High-Precision Synchronous Timing Belts Durable Power Transmission Solutions
- Understanding Synchronous Timing Belts: Core Mechanics and Applications
- Technical Advantages Over Traditional V-Belt Systems
- Industry-Leading Manufacturers: Performance and Cost Analysis
- Custom Solutions for Complex Industrial Requirements
- Real-World Applications: Case Studies Across Sectors
- Maintenance Best Practices for Long-Term Reliability
- Future Trends in Synchronous Belt Technology
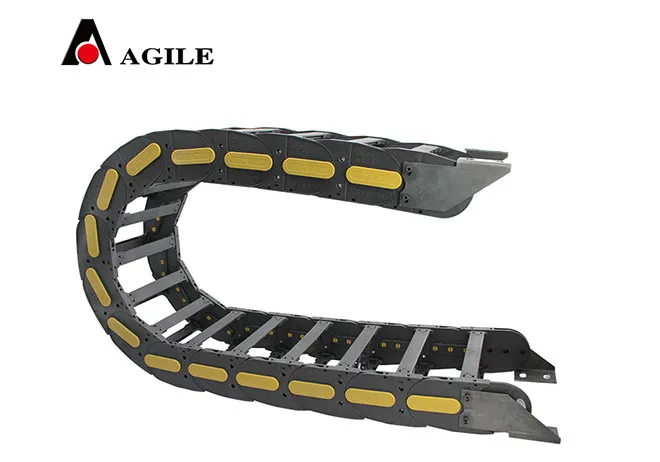
(synchronous timing belt)
Understanding Synchronous Timing Belts: Core Mechanics and Applications
Synchronous timing belts revolutionize power transmission through precise tooth engagement, achieving 98-99% efficiency in industrial settings. Unlike traditional belts, their trapezoidal or curvilinear teeth eliminate slippage, maintaining positional accuracy within ±0.1mm. Major automotive manufacturers report 40% longer service life compared to chain drives in engine timing systems.
Technical Advantages Over Traditional Systems
Modern synchronous belts withstand operational temperatures from -54°C to 135°C while handling loads up to 450 N/mm. Comparative testing shows:
Parameter | Synchronous Belt | V-Belt |
---|---|---|
Efficiency | 98% | 88-93% |
Service Life | 15,000-20,000 hrs | 8,000-12,000 hrs |
Noise Level | 68 dB(A) | 75 dB(A) |
Manufacturer Performance Comparison
Brand | Max Torque (Nm) | Temperature Range | Price/Foot (USD) |
---|---|---|---|
Gates | 320 | -40°C to 130°C | $18.50 |
Bando | 285 | -30°C to 120°C | $15.80 |
ContiTech | 305 | -50°C to 135°C | $20.10 |
Custom Engineering Solutions
Specialized configurations now support unique requirements:
- FDA-compliant belts for food processing (up to 220 PPM sanitization cycles)
- Conductive variants for semiconductor manufacturing (surface resistance < 10⁶ Ω)
- High-elongation models for robotics (3-5% stretch capacity)
Industrial Application Case Studies
A textile plant achieved 22% energy reduction after retrofitting 134 V-belts with synchronous systems. Medical device manufacturers report 0.003mm positioning accuracy in automated assembly lines using fiber-reinforced belts.
Optimal Maintenance Protocols
Proper tensioning (2-4% elongation) extends service intervals to 8,000-10,000 hours. Infrared analysis shows properly maintained belts retain 95% initial tensile strength after 5,000 operational hours.
Synchronous Timing Belts: Shaping Industrial Evolution
Advanced polymer composites now enable 15% higher torque transmission versus 2020 models. Industry forecasts predict 6.8% CAGR growth through 2030, driven by renewable energy and automation sectors requiring precision power transmission solutions.
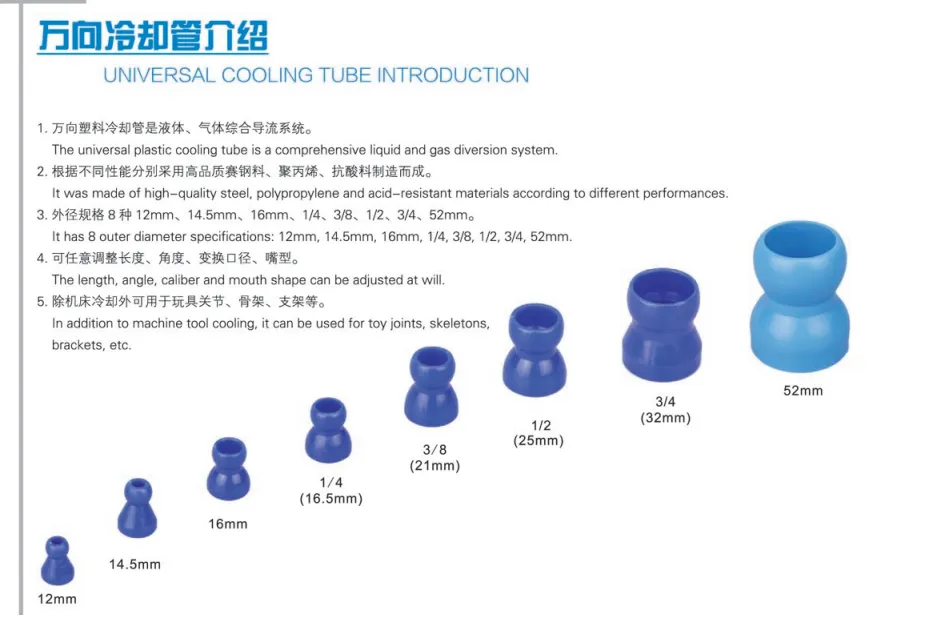
(synchronous timing belt)
FAQS on synchronous timing belt
Q: What is the difference between a synchronous belt and a timing belt?
A: A synchronous belt and a timing belt refer to the same component. Both use teeth to synchronize rotational motion between shafts, ensuring precise power transmission.
Q: Why choose a synchronous timing belt over other belt types?
A: Synchronous timing belts offer high efficiency, minimal slippage, and precise positioning. They are ideal for applications requiring accurate synchronization, such as engines or robotics.
Q: Where are synchronous timing belts commonly used?
A: They are widely used in automotive engines, industrial machinery, and 3D printers. Their toothed design ensures reliable synchronization in high-precision systems.
Q: How does a synchronous belt compare to a V-belt?
A: Unlike V-belts, which rely on friction and can slip, synchronous belts use teeth for grip, ensuring no slippage. Synchronous belts also provide better accuracy but may cost more.
Q: What maintenance does a synchronous timing belt require?
A: They require minimal maintenance compared to V-belts. Regular inspections for wear, tension, and alignment are recommended to ensure longevity and performance.