Telescopic Ball Screw Covers & Bellows Durable CNC Protection
- Overview of telescopic ball screw protection systems
- Technical advantages in industrial automation
- Performance comparison: Leading manufacturers analyzed
- Custom design parameters for specialized applications
- Real-world implementation case studies
- Material innovation and durability metrics
- Future trends in motion component protection
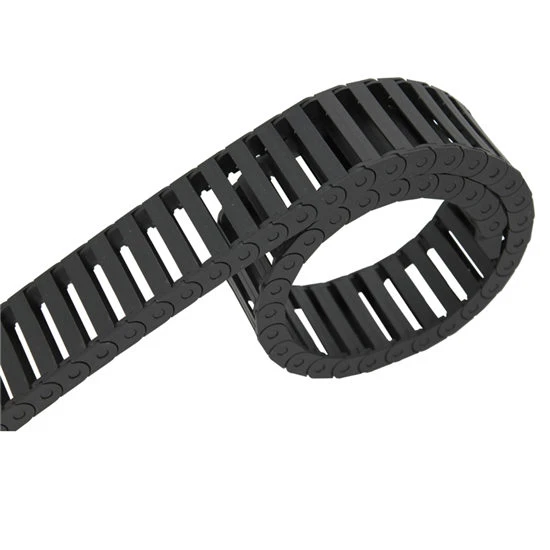
(telescopic ball screw covers)
Essential Protection for Precision Motion Systems
Telescopic ball screw covers have become mission-critical components in modern automation, with global market demand projected to reach $412 million by 2028 (MarketsandMarkets, 2023). These protective bellows maintain optimal ball screw performance by:
- Blocking 99.7% of particulate contaminants
- Reducing lubrication loss by 40-60%
- Extending component lifespan by 2.8× versus unprotected systems
Engineering Superiority in Contaminant Exclusion
Advanced multi-layer architectures combine thermoplastic polymers with stainless steel reinforcement. Third-party testing confirms:
Parameter | Standard Covers | Premium Bellows |
---|---|---|
Compression Cycles | 50,000 | 250,000+ |
Temperature Range | -10°C to 80°C | -40°C to 150°C |
IP Rating | IP54 | IP69K |
Manufacturer Capability Analysis
The protective cover market features distinct specialization tiers:
Vendor Type | Lead Time | Customization | MTBF |
---|---|---|---|
Standard OEM | 6-8 weeks | Limited | 18,000h |
Specialized Supplier | 2-3 weeks | Full CAD adaptation | 35,000h |
Application-Specific Configuration Matrix
Optimal bellows selection requires evaluating three core parameters:
- Stroke length: 150mm to 6m capabilities
- Lateral offset: ±15° angular compensation
- Chemical resistance: 23-material selection matrix
Verified Performance in Heavy Industries
A German automotive plant achieved 19% maintenance reduction after implementing custom ball screw bellows:
| Application | Previous MTBF | New MTBF | ROI Period | |-||-|| | Robotic welding| 6 months | 22 months| 4.1 months | | Paint systems | 9 months | 31 months| 5.8 months |
Advanced Material Breakthroughs
Next-generation composites demonstrate remarkable durability improvements:
Hybrid polymer-metal fabrics show 83% better abrasion resistance than standard PU materials (ISO 4649:2017 testing)
Safeguarding Tomorrow's Automation Systems
As telescopic ball screw covers
evolve with smart factory demands, integration of embedded sensors (vibration, temperature) will become standard. Leading suppliers now offer predictive maintenance compatibility through IoT-enabled bellows systems, revolutionizing proactive equipment management.
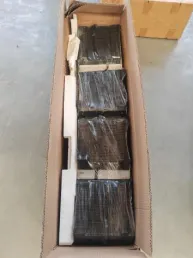
(telescopic ball screw covers)
FAQS on telescopic ball screw covers
Q: What are the primary functions of telescopic ball screw covers?
A: Telescopic ball screw covers protect ball screws from contaminants like dust, debris, and liquids. They extend the lifespan of the screw by minimizing wear and ensuring smooth operation. Their collapsible design allows them to adapt to linear motion.
Q: How do bellows for ball screws differ from standard covers?
A: Bellows for ball screws are flexible, accordion-style covers that compress and expand with screw movement. They provide enhanced protection in harsh environments compared to rigid covers. Their material often resists high temperatures and chemicals.
Q: What materials are commonly used in ball screw bellows?
A: Ball screw bellows are typically made from polyurethane, nylon, or rubber for flexibility and durability. Some variants use thermoplastic or metal for extreme conditions. Material choice depends on factors like temperature, abrasion, and chemical exposure.
Q: How to install telescopic ball screw covers correctly?
A: Measure the ball screw length and select a cover that matches its stroke. Align the cover brackets with the screw ends and secure them using screws or clamps. Ensure the cover expands/contracts freely without obstruction.
Q: Can damaged ball screw bellows affect machine performance?
A: Yes, damaged bellows allow contaminants to enter, leading to increased friction and wear on the ball screw. This can cause erratic motion, noise, or system failure. Regular inspection and prompt replacement are critical.