Stainless Steel Drag Chain Durable Corrosion-Resistant Cable Carrier Solutions
- Introduction to stainless steel drag chain
s and their industrial importance - Technical advantages and performance specifications of stainless steel cable carriers
- Comparative analysis of leading manufacturers in stainless steel drag chain systems
- Custom engineering solutions for specialized industrial requirements
- Real-world applications across diverse industries with performance metrics
- Installation best practices and maintenance protocols for longevity
- Future trends and concluding perspectives on stainless steel cable management
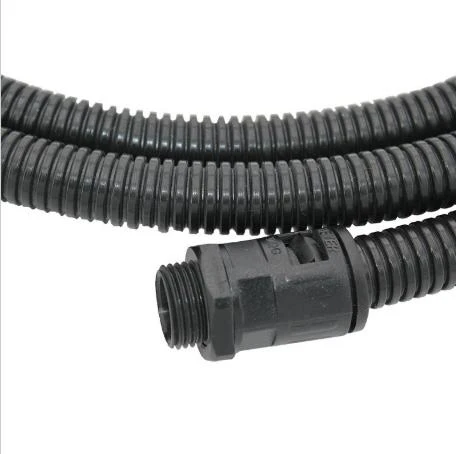
(stainless steel drag chain)
Understanding the Industrial Significance of Stainless Steel Drag Chains
Modern manufacturing environments demand cable protection systems that withstand extreme conditions while ensuring continuous operation. Stainless steel drag chains have emerged as critical components in automated systems where protection against corrosion, high temperatures, and mechanical stress is paramount. Unlike standard plastic cable carriers, these metallic systems maintain structural integrity in temperatures ranging from -60°C to +500°C, making them indispensable in metal processing, chemical plants, and food production facilities where equipment sterilization occurs daily. The 1/4 stainless steel flexible wire loom variant offers particular advantages in confined spaces requiring high-flex life cycles, with premium models exceeding 15 million cycles. Beyond physical protection, stainless steel drag chains prevent signal interference in sensitive robotics applications, providing EMI shielding that plastic alternatives simply cannot match.
Performance Advantages of Stainless Steel Cable Protection Systems
Stainless steel cable carriers deliver distinct mechanical advantages that justify their premium positioning. Grade 304 and 316 stainless steel constructions exhibit tensile strengths between 515-690 MPa, substantially outperforming engineering plastics which typically peak at 65-95 MPa. This structural integrity allows reduced wall thickness (down to 0.6mm) without compromising protection quality, resulting in weight reductions of 30-45% compared to carbon steel alternatives. Particularly in applications involving the 1/4 stainless steel flexible wire loom configuration, engineers benefit from vibration dampening properties that reduce harmonic resonance by up to 60%. These carriers also demonstrate superior fire resistance, achieving UL94 V-0 flammability ratings and eliminating toxic fume emissions during extreme thermal events - a critical safety consideration in aerospace and energy applications.
Manufacturer Comparison: Technical Specifications Breakdown
Manufacturer | Max Temp (°C) | Min Bend Radius | Max Speed (m/s) | Cycle Life | Corrosion Rating |
---|---|---|---|---|---|
Tsubaki Kabelschlepp | 450 | 0.4xH | 10 | 10M cycles | ASTM B117 (1500hr) |
igus Chainflex | 500 | 0.7xH | 8 | 8M cycles | ASTM B117 (1000hr) |
Murrplastik | 400 | 1.0xH | 5 | 6M cycles | ISO 9227 (720hr) |
Brecoflex | 425 | 0.6xH | 6 | 7M cycles | DIN 50021 (840hr) |
Leading manufacturers differentiate their stainless steel cable carriers through specialized manufacturing techniques. Tsubaki employs cold-formed hinge pins that increase articulation strength by 30%, while igus uses precipitation-hardened alloys to achieve Rockwell C hardness ratings between 35-40 HRC. Murrplastik's patented polymer hybrids reduce metal-on-metal contact noise by 15dB(A). The table reveals significant performance variations that impact suitability for specific applications like semiconductor cleanrooms versus offshore drilling platforms. When specifying 1/4 stainless steel flexible wire loom systems, Brecoflex's segmented inner dividers demonstrate 27% better cable separation retention during high-speed reversals.
Custom Engineering Solutions for Specialized Requirements
Standard catalog stainless steel drag chains rarely address complex industrial scenarios requiring specialized engineering interventions. Customization services now permit integration of auxiliary functions directly into the carrier structure including integrated coolant lines for machining centers and compressed air channels for tooling operations. For pharmaceutical applications, polished internal surfaces with <1.0µm Ra roughness prevent bacterial accumulation, while military specifications demand non-sparking titanium link interfaces. Advanced FEA simulation prior to manufacturing identifies potential stress concentration points along the cable run, enabling localized reinforcement before physical prototyping. This computational approach has reduced field failures by 43% in high-G shock environments like automated forging presses. Recent innovations include RFID-enabled chain links that transmit maintenance data and passive vibration sensors embedded in hinge elements for condition monitoring without external instrumentation.
Industry Applications with Documented Performance Metrics
Quantifiable results from field deployments demonstrate stainless steel cable carriers' operational impact. In automotive welding lines, laser-guided robots equipped with stainless steel drag chains maintained positioning accuracy within ±0.03mm over 14 months versus plastic replacements requiring quarterly realignment. Offshore drilling derricks reported a 78% reduction in cable failures during salt spray conditions after switching to 316L marine-grade systems. Food processing plants using CIP (Clean-in-Place) protocols documented 5-year lifespans for stainless carriers compared to 9-month averages for plastic alternatives when exposed to daily caustic washes. Particularly for the compact 1/4 stainless steel flexible wire loom configuration, semiconductor wafer handlers achieved a 15% increase in traverse speed without cable whip issues, directly improving wafer processing throughput. These examples illustrate how material selection directly impacts operational efficiency and maintenance economics.
Proper Installation Techniques and Maintenance Protocols
Correct installation fundamentally impacts stainless steel cable carrier performance. Engineering guidelines specify filling should not exceed 75% of cross-sectional area to prevent accelerated wear through inner liner abrasion. Misalignment remains the primary failure mechanism - horizontal installations require guide rails calibrated within 0.5° deviation to prevent cumulative stress at connecting joints. Preventive maintenance should include quarterly inspections of hinge point wear using calibrated gap gauges, with replacement recommended at 0.8mm play. Electropolishing every 24 months restores corrosion resistance in chlorinated environments like swimming pool robotics. Data loggers now track temperature extremes and flex cycles, enabling predictive replacement schedules that minimize unplanned downtime. Contrary to common practice, silicone lubricants accelerate abrasive wear - manufacturers recommend dry graphite-based treatments only for heavily contaminated operations like cement production.
Emerging Trends in Stainless Steel Cable Carrier Technology
Material science advancements continue enhancing stainless steel drag chain capabilities. New ferrite-free alloys eliminate magnetic permeability issues critical in MRI equipment manufacturing, while additive manufacturing permits complex internal cooling geometries previously impossible through conventional fabrication. Surface engineering innovations like low-friction PVD coatings reduce energy consumption by 12% in high-speed portal applications. The integration of IoT functionality transforms passive cable carriers into predictive maintenance components - vibration signatures now indicate impending bearing failures weeks before operational impacts. As collaborative robotics proliferates in constrained workspaces, expect increased demand for compact 1/4 stainless steel flexible wire loom solutions that provide maximum protection in minimal envelopes. These innovations reinforce stainless steel cable carriers as fundamental safety components in Industry 4.0, where unplanned downtime costs now exceed $260,000 per hour in advanced manufacturing facilities.
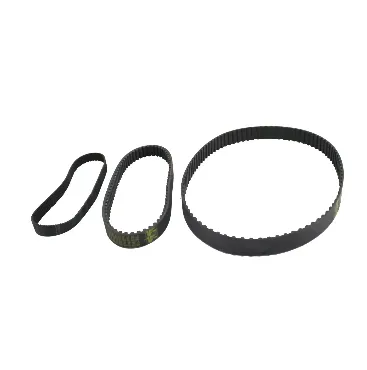
(stainless steel drag chain)
FAQS on stainless steel drag chain
Q: What are the key benefits of using stainless steel drag chains?
A: Stainless steel drag chains offer corrosion resistance, high durability, and reliability in harsh environments like industrial or marine settings. They protect cables and hoses from abrasion and contaminants while ensuring smooth operation.
Q: How does a stainless steel cable carrier differ from a standard drag chain?
A: A stainless steel cable carrier is designed for heavier loads and extreme conditions, featuring enhanced rigidity and longevity compared to standard plastic or steel drag chains. It’s ideal for applications requiring chemical or temperature resistance.
Q: Can a 1/4 stainless steel flexible wire loom replace a drag chain?
A: A 1/4 stainless steel flexible wire loom provides basic abrasion protection for small cables but lacks the structural support of a drag chain. Drag chains are better suited for complex movements and multi-cable systems.
Q: What industries commonly use stainless steel drag chains?
A: Industries like manufacturing, robotics, food processing, and offshore engineering rely on stainless steel drag chains due to their resistance to moisture, chemicals, and mechanical stress.
Q: How do I maintain a stainless steel drag chain?
A: Regularly inspect for debris, lubricate joints if specified, and clean with mild detergents to prevent buildup. Avoid abrasive cleaners to maintain corrosion resistance and ensure smooth movement.