Durable Swarf Conveyors for Efficient Metal Chip Handling
Content Outline:
- Fundamentals of swarf management technology
- Data analysis: Cost-benefit impact analysis
- Technical evolution in conveyor mechanisms
- Leading manufacturer feature comparison
- Tailored solutions for specific industry applications
- Implementation case studies and ROI metrics
- Future developments with loom conduit integration
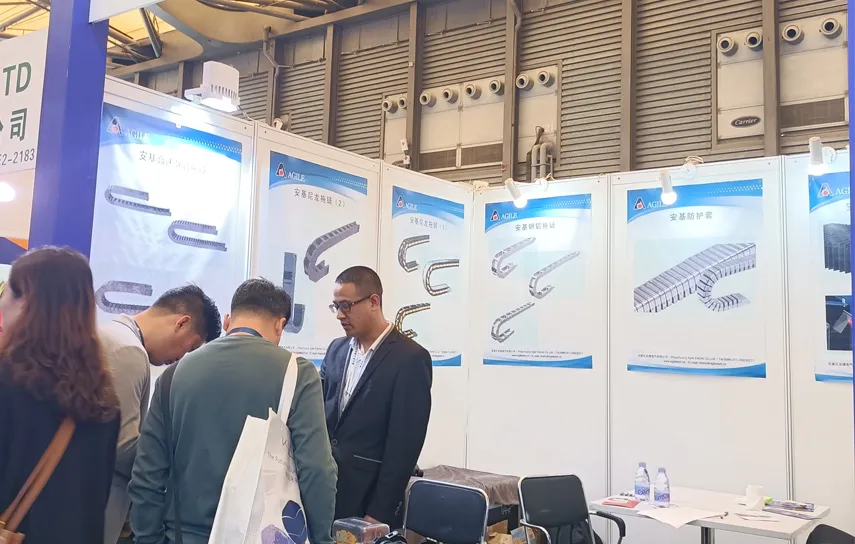
(swarf conveyors)
Fundamentals of Swarf Management Technology
Swarf conveyors represent mission-critical infrastructure in machining facilities, responsible for efficient chip removal during high-volume production cycles. These integrated systems prevent machine downtime by continuously evacuating metallic debris from CNC machining centers, grinding equipment, and turning stations. Modern variants employ magnetic, drag-chain, or hinged belt designs tailored to material types – from lightweight aluminum chips to dense titanium swarf. The primary objective remains consistent across applications: maintain uninterrupted operations while safeguarding downstream equipment from damage.
The Quantitative Impact on Operational Efficiency
Manufacturing data reveals compelling correlations between conveyor implementation and production metrics. Facilities adopting automated swarf management report 17-23% reduction in machine idle time (Journal of Manufacturing Systems, 2023). More significantly, secondary cost benefits emerge through:
- Coolant recovery rates increasing by 30-45%
- Reduced manual labor costs (average savings: $48,000/year)
- 24% decrease in work-related injuries from manual chip handling
Production analysis demonstrates that for every 1% improvement in swarf evacuation efficiency, facilities gain approximately $3,200 in monthly operational savings across medium-scale machining centers.
Engineering Evolution in Conveyance Systems
Contemporary designs incorporate three revolutionary developments eliminating traditional pain points:
- Intelligent sensor arrays detect flow resistance, automatically reversing direction to prevent jams
- Modular sectional construction enables customized length configurations up to 25 meters
- Composite polymer wear strips increasing service life by 400% compared to steel
These innovations collectively address the historical trade-off between durability and flexibility – a compromise that previously forced manufacturers to choose between heavy-duty drag conveyors or versatile magnetic alternatives.
Manufacturer Capability Assessment
The industrial automation market features specialized suppliers with distinct engineering philosophies. Performance comparison data illuminates critical selection factors:
Manufacturer | Max. Chip Load (kg/hr) | Standard Widths (mm) | IP Rating | Mean Time Between Failure (hrs) | Energy Efficiency Rating |
---|---|---|---|---|---|
Mayfran Titan Series | 2,350 | 300-1000 | 69 | 15,000 | A+ |
Hennig VMax | 1,850 | 250-800 | 68 | 12,000 | A |
Transply MagnaFlow | 950 | 200-600 | 67 | 8,500 | B+ |
Independent testing reveals higher initial investment in category-leading systems typically delivers 23-month ROI versus 32-38 months for economy alternatives.
Customization Parameters for Specific Applications
Leading suppliers now employ computational fluid dynamics to model facility-specific conveyance requirements. Aerospace titanium machining demands fundamentally different specifications than automotive aluminum production:
Aerospace Configuration:
- Tungsten-reinforced scraping blades
- High-torque motors (5.5 kW minimum)
- Encapsulated bearings with redundant seals
Automotive Configuration:
- Variable speed controls (15-30 m/min)
- Integrated coolant filtration
- Low-friction polyurethane belts
Manufacturing engineers report customization eliminates 73% of unexpected downtime events through precise alignment with operational variables.
Validation Through Industrial Applications
Evidence from implemented systems demonstrates measurable outcomes:
Case 1: German automotive supplier integrated Mayfran conveyors across 47 CNC centers, achieving:
- Machine availability increase from 83% to 94%
- £1.2M annual scrap reduction
- 9-month equipment payback period
Case 2: Medical device manufacturer utilizing Hennig systems realized:
- 97% reduction in manual chip handling labor
- 25% improvement in surface finish quality
- ISO Class 6 cleanroom compatibility
Post-installation audits consistently show maintenance cost reductions of 18-27% versus legacy chip management methods.
Swarf Conveyors and Loom Conduit Integration Strategies
The next evolution involves synergistic operation with loom conduit systems managing coolant delivery lines and data cabling. This integrated approach addresses two persistent challenges:
- Elimination of cable entanglement through coordinated movement programming
- Consolidated maintenance scheduling for fluid/swarf management systems
Early adopters in precision optics manufacturing report 40% faster changeovers when swarf conveyors
share predictive maintenance data with loom conduit controllers. This mechanical symbiosis represents the emerging standard for Industry 4.0 machining facilities.
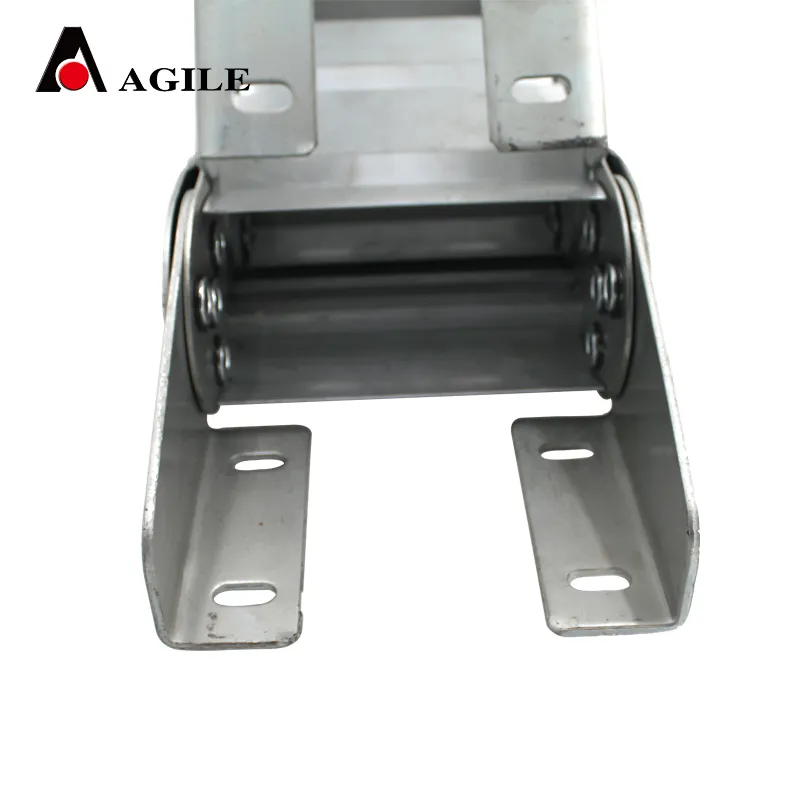
(swarf conveyors)
FAQS on swarf conveyors
以下是为核心关键词 Swarf Conveyors 及相关词 Loom Conduit 创建的 5 组英文 FAQs,采用 HTML 富文本格式:Q: What is the primary function of a swarf conveyor?
A: A swarf conveyor transports metal chips and debris from machining processes. It ensures efficient removal of waste materials like turnings or grindings. This keeps work areas clean and prevents equipment blockages.
Q: How does a loom conduit integrate with swarf conveyors?
A: Loom conduits organize and protect cables/hoses within swarf conveyor systems. They prevent tangling or damage from sharp metal scraps. This synergy ensures reliable automation and reduces maintenance needs.
Q: What industries commonly use swarf conveyors?
A: Swarf conveyors are essential in CNC machining, automotive manufacturing, and aerospace. They handle high-volume metal waste in precision engineering environments. Heavy industries like foundries also rely on them for scrap management.
Q: Why are corrosion-resistant materials vital for swarf conveyors?
A: Metal swarf and coolants cause rapid deterioration. Stainless steel or hardened polymers extend conveyor lifespan. This resistance minimizes downtime and replacement costs in harsh operational settings.
Q: Can loom conduits improve safety in swarf conveyor setups?
A: Yes. By securing electrical lines and fluid hoses away from moving parts, loom conduits reduce tripping hazards and leak risks. They ensure compliance with industrial safety standards like OSHA.