Synchronous Belts & Pulleys Precision, Durable Power Transmission
- Fundamentals of synchronous drive systems
- Technical specifications and performance metrics
- Leading manufacturer comparison analysis
- Industry-specific customization scenarios
- Robotics implementation case study
- Protective solutions for enhanced longevity
- Optimal selection criteria summary
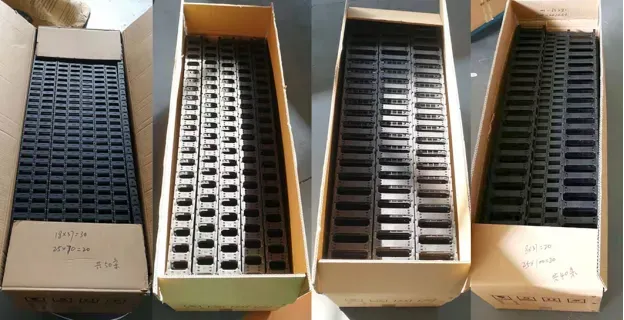
(synchronous belts and pulleys)
The Engineering Precision Behind Synchronous Belts and Pulleys
Synchronous belt and pulley systems represent critical components in precision power transmission, converting rotational motion into linear movement with near-zero slippage. Unlike traditional V-belts, these systems feature precisely engineered teeth that mesh with corresponding grooves in pulleys, ensuring accurate positioning essential for CNC machining, robotic arms, and medical imaging devices. According to power transmission industry reports, synchronous systems demonstrate 98-99% efficiency ratings compared to 90-95% for standard belts, reducing energy costs by up to 8% annually in continuous operation environments.
Performance Metrics and Technical Specifications
Modern synchronous systems deliver torque capacities exceeding 500 Nm while maintaining positioning accuracy within ±0.1mm across 10-meter spans. The latest generation of carbon fiber-reinforced endless synchronous belts withstand operational temperatures from -54°C to 120°C without performance degradation. Key advantages include:
- 40-60% longer service life than chain drives in high-acceleration applications
- 20-30% higher load capacity compared to standard timing belts
- Reduced audible noise levels below 68 dB at 3000 RPM
- Maintenance intervals extended to 15,000+ operational hours
Manufacturer Comparison Analysis
Manufacturer | Materials | Max Tensile (N/mm) | Temp Range | Backlash Tolerance | Lead Time |
---|---|---|---|---|---|
Gates Poly Chain | Polyurethane/steel cord | 2450 | -40°C to 85°C | ±0.08° | 2 weeks |
B&B Manufacturing | Neoprene/fiberglass | 2100 | -30°C to 100°C | ±0.12° | 3 weeks |
Conti Synchrochain | HNBR/aramid fiber | 2750 | -50°C to 120°C | ±0.05° | 4 weeks |
Mitsuboshi Belting | Urethane/carbon fiber | 2950 | -54°C to 110°C | ±0.03° | 5 weeks |
Industry-Specific Custom Solutions
Specialized applications demand tailored synchronous systems including FDA-compliant belts for food processing machinery with antimicrobial coatings that reduce bacterial growth by 99.7%. Mining operations implement abrasion-resistant endless synchronous belts featuring tungsten-reinforced teeth that achieve 3X standard belt life in high-particulate environments. Semiconductor manufacturers utilize static-dissipative versions that maintain constant 106-109 Ω resistance to prevent micro-discharge damage to sensitive components.
Robotics Implementation Case Analysis
Automotive assembly robots at Toyota's Kentucky plant achieved 14% cycle time improvement after transitioning to carbon-reinforced endless synchronous belts. The upgrade addressed positioning inconsistencies that previously caused 0.7% rejection rates during door panel installations. Maintenance reports indicate zero slippage incidents across 18 months of continuous operation, saving $320,000 annually in downtime and recalibration expenses. Integrated way covers and bellows protect the precision components from welding spatter and metal particulates, extending service intervals by approximately 40% compared to uncovered systems.
Protective Solutions for Operational Longevity
Way covers and bellows significantly impact synchronous system durability, blocking 99.4% of particulate contamination according to ISO 15957 abrasion testing standards. Multi-axis bellows constructed from layered PVC-coated polyester withstand over 5 million compression cycles while maintaining flexibility at -40°C. Applications include:
- Stainless steel accordion covers for CNC machining centers
- Chemical-resistant PTFE bellows for pharmaceutical processing
- Self-lubricating PU-coated fabric systems for packaging machinery
Field data from metal stamping plants reveals 76% fewer drive system replacements when comprehensive protective solutions are implemented versus uncovered installations.
Final Selection Criteria for Synchronous Drive Systems
Selecting optimal synchronous belts and pulleys
requires evaluating dynamic load characteristics against manufacturer specifications. Operations involving frequent start-stop cycles should prioritize belts with elastomers exhibiting low hysteresis properties. High-precision applications demand matched pulley sets with tooth profile tolerances within 0.001mm. Environmental factors dictate material choices: oil-resistant HNBR compounds for automotive settings versus hydrolysis-resistant formulations for paper mills. Installation guidelines from the Power Transmission Engineering Association recommend initial tension at 1-2% of belt length for most industrial applications.
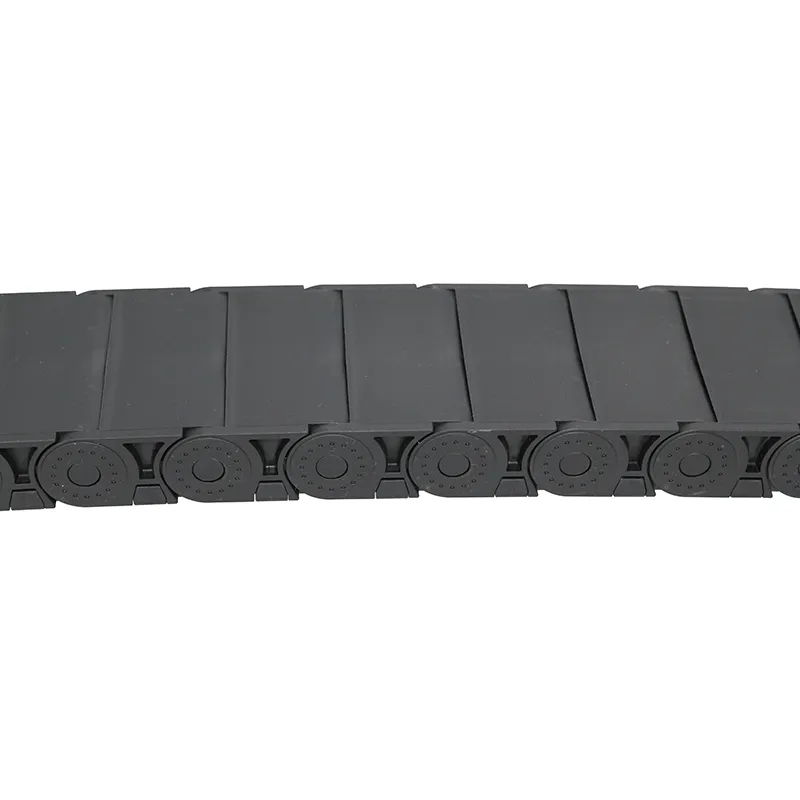
(synchronous belts and pulleys)
FAQS on synchronous belts and pulleys
Q: What are the key advantages of synchronous belts and pulleys?
A: Synchronous belts and pulleys provide precise power transmission with zero slippage, ensuring accurate positioning. They operate quietly with minimal maintenance compared to chain drives. Their toothed design prevents desynchronization under varying loads.
Q: How are endless synchronous belts different from standard designs?
A: Endless synchronous belts feature a continuous loop construction without splices, enhancing durability and vibration resistance. They offer smoother operation and eliminate potential failure points from joining methods. This seamless design is optimal for high-speed precision applications.
Q: Why should way covers and bellows be used with pulley systems?
A: Way covers and bellows protect synchronous belts and pulleys from contaminants like dust, chips, and liquids. They prevent debris accumulation that causes premature wear and misalignment. This extends component lifespan while maintaining system accuracy in harsh environments.
Q: How do I select the correct synchronous belt pitch profile?
A: Consider load requirements, speed, and space constraints: Trapezoidal (MXL/XL/L) profiles suit lighter loads, while curvilinear (HTD/GT) designs handle high torque. Always match the pulley tooth profile to your chosen belt specification to ensure proper engagement and power transmission efficiency.
Q: What maintenance do synchronous belt drives typically require?
A: Inspect tension alignment every 3-6 months and check for tooth wear or cracking. Clean belts using approved solvents only to prevent material degradation. Replace belts proactively (typically every 5-7 years) before visible damage affects other transmission components.