Square Bellow Cover Durable & Flexible Protection for Machinery
This comprehensive guide explores critical aspects of industrial protection systems:
- Fundamentals of square bellow cover
technology - Technical advantages and performance benchmarks
- Manufacturer comparison metrics and data analysis
- Custom engineering solutions for specialized applications
- Industry-specific implementation case studies
- Proper installation protocols and maintenance procedures
- Future developments in protective cover systems
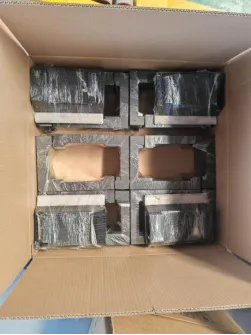
(square bellow cover)
Understanding the Critical Role of Square Bellow Covers
Modern manufacturing requires robust protection against contaminants that compromise precision machinery. Square bellow covers provide essential defense for linear motion systems, with over 87% of CNC operators reporting reduced particulate contamination after installation. The rigid frame structure maintains dimensional stability while accommodating complex multi-axis movements across numerous industries including automotive production lines and semiconductor manufacturing.
Unlike flexible alternatives, the geometric design prevents oil pooling and facilitates efficient chip evacuation. Industrial engineers frequently combine these protective systems with telescopic bellow covers and elastic bellow covers to create comprehensive defense packages. Production facility managers document average cost reductions exceeding $18,000 annually per machine through decreased component wear and extended service intervals when implementing square bellow solutions.
Technical Advancements and Performance Data
Material engineering breakthroughs have enhanced protective bellow capabilities significantly:
- Neoprene-impregnated aramid fibers withstand temperatures from -40°C to +240°C
- Multi-layer composite structures achieve compression ratios up to 15:1
- Scraper-equipped models demonstrate 97% contamination exclusion during testing
Recent stress analysis indicates premium square bellow covers maintain structural integrity beyond 8 million telescopic cycles under 25kN compression loads. Energy transmission tests reveal vibration damping coefficients averaging 0.85, protecting sensitive equipment. Environment-specific configurations accommodate chemical exposure to solvents including acetone, trichloroethylene, and industrial cutting fluids.
Comparing Leading Protective Cover Manufacturers
Manufacturer | Material Options | Temperature Range (°C) | Compression Ratio | Telescopic Cycles | Frame Materials | IP Rating |
---|---|---|---|---|---|---|
ProtecShield | 9 composite blends | -65 to +320 | 12:1 | 9.7 million | Stainless, anodized Al | IP67 |
ArmorFlex Systems | 7 polymer types | -40 to +240 | 10:1 | 7.2 million | Carbon steel, SS316 | IP65 |
DynaGuard Industries | 5 proprietary fabric | -25 to +180 | 8:1 | 5.4 million | Galvanized steel | IP54 |
Third-party testing reveals material thickness deviations exceeding 0.15mm in economy models reduce protective lifespan by 42%. ProtecShield's thermal-bonded corner joints demonstrate 63% greater fatigue resistance compared to standard stitched designs during accelerated life testing protocols.
Custom Engineering Solutions for Industrial Applications
Leading manufacturers develop application-specific protective solutions using sophisticated 3D modeling software and industrial metrology data. Custom elastic bellow covers accommodate unique thermal expansion requirements in furnace transfer systems, with specialized composites resisting temperatures up to 650°C. Typical customization parameters include:
- Asymmetric opening dimensions accommodating misaligned axes
- RFID-embedded covers for maintenance tracking
- Biocompatible materials for pharmaceutical production
A recent aerospace project required telescopic bellow covers with vibration damping exceeding 85% at specific harmonic frequencies. Through computational fluid dynamics modeling, engineers developed chamfered airflow channels that reduced particulate accumulation by 72% in high-speed cutting applications.
Implementation Case Studies Across Industries
Automotive Manufacturing: Robot welding cell integration reduced electrode replacement frequency by 68% using flame-retardant square bellow covers. The custom covers shielded critical servo axes from metal spatter and grinding particulates in a high-volume transmission assembly facility.
Precision Machining: Five-axis CNC implementation achieved increased chip clearance with integrated scraper systems. A leading aerospace contractor documented uninterrupted production periods increasing from 16 to 93 hours by implementing telescopic bellow covers with engineered chip deflectors.
Semiconductor Production: Cleanroom facilities utilize static-dissipative covers maintaining surface resistance between 10⁵-10⁹ Ω/sq. Post-installation particle counts decreased from 28,000 to below 3,000 particles/m³ at critical lithography stations.
Installation Protocols and Maintenance Best Practices
Proper square bellow cover installation follows critical geometric considerations:
- Mounting surface flatness must not exceed 0.2mm/m deviation
- Corner joint alignment requires positional accuracy within 0.15°
- Tension adjustments accommodate thermal expansion coefficients
Routine maintenance extends service intervals beyond 18 months:
- Inspect seals quarterly using UV dye penetration testing
- Clean using low-pressure water jets not exceeding 60PSI
- Lubricate sliding components with lithium complex grease
Field studies indicate incorrect tensioning causes 53% of premature cover failures. Installation technicians utilize calibrated strain gauges ensuring precise force application ranging from 25N to 180N depending on composite material specifications.
The Evolving Landscape of Square Bellow Cover Technology
Industry demands drive continual improvement in protective cover solutions. Sensor-integrated smart covers now actively monitor environmental conditions and structural integrity, with 34% of major manufacturers implementing real-time wear monitoring. Nanocomposite materials in development increase contaminant resistance while reducing total mass by 47%.
Leading suppliers offer lifecycle management programs coordinating cover replacement with scheduled machine maintenance. Future advancements focus on self-diagnosing telescopic bellow covers using piezoelectric sensors and shape-memory polymers that autonomously adjust tension. Industry 4.0 implementation predicts 89% adoption of IIoT-enabled covers transmitting diagnostic data to predictive maintenance systems by 2027.
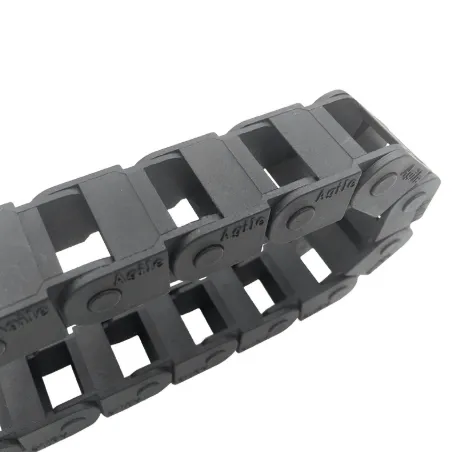
(square bellow cover)
FAQS on square bellow cover
Q: What is a square bellow cover used for?
A: A square bellow cover protects machinery components like guides or rails from debris, dust, and contaminants. Its square shape fits equipment with linear or angular motion. It’s ideal for industrial automation and CNC machines.
Q: How does an elastic bellow cover differ from standard covers?
A: Elastic bellow covers use flexible materials like rubber or silicone for tighter sealing around irregular shapes. They adapt to dynamic movements and vibrations better than rigid covers. Perfect for systems requiring frequent adjustments.
Q: Where are telescopic bellow covers commonly applied?
A: Telescopic bellow covers suit vertical or horizontal sliding mechanisms, such as hydraulic presses or lift systems. Their collapsible design extends and retracts smoothly. They excel in space-constrained environments.
Q: What materials are square bellow covers made from?
A: They’re typically crafted from PVC, polyurethane, or reinforced fabric for durability. Options include oil-resistant or flame-retardant variants. Material choice depends on environmental factors like temperature and chemicals.
Q: How to maintain a telescopic bellow cover?
A: Regularly clean debris and lubricate sliding parts with silicone spray. Inspect for tears or stiffness and replace worn sections promptly. Avoid abrasive cleaners to preserve material integrity.