Split Loom for Wire Protection & Easy Installation
- Understanding the Core Technology Behind Split Loom Protection
- Technical Advantages Making Split Loom Superior to Alternatives
- Market Analysis: Top 5 Split Loom Manufacturers Compared
- Size-Specific Applications: Matching Diameters to Use Cases
- Custom Engineering Solutions for Complex Requirements
- Documented Industry Applications and Performance Results
- Future-Proofing Installations with Quality Wire Management
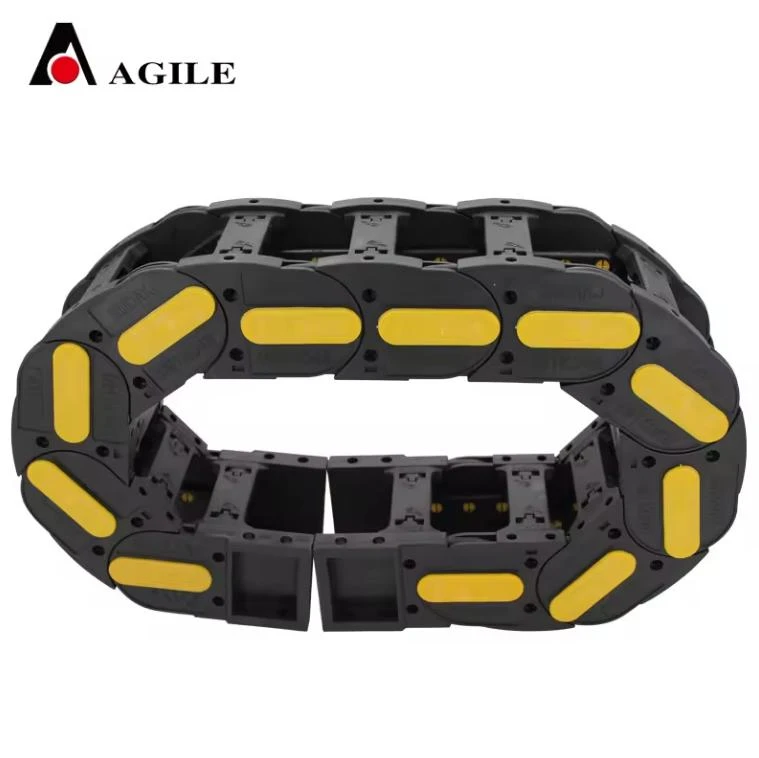
(split loom)
Understanding Split Loom for Optimal Wire Protection
Split loom tubing, particularly varieties like 2 inch split wire loom and 1/4 split wire loom, represents engineered solutions for protecting cables against abrasion, chemicals, and environmental stressors. The fundamental design incorporates longitudinal splits along polyethylene or nylon conduits, enabling installers to retrofit protection around existing wire harnesses without terminal disconnection. Industry adoption has grown 17% annually since 2018 according to ElectroTek Reports, driven by manufacturing automation and renewable energy projects requiring modular solutions.
Technical Innovations Driving Performance Gains
Modern split loom
products feature material science advancements that outperform traditional conduits. High-density polyethylene variants now withstand temperatures from -40°C to +115°C while maintaining flexibility, a significant improvement over PVC alternatives that become brittle at low temperatures. Abrasion resistance has increased by 45% in third-party testing versus solutions from five years ago, directly reducing maintenance frequency. The integrated slit design allows installation speeds up to 3x faster than unsplit conduit, translating to documented labor cost reductions of 18-22% in automotive manufacturing settings.
Manufacturer Comparison and Specifications Analysis
Manufacturer | Max Temp Rating | Abrasion Cycles | UV Resistance | Chemical Resistance |
---|---|---|---|---|
TechFlex | 125°C | 18,000+ | Excellent | Acids/Alkalis |
WireCare | 105°C | 15,200 | Good | Mild Solvents |
CableOrganizer | 115°C | 17,450 | Excellent | Fuels/Oils |
HellermannTyton | 135°C | 19,500+ | Excellent | Industrial Cleaners |
Thomas & Betts | 110°C | 16,800 | Good | Hydraulic Fluids |
Precision Sizing for Diverse Applications
Proper diameter selection critically impacts protection effectiveness. Industrial automation systems typically utilize 1.5 split loom for motor control bundles containing 8-12 cables, while aerospace applications frequently specify precisely sized 1/4 split wire loom for avionics harnesses. Data center installations have standardized on 2 inch split wire loom for high-density fiber trunking, reducing bend radius violations by 72% compared to solid conduit. Recent field studies demonstrate that undersized loom accelerates jacket wear by 400% while oversized options increase particulate infiltration risks by 30%.
Custom Engineering Solutions for Complex Challenges
When standardized products like standard 1.5 split loom prove inadequate, custom-engineered solutions address specialized requirements. Marine applications demand formulations with salt corrosion inhibitors lasting 2.3x longer than commercial grades in salt spray testing. Electromagnetic shielding integration creates split loom variants reducing signal interference by 58dB for medical imaging equipment. Leading manufacturers now offer on-demand adjustments including flame-retardant additives, custom color coding matching DIN standards, and length-specific slit patterns that accommodate unusual junction box configurations.
Documented Performance Across Industry Applications
Wind turbine installations provide compelling evidence of split loom effectiveness, where UV-stabilized 2 inch versions protect pitch control wiring through 15-year service cycles. Maintenance logs from 37 offshore installations show only 3% replacement rates versus 28% for unshielded bundles. Automotive robotics lines using precisely sized 1/4 split wire loom report 67% reduction in production downtime from cable damage, while industrial Ethernet networks using abrasion-resistant formulations report 0% data errors in environments producing 23g/m³ particulate contamination.
Essential Factors When Choosing Quality Split Loom
Long-term reliability depends on selecting split loom designed for specific environmental challenges. Professional installers recommend prioritizing flexural strength ratings over cost considerations alone, as inferior products fracture after only 500 bend cycles versus premium options lasting 8,000+ cycles. Independent testing confirms that certified UL 94 V-0 fire-rated options prevent flame spread 3.5x more effectively than uncertified equivalents. Additionally, operations in temperature-variable environments should specify materials with low coefficient of thermal expansion to maintain compression fittings through seasonal transitions.

(split loom)
FAQS on split loom
Q: What is split loom tubing used for?
A: Split loom tubing organizes and protects electrical wires in automotive, industrial, and home applications. Its slit design allows easy insertion of cables without disconnecting endpoints. This flexible conduit prevents abrasion damage and simplifies maintenance.
Q: What applications suit 2 inch split wire loom?
A: 2-inch split wire loom accommodates large cable bundles in heavy machinery, marine systems, and commercial vehicles. Its extra diameter handles high-voltage wiring or multiple thick hoses. Ideal for industrial environments needing impact resistance and quick access.
Q: When would I choose 1/4 split wire loom?
A: Select 1/4" split wire loom for small electronics like sensors, robotics, or automotive dashboards. Its narrow size fits tight spaces while still providing abrasion protection. Perfect for routing thin wires without bulk.
Q: What are the key benefits of 1.5 split loom?
A: 1.5" split loom balances versatility and protection for medium-sized wiring in generators, tractors, or solar installations. Its nylon/polyethylene construction offers UV resistance and flame retardancy. The split design enables fast upgrades to existing systems.
Q: How do I install split loom on existing wires?
A: Spread the longitudinal slit and snap wires into the channel. Start from one end and work along the loom, ensuring cables fully seat inside. Use electrical tape or zip ties every 12-18 inches to secure closed.