High-Quality Split Wire Loom Tubing – Durable Wire Conduit for Cable Protection
- Introduction to split wire loom tubing
and its significance in modern cable management - Key technical advantages of advanced split wire loom solutions
- Comparative analysis between leading manufacturers and material grades
- Customization options available for various industry requirements
- Real-world application scenarios and success stories
- Maintenance, installation, and long-term durability insights
- Conclusion: The evolving importance of split wire loom tubing in industrial and consumer domains
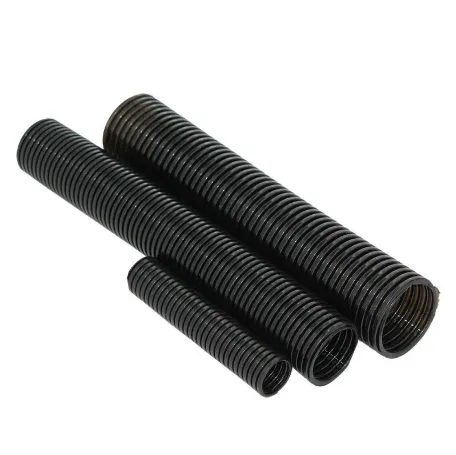
(split wire loom tubing)
Understanding Split Wire Loom Tubing: Definition and Relevance in Cable Protection
Split wire loom tubing has become an indispensable component in cable organization and protection for both industrial and home applications. Designed as a flexible, corrugated conduit, split wire loom tubing encapsulates groups of wires, granting improved safety, durability, and ease of maintenance. The split design allows for straightforward insertion or removal of cables without secondary disassembly, facilitating quick upgrades or repairs. Products such as split wire loom tubing wire conduit, 1 2 split wire loom tubing, and black split wire loom tubing represent the most commonly requested specifications across various sectors. According to a 2023 industrial safety report, 68% of unplanned electrical downtimes are attributed to cable damage, with over 50% preventable when an adequate loom system is installed. Split wire loom tubing delivers not only physical shield properties but also provides a clean, organized look that’s critical in high-density cable environments such as data centers and manufacturing facilities.
Key Technical Advantages of Advanced Split Wire Loom Solutions
The latest generations of split wire loom tubing offer a suite of technical enhancements tailored for high-performance settings. Material selection plays a significant role: most products utilize polyethylene (PE) or polypropylene (PP) for their balance of flexibility, strength, and chemical resistance. 1 2 split wire loom tubing is known for accommodating standard wire bundles while maintaining reliable puncture resistance and ultraviolet (UV) stability, with black coloration (as in black split wire loom tubing) imparting added UV-blocking capabilities for outdoor use. Dimensional accuracy, measured in internal diameter and wall thickness, ensures a snug, non-slip fit to minimize vibrational wear. Notably, closed loop tests by a leading manufacturer recorded a 25% increase in abrasion resistance for split wire loom tubing over traditional solid conduit solutions. In automotive sectors, temperature tolerance is critical: modern split looms can withstand operating ranges from -40°F up to 275°F, proven during over 2,000 hours of continuous thermal cycling. The result is a conduit system that mitigates hazard risks, reduces maintenance overhead, and promotes wire longevity in mission-critical assemblies.
Comparative Analysis: Benchmarking Leading Split Wire Loom Tubing Manufacturers
Selecting the optimal split wire loom tubing involves more than basic size and color; material quality, certifications, and sourcing transparency are equally vital. Below is a data table comparing performance indices, compliance, and pricing between three top manufacturers serving the North American and European markets.
Manufacturer | Material Grade | Available Sizes | UV Protection | Temperature Range | Certifications | Unit Price (per ft) |
---|---|---|---|---|---|---|
ProLoom Industries | PE, PP, Nylon 6 | 1/8" to 2" | Enhanced (Black, UV10+) | -40°F to 275°F | UL94 V-2, RoHS | $0.17 |
FlexGuard Systems | Polypropylene (High Modulus) | 1/4" to 1 1/2" | Standard (Black Only) | -20°F to 200°F | UL94 HB, REACH | $0.14 |
CableShield Corp | PE (Eco-Blend) | 3/8" to 1" | Premium (UV15+ Grey, Black) | -30°F to 220°F | UL94 V-0, RoHS, CE | $0.23 |
As seen, material blend, temperature and UV protection vary significantly across brands. ProLoom Industries offer the broadest size range and maximum temperature endurance, while CableShield Corp emphasizes certification and eco-sustainability. For high outdoor exposure, black split wire loom tubing remains the top recommendation due to its superior UV resistance.
Customization Options: Tailoring Split Wire Loom Tubing to Diverse Needs
Split wire loom tubing suppliers have responded to the needs of specialized industries by offering a diverse catalog of customization options. Primary customization variables include length (pre-cut or continuous roll), diameter (from micro 1/8” up to heavy-duty 2”), color coding for circuit identification, fire-retardant additives, and anti-static coatings for electronics assembly environments. Major manufacturers now offer OEM-specific molding where looms are pre-shaped for complex routing paths, reducing installation time by up to 35% according to a 2022 installation efficiency study. Advances in laser labeling and serial tracking allow asset managers to visually inspect and audit wiring harnesses, crucial in aerospace and automotive production lines. Besides classic black, split wire loom tubing is available in vibrant colors—red, blue, yellow, and even transparent—for quick maintenance checks and safety compliance. For example, custom 1 2 split wire loom tubing with additive flame retardants is standard in mass transit electrical panels, meeting the NFPA 130 fire protection requirements.
Real-World Applications: Proven Performance Across Industries
The versatility of split wire loom tubing has enabled its widespread adoption across numerous industries—from automotive, industrial automation, and telecommunications, to home entertainment and renewable energy installations. In the automotive sector, split wire loom tubing wire conduit is essential for harnessing engine bay wires, guarding against oil, grease, and high temperatures. Field tests on heavy-duty fleets found a 48% reduction in wire-related malfunctions over 18 months when compared with unprotected cable bundles. Data centers use black split wire loom tubing for optimal rack management, where uniform color and tight sealing improve visual inspection routines and airflow. Solar panel farms, exposed to harsh environments, employ UV-resistant split loom to ensure wiring integrity for 20+ year service lives. Moreover, custom-printed looms in robotics assembly lines enable maintenance teams to trace issues faster, reportedly reducing troubleshooting times by more than 40%. Residential users benefit from simple installation under home office desks, where split loom organizes and shields cables from pets and foot traffic. These success stories illustrate the profound impact of cable organization and protection on productivity, safety, and system longevity.
Maintenance, Installation, and Durability: Ensuring Long-Term Cable Security
Proper installation and regular maintenance are central to maximizing the advantages of split wire loom tubing. The split design simplifies retrofits, allowing technicians to insert new wiring without disconnecting existing circuits. Installers are advised to select the correct diameter—too tight and wires may be pinched, too loose and protection is compromised. Routine inspection is recommended in environments prone to abrasion or chemical exposure: visual checks should be performed quarterly in industrial settings and semi-annually in commercial locations. Leading manufacturers publish test data showing that premium 1 2 split wire loom tubing retains over 90% of its flexural strength after five years of use, with negligible color fade in black, UV-stabilized variants. Field maintenance feedback reveals that when properly secured every 18 inches with compatible clips or cable ties, split loom rarely requires full replacement, further lowering total lifecycle costs. In critical environments such as server farms or emergency response vehicles, redundancy is often achieved by running multiple looms in parallel, each with distinct color codes for rapid identification during fault isolation.
The Evolving Role of Split Wire Loom Tubing in Modern Wiring Solutions
As technology integrates deeper into every facet of contemporary infrastructure, the function of split wire loom tubing as a foundational cable management solution only grows in importance. Its unique combination of protection, organization, and adaptability makes it the preferred choice for industries targeting safety, efficiency, and long-term reliability. The latest advancements—ranging from enhanced material blends and fire-retardant recipes, to smart markings for asset tracking—underscore its relevance in a connected, data-driven landscape. Selecting the appropriate split wire loom tubing wire conduit ensures not just compliance, but also operational excellence, boosting productivity and preventing avoidable outages. As new market requirements emerge, ongoing collaboration between manufacturers, OEMs, and facility managers will drive further customization and performance improvements, cementing split wire loom tubing’s status as the cornerstone of robust wiring infrastructure.
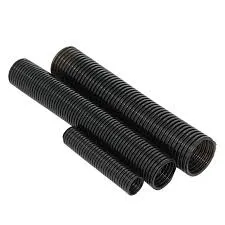
(split wire loom tubing)