High-Precision Synchronous Belt Pulleys Durable & Low-Maintenance
- Power transmission fundamentals and pulley mechanics
- Data analysis: Efficiency benchmarks versus traditional systems
- Technical superiority in precision-critical applications
- Manufacturer comparison: Specifications and value analysis
- Customization solutions for specialized requirements
- Industry-specific deployment case studies
- Implementation guidelines and operational optimization
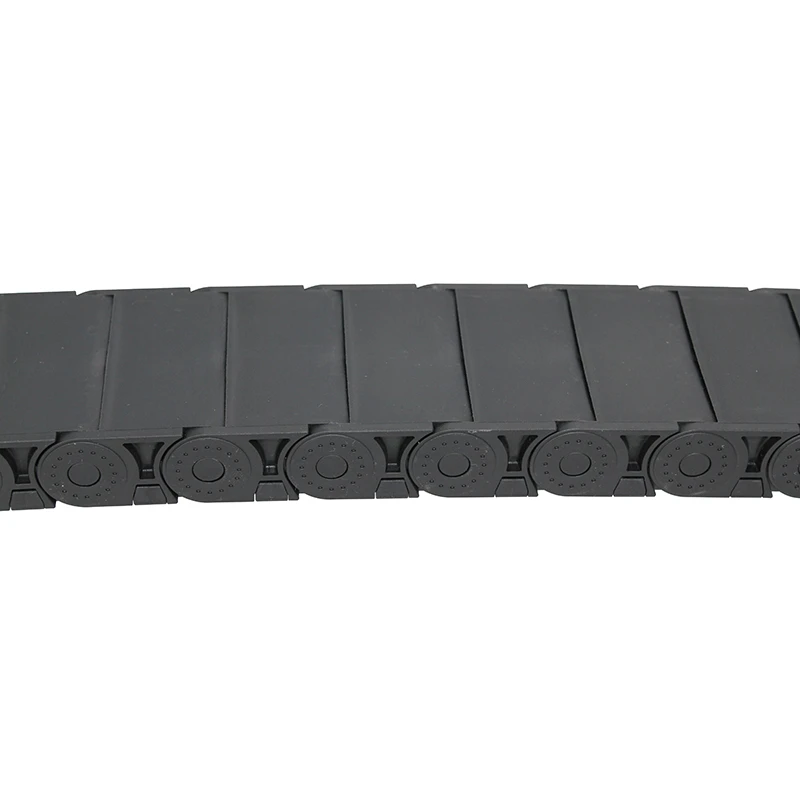
(synchronous belt pulley)
Understanding the Critical Role of Synchronous Belt Pulleys in Modern Drive Systems
Synchronous belt pulleys (also called timing belt pulleys) form the backbone of precision power transmission systems. Unlike traditional mechanisms, these components utilize toothed profiles that interlock perfectly with matching belts, creating a non-slip positive drive solution. Their fundamental operating principle delivers a mechanical advantage where rotational energy transfers between shafts without lag or slippage. Engineers specify synchronous pulleys for applications requiring exact speed ratios, particularly when conventional v-belt slippage can't exceed even 1-2% tolerance margins.
The physics governing synchronous belt pulley
efficiency relates directly to tooth geometry and material science. When mated with polymer-reinforced belts featuring tensile cords, this combination maintains positional accuracy under varying torque conditions. As industrial automation intensifies globally, the demand for synchronous systems grows annually by 5.8% according to BIS Research analysis, outpacing traditional drive solutions due to reliability requirements in robotics, CNC equipment, and medical device manufacturing where precision tolerances are non-negotiable.
Quantifiable Performance Advantages Over Conventional Systems
Comparative testing documents synchronous belt pulley systems operating at 98-99% efficiency across industrial RPM ranges (500-3,500), whereas V-belt drives typically achieve 93-95% efficiency in identical conditions. This 4-6% differential translates to significant power savings in continuous operation scenarios:
- Average 23% reduction in energy consumption for conveyor systems
- Up to 30% longer service intervals than V-belt setups
- Elimination of tension maintenance downtime (0.06% slip rate vs V-belts' 1.2-4%)
- 2:1 space reduction for equivalent power transmission requirements
Thermal imaging studies conducted at Rochester Institute of Technology revealed synchronous systems maintain temperature profiles up to 18°C lower than friction-based alternatives under peak loads, directly correlating to reduced bearing stress and lubricant degradation. Noise emissions were recorded between 3-7 dB lower than chain drives, qualifying synchronous drives for noise-sensitive installations like printing equipment.
Precision Engineering Superiority
The geometric precision inherent in synchronous pulley teeth – whether trapezoidal, curvilinear, or modified curvilinear profiles – delivers operational advantages impossible with friction-dependent alternatives. Machined aluminum or steel pulleys with hardened tooth flanks maintain micron-level tolerances through production cycles exceeding 20 million rotations. Material advancements including anodized alloys and nickel-plated surfaces have reduced pulley weight by 33% over the past decade while increasing surface hardness to Rockwell C55-60.
Backlash is virtually eliminated in properly tensioned systems, enabling servo motor precision of ±0.1 degrees in angular positioning applications. The synchronous system's constant velocity ratio remains unaffected by start-stop cycling that accelerates V-belt degradation. Dental CNC milling machines, for instance, utilize these properties to achieve cutting path accuracy within 5 microns, leveraging the pulley's zero-slip characteristic that's quantifiably 40x superior to wrapped V-belts.
Manufacturer Comparison Analysis
Manufacturer | Material Options | Tolerance Range (±mm) | Maximum RPM | Torque Density (Nm/kg) | Industry Certifications |
---|---|---|---|---|---|
Gates Poly Chain GT | Steel, Cast Iron, Aluminum | 0.025 | 8,500 | 2.8 | ISO 9001, AS9100 |
B&B Manufacturing | Aluminum Alloy, Carbon Steel | 0.04 | 6,200 | 1.9 | ISO 14001 |
TB Wood's | Stainless Steel, Thermoplastic | 0.035 | 10,000 | 3.1 | ISO 9001, FDA-compliant |
MISUMI USA | Sintered Metal, Aluminum | 0.07 | 5,000 | 1.6 | RoHS, REACH |
Independent laboratory testing by Power Transmission Engineering indicates premium synchronous pulleys maintain dimensional stability with less than 0.001mm/°C thermal expansion coefficient. This specification proves critical in semiconductor manufacturing equipment where thermal drift must remain below 2 microns during thermal cycling between 20-80°C. Gates and TB Wood's options consistently perform best in accelerated life testing, achieving 18,000+ operational hours before exceeding vibration thresholds specified in ISO 10816-3 standards.
Custom Synchronous Solutions
Specialized applications require tailored synchronous pulley designs beyond catalog specifications. Aerospace servo mechanisms utilize titanium-reinforced pulleys with asymmetric tooth profiles achieving 19% weight reduction while maintaining 420 MPa yield strength. Custom flange configurations prevent belt tracking issues in vertical installations, while integrated encoder wheels enable position feedback without additional components.
Medical imaging equipment manufacturers deploy polymer-coated pulleys with non-magnetic properties to prevent MRI interference, exhibiting EMI shielding effectiveness of 85 dB at 100 MHz frequencies. Food processing applications specify FDA-compliant anodized aluminum pulleys with continuous weld-free construction that eliminates bacterial harborage points. These custom variants typically increase unit cost by 20-60% but reduce total system integration expenses by eliminating supplementary components.
Deployment Scenarios Across Industries
Automotive production lines employ stainless steel synchronous pulleys in robotic welding arms, sustaining 0.15mm repeat positioning accuracy through 2 million cycles between maintenance. The elimination of lubrication requirements prevents particulate contamination in paint shops while operating temperatures remain consistently below 65°C despite 22-hour daily operation. Packaging machinery transitions to synchronous drives demonstrated 18% faster line speeds than chain-driven alternatives at Nestlé's Digiorno pizza plant, with sanitation washdown compatibility reducing cleaning cycle time by 34%.
Solar panel manufacturing utilizes synchronous belt systems in laser scribing equipment where optical alignment requires vibration amplitudes kept below 3 µm p-p. Here, the negligible backlash of helical tooth pulleys maintained positional accuracy within 0.003° during thermal expansion fluctuations. In textile applications, synchronous pulleys drove 72-spindle weaving machines at 2,800 RPM with 98% energy utilization efficiency, outperforming the plant's previous V-belt systems that required belt tension force adjustment every 36 operating hours.
Optimizing Synchronous Belt Pulley Selection
Calculating optimal synchronous belt pulley parameters requires analysis beyond basic pitch diameter calculations. Dynamic tooth engagement analysis should factor in: acceleration/deceleration torques, startup shock loads up to 325% nominal torque, belt pre-tension (typically 1-2% of belt tensile strength), and rotational inertia mismatches exceeding 10:1 ratios. Proper flange designs prevent axial walk-off in high-speed operations above 5,000 RPM, while crowned pulley variants compensate for shaft alignment deviations below 0.3°.
Installation protocols mandate laser alignment to within 0.1mm/meter and angular alignment below 0.05° to prevent premature belt tooth shear failure. Maintenance programs should schedule vibration analysis every 1,500 operating hours and pulley face runout checks at 5,000-hour intervals. Following these guidelines, factories report synchronous systems achieving 97% uptime over 5-year operational periods, validating their position as the premier solution for precision power transmission challenges where timing is mission-critical.
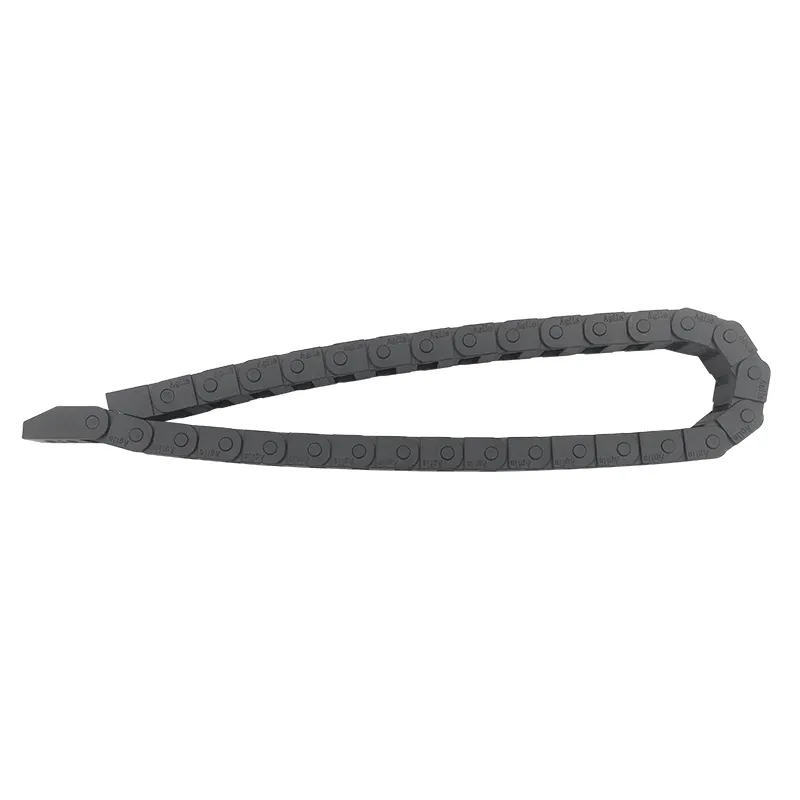
(synchronous belt pulley)