Split Loom Tubing Sizes Comparison A Guide to Selecting the Right Fit
Understanding the Importance of Split Loom Tubing Sizes in Manufacturing
In the manufacturing industry, precision and efficiency are paramount. One often overlooked component that significantly contributes to these factors is the split loom tubing, a vital part of many machines and equipment. Split loom tubing sizes play a crucial role in determining the performance and reliability of various systems, from conveying fluids to protecting cables and wires. This article delves into the importance of selecting the right split loom tubing sizes for optimal results in manufacturing processes.
Split loom tubing, also known as split conduit or split pipe, consists of a flexible plastic or rubber tube that can be easily opened and closed around bundles of wires or cables. The primary function of this tubing is to provide protection from physical damage, chemical exposure, and environmental factors such as dust and moisture. However, the effectiveness of this protection is largely dependent on choosing the correct size of the tubing.
The size of the split loom tubing must be carefully selected based on the number and size of the wires or cables it will encase. A tubing that is too small may not fit around the bundle properly, leaving gaps where debris and moisture can infiltrate, potentially causing damage or short circuits. On the other hand, a tubing that is excessively large might move around, leading to abrasion of the wires and reducing the overall integrity of the system.
Moreover, the appropriate size of split loom tubing ensures ease of installation and removal
Moreover, the appropriate size of split loom tubing ensures ease of installation and removal
Moreover, the appropriate size of split loom tubing ensures ease of installation and removal
Moreover, the appropriate size of split loom tubing ensures ease of installation and removal
split loom tubing sizes. When maintenance or upgrades are necessary, having the correct size allows for quick and efficient changes without damaging the wires or cables inside. This not only saves time but also reduces downtime, which is essential for productivity in any manufacturing setting.
Another consideration when choosing split loom tubing sizes is the space constraints within machinery or along production lines. In tight spaces, a smaller profile tubing may be required to ensure a clean and organized setup. Conversely, in areas where space is not an issue, a larger size could offer more flexibility during installation and future modifications.
In conclusion, the selection of split loom tubing sizes is a critical decision that impacts both the protection of vital components and the efficiency of manufacturing operations. By understanding the importance of matching the tubing size to the specific needs of each application, manufacturers can enhance product quality, reduce maintenance costs, and improve overall workflow. It is a small detail that can make a significant difference in the success of industrial processes.
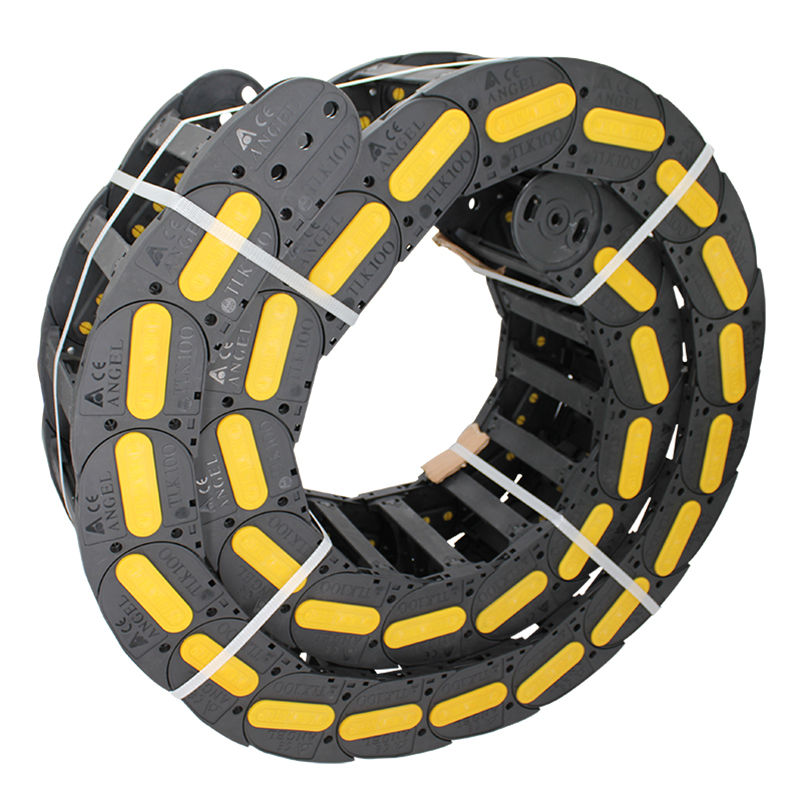
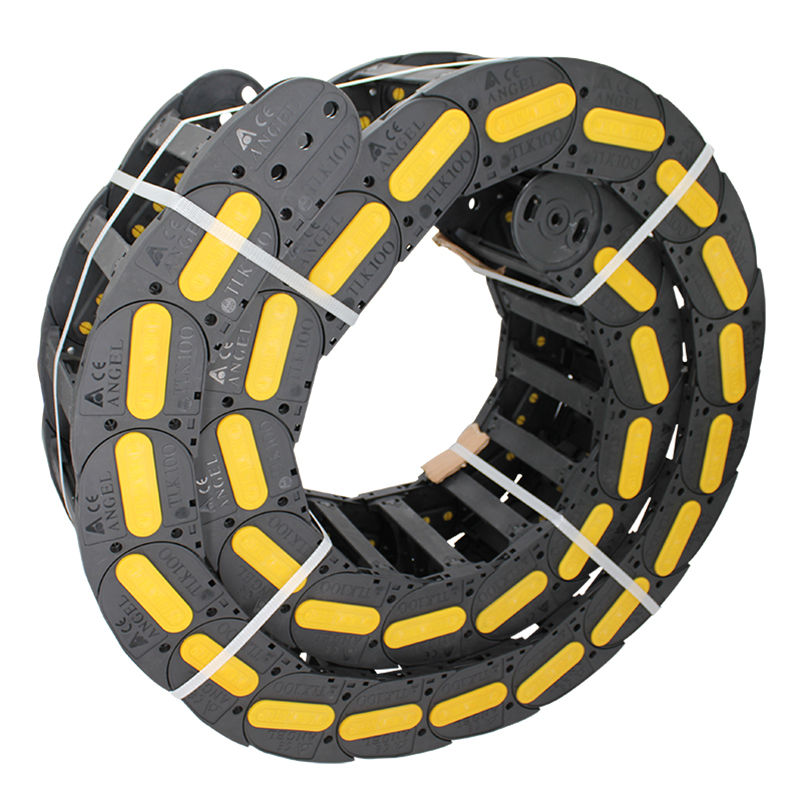