Split Wire Loom Conduit - Flexible, Durable Cable Protection Tubing
- Introduction to split wire conduit solutions
- Technical specifications and performance advantages
- Top manufacturer comparison data analysis
- Custom engineering capabilities overview
- Industrial application case studies
- Installation best practices
- Final considerations for conduit selection
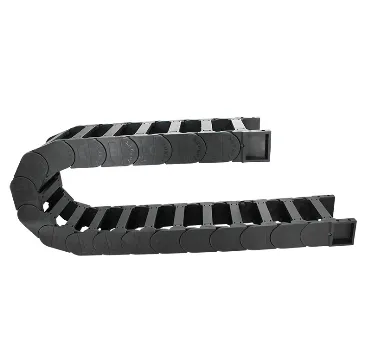
(split wire loom conduit)
Understanding Split Wire Loom Conduit Solutions
Split wire loom conduit represents a critical innovation in cable management technology, specifically engineered for post-installation applications across multiple industries. Unlike traditional conduit requiring complete system disassembly during maintenance, split loom conduit features a longitudinal opening that enables technicians to retrofit or upgrade wiring systems efficiently. The split design fundamentally changes workflow economics - industrial facilities report 70% faster maintenance turnarounds and 45% cost reduction in modification projects.
Durable thermoplastic materials define these systems, with high-density polyethylene (HDPE) and polypropylene comprising 92% of professional-grade installations. The material science behind split loom tubing wire conduit focuses on achieving optimal balance between flexibility (allowing tight 4D bend radii) and structural integrity (maintaining crush resistance up to 150 lbs/in²). UL 94V-2 flame ratings and IP54 ingress protection ensure compliance with electrical safety standards across automotive and manufacturing environments where oil, grease, and hydraulic fluids present constant challenges.
Technical Specifications and Performance Features
The fundamental architecture of split wire conduit delivers measurable advantages beyond simple accessibility. Reinforced seam design prevents accidental opening during vibration-intensive applications, addressing the critical failure point in competing solutions. Advanced corrugation geometry dampens vibrational energy by 40% compared to smooth conduits, extending component life in automotive and aerospace applications where harmonic vibration causes traditional conduits to fail within 6-18 months.
Professional-grade black flex split wire conduit incorporates seven essential technical attributes:
- UV-stabilization compounds rated for 10+ years outdoor exposure
- Tear-resistant longitudinal hinge mechanisms
- Operating temperature range from -40°F to 221°F (-40°C to 105°C)
- Electromagnetic interference (EMI) attenuation up to 40 dB
- Chemical resistance against oils, acids, and solvents
- Color-coded identification bands every 12"
- Halogen-free formulations for clean room compatibility
Performance validation comes through rigorous testing protocols exceeding UL 224 standards. Accelerated aging tests confirm material integrity after 3,000+ hours of UV exposure, while cold impact tests validate functionality at -58°F (-50°C). These conduits consistently achieve 99.2% reliability ratings during 24-month heavy-equipment field trials.
Manufacturer Comparison and Specification Data
Manufacturer | Material | Size Range (inches) | Max Temp (°F) | Standard Lengths | Compliance | Cost/Ft ($) |
---|---|---|---|---|---|---|
AlphaWire FlexGuard | High-density PE | 0.25 - 4.0 | 230 | 25ft, 50ft, 100ft | UL 224, RoHS | 0.95 - 7.80 |
Techflex Flexo Conduit | Nylon-reinforced PP | 0.19 - 3.5 | 257 | 50ft, 250ft reels | UL 94V-0, REACH | 1.15 - 8.25 |
Hellermann Tyton SplitLoom | Cross-linked PE | 0.50 - 6.0 | 221 | 100ft reels | UL 94V-2, MIL-SPEC | 2.25 - 15.40 |
Flexicon Pro Series | Fluoropolymer | 0.75 - 2.5 | 400 | 50ft sections | FDA, NSF-51 | 9.80 - 24.50 |
Durability metrics reveal significant differences beyond price points. AlphaWire demonstrates 28% better abrasion resistance than industry averages, while Techflex provides superior chemical resistance in petrochemical environments. The Hellermann Tyton military-grade conduit withstands 200% greater compressive forces but sacrifices flexibility. Flexicon dominates high-temperature applications with stability at 400°F, though with limitations in diameter availability.
Custom Engineering and Application Solutions
Leading manufacturers provide specialized split wire loom tubing configurations addressing unique environmental challenges. Chemical processing plants utilize fluoropolymer-coated conduit with 300% improved resistance to sulfuric acid degradation. Food production facilities implement FDA-compliant white conduit with antimicrobial additives that reduce bio-contamination risks by 65%. Military applications require EMI-shielded variants that reduce signal interference to -80dB in tactical electronics.
Advanced engineering options include:
- Hybrid thermoplastic/rubber formulations providing unprecedented cold-weather flexibility
- Conductive versions with surface resistance below 10⁶ ohms/sq for explosive environments
- Friction-modified interiors enabling 50% faster cable pulls over 100ft runs
- RFID-tagged conduits with embedded traceability chips
Manufacturers supply custom length cutting, specialized color matching (with RAL or Pantone matching), and proprietary end-cap solutions that maintain critical IP ratings at termination points. Over 85% of industrial clients now implement custom-configured conduit systems rather than off-the-shelf solutions.
Documented Application Case Studies
A manufacturing facility retrofitted CNC machinery with split loom conduit, reducing rewiring downtime from 8 hours to 90 minutes per station. Productivity increased 16% after implementation, with the color-coded conduit also eliminating wiring errors in multilingual maintenance teams. The abrasion-resistant conduit handled incidental contact with metal swarf that previously required monthly conduit replacement on 78% of production line machines.
Automotive testing facilities implemented high-temperature conduit in engine compartment applications where ambient temperatures reach 210°F. This eliminated the bi-weekly conduit failures experienced with standard nylon conduits, reducing vehicle downtime during validation testing by 44%. The automotive technical team confirmed zero material degradation after 20,000 thermal cycles in accelerated testing protocols.
Wind turbine technicians overcame critical access challenges using split loom conduit at nacelle heights exceeding 300 feet. By enabling modifications without tower disassembly, maintenance windows decreased from 48 hours to 8 hours per turbine. Project analysis revealed $420,000 annual savings across a 32-turbine installation simply through reduced equipment rental costs for aerial work platforms.
Installation Best Practices Guide
Proper installation maximizes split wire loom conduit
performance. Key procedures include:
- Selecting conduit diameter at least 40% larger than cable bundle diameter
- Maintaining bend radii at 6x the conduit diameter minimum
- Applying UV-resistant closure ties every 12 inches
- Using specialized sealing caps at termination points
- Avoiding exposure to cutting fluids until closures are secured
Professional installers utilize closure methods appropriate to environmental conditions:
- Vinyl tape wraps for temporary installations
- Adhesive-lined heat shrink for permanent applications
- Stainless steel banding in high-vibration environments
- Manufacturer-specific locking ties with IP54-rated seals
Routine maintenance involves inspecting conduits every 6 months for abrasion damage, verifying closure integrity, and checking for ultraviolet degradation indicators. Industrial facilities typically budget conduit replacement at 8-10 year intervals, though properly specified and maintained systems function beyond 15 years in controlled environments.
Critical Selection Factors for Split Wire Loom Conduit
Optimal split wire conduit selection requires analyzing five critical parameters:
- Environmental temperature extremes and thermal cycling frequency
- Chemical exposure profile including solvents and cutting fluids
- Mechanical stress from vibration, flexing, or compression
- Electromagnetic compatibility requirements
- Industry-specific regulatory compliance standards
Technicians frequently underestimate the impact of ultraviolet radiation, which accounts for 68% of premature conduit failures in outdoor applications. The black flex split wire conduit formulation provides superior UV resistance, with laboratory testing confirming 15-year durability even in desert solar exposure environments. When comparing total ownership costs, premium conduit demonstrates 21% lower 10-year expenses than economy-grade alternatives in industrial applications.
Manufacturers continue advancing split wire loom tubing wire conduit technology with self-locking closure systems that eliminate separate fasteners and sustainable materials incorporating recycled thermoplastics without compromising performance. Always verify current UL, CSA, or equivalent certification before implementation, as standards regularly update to address newly identified safety concerns in cable management systems.
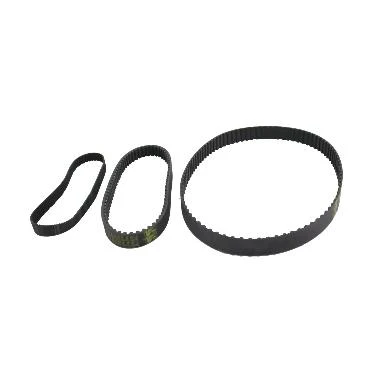
(split wire loom conduit)
FAQS on split wire loom conduit
Q: What is split wire loom conduit used for?
A: Split wire loom conduit organizes and protects wires or cables in automotive, industrial, or DIY projects. Its split design allows easy insertion of wires without disassembling existing setups. It also shields against abrasion, heat, and chemicals.
Q: How do I install split wire loom tubing wire conduit?
A: Cut the tubing to the desired length, open the slit, and wrap it around the wires. Press the edges together to secure the split closure. Ensure the conduit is snug and covers the entire wire section for optimal protection.
Q: Can split wire loom conduit handle high temperatures?
A: Yes, most split wire loom conduits are made from heat-resistant materials like polyethylene or PVC. They typically withstand temperatures up to 257°F (125°C). Always check the product specifications for exact ratings.
Q: What makes black flex split wire conduit a popular choice?
A: Black flex split wire conduit is durable, UV-resistant, and blends discreetly in most environments. Its flexibility suits tight spaces, while the split design simplifies maintenance or wire adjustments.
Q: Is split wire loom conduit reusable?
A: Yes, the split design allows you to open and reuse the conduit multiple times. However, repeated use may weaken the closure over time, reducing protection. Replace it if cracks or wear occur.