageous in environments where maintenance access is limited or where downtime needs to be minimized.
3. Accurate Timing The design of the synchronous belt and pulley system allows for precise timing between components, making them ideal for applications such as robotics, CNC machinery, and conveyor systems.
4. Longevity Synchronous belts can withstand considerable wear and tear, and when properly installed and maintained, they can last for many years. This durability contributes to lower replacement costs and improved uptime for equipment.
synchronous belt pulley
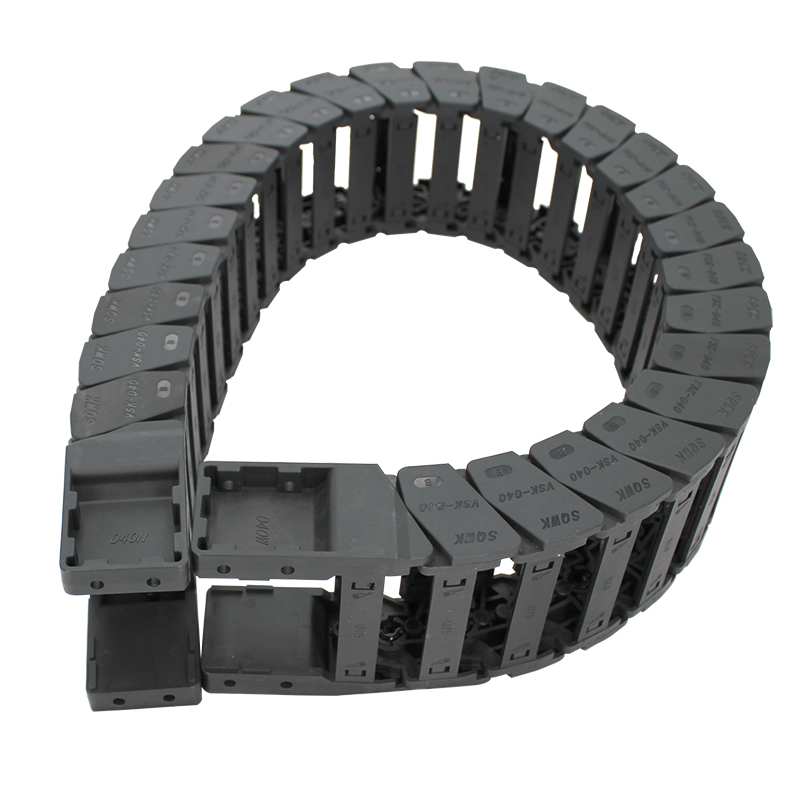
Applications of Synchronous Belt Pulleys
Synchronous belt pulleys are utilized in a myriad of applications across different industries. Some common use cases include
- Automotive Engines Synchronous belts are often used in camshaft drives to ensure that the engine's timing remains accurate, preventing significant engine damage. - Industrial Machinery Many manufacturing processes rely on synchronous belt drives for conveyor systems and equipment that require synchronized movements, such as printing presses and packaging machines.
- Robotics In robotic systems, synchronous belt pulleys provide exact positioning necessary for precise movements, making them integral to robotics applications.
- HVAC Systems Synchronous belts can also be found in heating, ventilation, and air conditioning systems, where they facilitate the movement of fans and other components.
Maintenance and Best Practices
While synchronous belt pulleys require less maintenance than many other mechanical components, it is still crucial to perform regular inspections and follow best practices. Regular checks should include
- Alignment Ensuring that pulleys are correctly aligned to avoid premature wear and tear. - Tension Monitoring belt tension is vital to maintain performance and prevent slippage or failure. - Wear Inspection Regularly examining both the belt and pulley for signs of wear can help prevent unexpected breakdowns.
Conclusion
Synchronous belt pulleys represent a vital aspect of modern mechanical systems, contributing to efficient, reliable, and precise power transmission. Their applications across diverse industries underscore their significance in engineering design. By understanding their function, advantages, and maintenance needs, engineers and mechanics can ensure optimal performance in the systems they help to create and maintain.