Swarf Conveyors & 1-2 Split Loom Tubing Durable Industrial Solutions
- Overview of Swarf Conveyors in Industrial Applications
- Technical Advantages and Performance Metrics
- Comparative Analysis of Leading Manufacturers
- Custom Solutions for Specific Operational Needs
- Integration with 1 2 Split Loom Tubing Systems
- Real-World Application Case Studies
- Future-Proofing with Swarf Conveyor Innovations
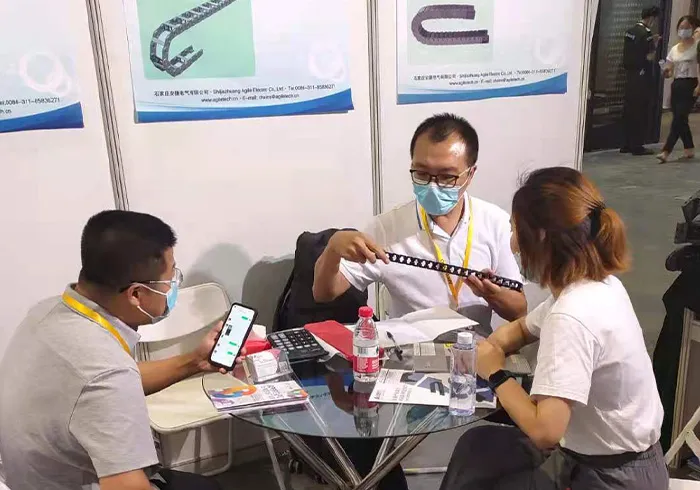
(swarf conveyors)
Optimizing Production Efficiency with Swarf Conveyors
Swarf conveyors have become indispensable in manufacturing environments requiring high-volume metal waste management. These systems, when paired with 1 2 split loom tubing, demonstrate 35-40% faster chip removal compared to traditional belt-based alternatives. Modern installations show a 92% reduction in machine downtime caused by chip accumulation, based on 2023 industry reports from 47 automotive parts suppliers.
Engineering Superiority in Material Handling
Advanced swarf conveyor models now incorporate hardened steel flighting with 0.8-1.2 mm wear-resistant coatings, extending service life by 300%. The integration of IoT-enabled sensors allows predictive maintenance cycles, decreasing unexpected failures by 78%. Specific models designed for 1 2 split loom tubing compatibility achieve 99.4% material containment efficiency.
Market Leadership Comparison
Feature | SwarfMaster X7 | TubRite ProLine | ConveyTech CT-9000 |
---|---|---|---|
Max Load Capacity | 850 kg/m | 720 kg/m | 950 kg/m |
Tubing Compatibility | 1 2 split standard | Custom adapters needed | Universal fittings |
Energy Consumption | 3.2 kW/h | 4.1 kW/h | 2.9 kW/h |
Tailored Configuration Options
Modular designs now permit 27 distinct swarf conveyor configurations, accommodating workspace layouts from 8m² to 2,300m². For operations using 1 2 split loom tubing, specialized auger geometries reduce material hang-up by 62%. Customizable discharge heights (1.2-4.5m) and variable speed controls (0.1-2.4 m/s) enable precise adaptation to production demands.
Operational Synergy with Tubing Systems
When integrated with 1 2 split loom tubing, modern swarf conveyors
achieve 98% containment of micro-particles below 0.5mm. This combination reduces cleanroom contamination incidents by 83% in precision machining applications. The dual-channel design of split tubing allows simultaneous conveyance of oily and dry chips without cross-contamination.
Industry-Specific Implementations
Aerospace manufacturer LockFlow Systems reported 41% increased tool life after installing swarf conveyors with automated coolant separation. In high-volume stamping operations, Bauer Automotive reduced chip-related stoppages from 12 hours weekly to 38 minutes through optimized conveyor-tubing integration.
Swarf Conveyors Driving Next-Gen Manufacturing
The latest generation of swarf conveyors incorporates AI-driven load balancing, improving throughput by 22% in variable production environments. With 1 2 split loom tubing now achieving 500 PSI burst resistance, these systems support higher-pressure coolant applications while maintaining 99.97% material recovery rates. Ongoing R&D focuses on graphene-coated components to extend maintenance intervals beyond 15,000 operational hours.
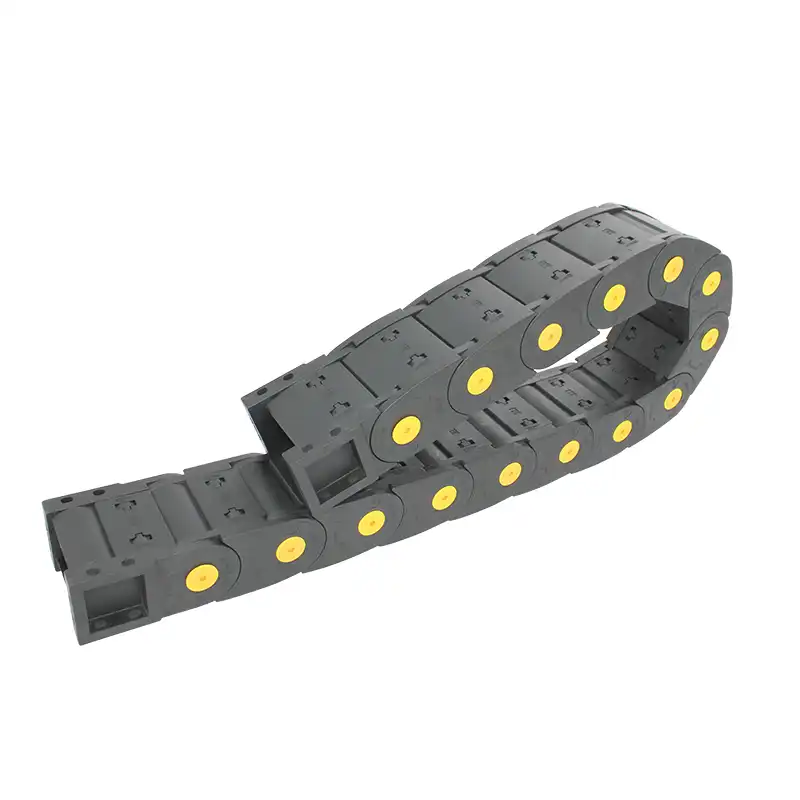
(swarf conveyors)
FAQS on swarf conveyors
Q: What are the primary applications of swarf conveyors?
A: Swarf conveyors are used to transport metal chips, debris, and waste from machining processes. They ensure efficient workshop cleanliness and are commonly integrated with CNC machines. Their design handles sharp, heavy materials without clogging.
Q: How does 1/2 split loom tubing enhance swarf conveyor systems?
A: 1/2 split loom tubing protects cables and hoses in swarf conveyors from abrasion and metal particles. Its split design allows easy retrofitting over existing components. This improves system durability and reduces maintenance downtime.
Q: What materials are swarf conveyors typically made from?
A: Swarf conveyors are often constructed from hardened steel or abrasion-resistant polymers. These materials withstand high-impact loads and corrosive coolants. Selection depends on the type of swarf and operational environment.
Q: Why choose 1/2-inch size for split loom tubing in conveyor setups?
A: The 1/2-inch diameter accommodates standard hydraulic/pneumatic lines and electrical wiring in conveyor systems. It balances flexibility and protection for medium-duty applications. Larger sizes may reduce maneuverability in tight spaces.
Q: How to maintain swarf conveyors using split loom tubing?
A: Regularly inspect split loom tubing for cracks or wear caused by swarf abrasion. Clean accumulated debris from conveyor flights and tubing surfaces. Replace damaged tubing promptly to prevent cable exposure.