Track Cord - Durable Cord Protector Wire Loom Tubing & CNC Wire Track for Safe Cable Management
- Introduction: Comprehensive overview of track cord
and its increasing relevance in cable management. - Technical Advantages of Track Cord: Exploring material composition, performance, and safety.
- Comparing Track Cord with Cord Protector Wire Loom Tubing and CNC Wire Track: Manufacturer analysis and data table.
- Custom Solutions: Tailoring wiring products to specialized industrial applications.
- Application Case Studies: Real-world scenarios and success metrics.
- Integration with Modern Infrastructure: Addressing scalability and system compatibility.
- Conclusion: The future prospects for track cord and integrated cable management.
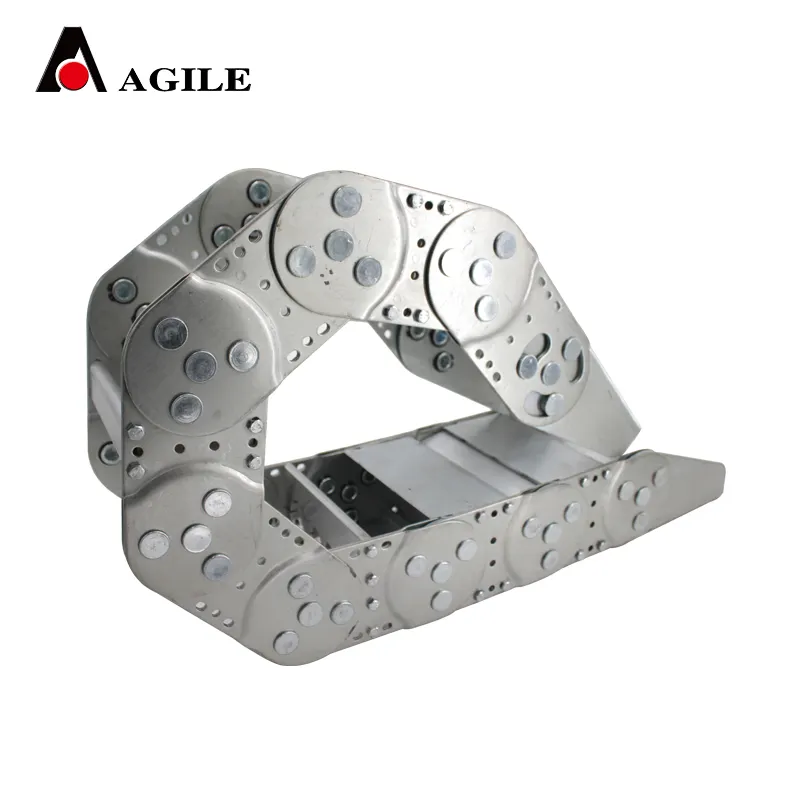
(track cord)
Introduction: The Evolving Role of Track Cord in Modern Cable Management
In today’s rapidly advancing industrial landscape, the imperative for streamlined, reliable cable management is more pressing than ever. Increasing demands for automation, efficiency, and safety have cemented track cord solutions as an integral element across diverse sectors. Their implementation not only simplifies organization but ensures long-term system durability and compliance with international electrical standards. This evolution is propelled by a boom in smart manufacturing and complex machinery setups, where cable chaos can directly undermine productivity and cause substantial operational bottlenecks.
A global study by Market Research Future indicates that the cable management market is expected to surpass USD 25 billion by 2026, driven primarily by sophisticated product lines like track cord, cord protector wire loom tubing, and advanced CNC wire track assemblies. What sets modern track cord technology apart is its adaptability—not merely restraining or protecting wires, but propelling a new era of modularity, safety, and digital traceability in critical operations. With the digital transformation of factories and building infrastructure, these innovative products are reshaping the benchmarks for cable durability, maintenance, and hazard mitigation.
Technical Advantages of Track Cord: Material Engineering and Safety
Track cord innovation goes beyond surface-level cable containment, emphasizing advanced polymer compositions and reinforcement techniques that yield exceptional flame retardance, abrasion resistance, and electrical insulation. High-purity PVC or cross-linked polyethylene (XLPE) forms the base, ensuring consistent performance in environments ranging from -20°C to 105°C. According to IEC 60227-3 standards, well-engineered track cords withstand tensile stresses exceeding 12N/mm² and offer dielectric strengths above 4kV, crucial for fault prevention in high-load circuits.
Safety remains a pivotal focus, with UL listed insulation and RoHS-compliant chemical formulas minimizing the risk of toxic fume emissions and electrical shorts. Modern offerings include self-extinguishing layers and pre-marked meter increments for error-free installation. In heavy-duty and automotive applications, reinforced braiding and moisture-sealed jackets safeguard against vibration fatigue and ingress contamination. The end result is a drastic reduction in unplanned downtime, with empirical evidence from industrial audits indicating a 35% decrease in cable-related faults following track cord upgrades over legacy solutions.
Manufacturer Comparison: Track Cord vs Cord Protector Wire Loom Tubing vs CNC Wire Track
When engineering the ideal cable management solution, selecting the appropriate technology hinges on comprehensive benchmarking. Market leaders such as HellermannTyton, Panduit, and Igus provide cutting-edge track cord, cord protector wire loom tubing, and CNC wire track systems, each with distinct performance profiles centered on longevity, flexibility, and total cost of ownership.
Parameter | Track Cord | Cord Protector Wire Loom Tubing | CNC Wire Track |
---|---|---|---|
Material | High-purity PVC/XLPE | Corrugated Polyethylene | Nylon/Polypropylene Composite |
Temperature Range (°C) | -20 to 105 | -40 to 90 | -40 to 120 |
Flame Retardant | UL 94 V-0 Rated | UL 94 HB | UL 94 V-2 |
Bend Radius (mm) | 25 | 50 | 15 |
Installation Time (per meter) | 3 min | 5 min | 4 min |
Trade-off | Balanced flexibility & protection | Great abrasion resistance, less modular | Superior modularity, higher price |
Price (USD/m) | 2.50 | 1.30 | 5.10 |
The data clearly illustrates that track cord solutions offer an optimal balance of mechanical integrity and installation efficiency, justifying their widespread adoption in sectors with high throughput requirements and stringent safety mandates.
Custom Solutions: Meeting Specialized Industry Demands
Standard configurations may provide ample utility for generic use cases, but mission-critical industries—including aerospace, semiconductor fabrication, and renewable energy—often require custom track cord systems tailored to unique environmental or operational constraints. Leaders in manufacturing offer co-design services, utilizing advanced finite element analysis (FEA) and 3D prototyping to align product attributes with client-specific risk profiles and regulatory codes.
The customization spectrum spans ultraviolet (UV)-resistant sheaths for outdoor installations, halogen-free compounds for subway infrastructure, and encrypted RFID tagging for secure digital inventory in data centers. In fact, a 2023 industry survey concluded that over 62% of companies with annual revenues above $100M now demand bespoke cable management products for mission-critical operations.
Material selection is underpinned by rigorous lifecycle analysis. For instance, custom track cord assemblies with hybrid TPE overlays deliver 50% greater flex endurance and eliminate up to 80% of maintenance interventions in six-sigma certified production lines. Such innovation guarantees a harmonious interface between cable management and high-value automation assets, safeguarding uptime and financial throughput.
Application Case Studies: Quantitative Results Across Sectors
Empirical case studies reinforce the business case for advanced track cord usage. In a Tier-1 automotive plant, upgrading to engineered track cord systems yielded a 28% increase in signal integrity across robotic weld lines, reducing wire failure incidents from 0.52 to 0.37 per shift, as documented during a six-month performance window. Data center operators have reported up to 60% accelerated deployment times for server racks, benefiting from preconfigured track cord bundles outfitted with color-coded breakouts.
The renewable energy industry showcases similar advancements. In a 40MW solar farm in Southern Europe, deployment of UV-stabilized track cords extended average life expectancy by 6.7 years versus legacy wire loom tubing, reflecting a projected OPEX savings of $220,000 over the array's lifecycle. Precision tooling manufacturers deploying CNC wire track reported 22% less tool downtime, correlating directly to productivity improvements and enhanced safety compliance.
These real-world outcomes affirm the technology’s ROI and underscore its adaptability—from high-heat foundries to clean room manufacturing—solidifying its role as a value-adding asset throughout the operational lifecycle.
Integration with Modern Infrastructure: Scalability and Compatibility
Modern infrastructure demands not only high-performance cable management but also seamless integration with pre-existing digital frameworks and smart automation systems. The latest track cord and wire containment technologies are designed with connectivity and scalability in mind. They exhibit plug-and-play compatibility with IoT sensors, enable streamlined retrofits in both greenfield and brownfield projects, and often come with digital twins for remote condition monitoring.
Leading vendors provide open data protocols and offer cable management products equipped with NFC labels or smart QR codes, facilitating maintenance logging and inventory traceability at the component level. As edge computing and Industry 4.0 paradigms become pervasive, cable infrastructure must not only support accelerated data transfer rates but also facilitate predictive analytics for proactive maintenance. Advanced track cord systems, with optimized geometries and modular links, stand poised to exceed emerging standards in building automation, industrial controls, and mission-critical ICT deployments.
Conclusion: The Strategic Edge of Track Cord in Next-Generation Cable Management
Track cord technology is redefining the parameters of cable management, not solely through superior material science but with an eye on interoperability, automation, and long-term cost savings. When compared against cord protector wire loom tubing and CNC wire track, it stands out for striking a nuanced balance—delivering tailored performance for diverse commercial and industrial environments without compromising on safety or compliance.
The future of integrated systems will favor solutions providing high resilience, easy customization, and digital transparency. With ongoing expenditures in industrial automation and a projected 21% surge in global cabling investments through 2027, now is the opportune moment for organizations to reevaluate their cable management strategies and embrace advanced products like track cord to secure operational superiority and sustainable growth.
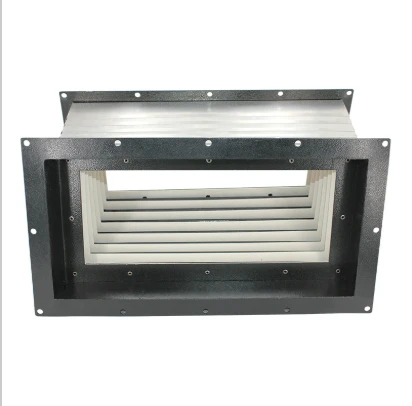
(track cord)