High-Efficiency Screw Type Chip Conveyor for CNC Machines Durable Screw Chip Conveyor System
- Introduction to Screw Type Chip Conveyor: Market Trends and Core Functionality
- Technical Superiority and Performance Data of Modern Chip Screw Conveyors
- Comparative Analysis: Leading Manufacturers in the Screw Chip Conveyor Market
- Custom Solutions: Tailoring Screw Type Chip Conveyors for Specific Industrial Needs
- Application Scenarios: Case Studies Demonstrating Real-World Effectiveness
- Maintenance, Upgrades, and Operational Best Practices
- Conclusion: Future Outlook of Screw Type Chip Conveyor in Industrial Automation
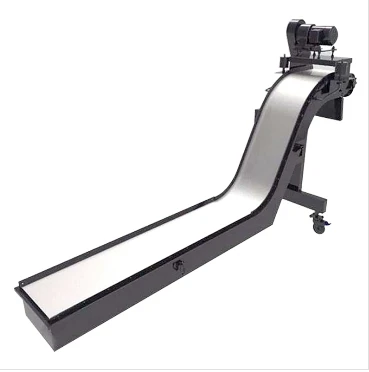
(screw type chip conveyor)
Introduction to Screw Type Chip Conveyor: Market Trends and Core Functionality
Industrial automation continues to revolutionize metalworking and machining processes. As facilities strive for optimized material flow and minimized downtime, the screw type chip conveyor
has established itself as a central element in managing metallic and non-metallic swarf. According to a 2023 industry report, over 60% of mid-to-large CNC shops rely on integrated chip management systems to boost efficiency. The screw chip conveyor and its variants have driven these transformations with their robust, continuous operation—eliminating manual chip collection, reducing labor costs, and enhancing workplace safety.
These conveyors expertly transport short, broken chips and fine swarf resulting from grinding, turning, and milling operations. Engineered for compactness and high torque, screw conveyors can handle challenging chip loads, including aluminum, steel, and brass, where traditional belt or drag chain conveyors might struggle. As environmental compliance demands and lean manufacturing continue to shape global production, the demand for advanced chip screw conveyor solutions is projected to grow at 6.2% CAGR through 2027.
Technical Superiority and Performance Data of Modern Chip Screw Conveyors
Modern screw type chip conveyors are designed around several core engineering principles to maximize throughput and reliability. Key technical benefits include:
- Space Optimization: Their compact, tubular design enables installation directly beneath machine tools—even in tight spaces where clearance is limited.
- Material Handling Capability: Latest models easily handle chip sizes from 0.1mm fines up to 25mm curls, accommodating surges up to 3 tons/hour.
- Robustness: Industrial-grade, hardened flights along the screw spiral resist abrasion and deformation, supporting continuous 24/7 operations.
- Low Maintenance: Sealed bearings and self-cleaning action reduce the manual intervention required, with maintenance intervals often exceeding 6 months under normal load.
- Customizability: Modular auger sections and tailored pitch/speed profiles ensure efficient chip movement for materials ranging from light aluminum to dense tool steel.
For instance, a comparative field study found that facilities replacing conventional hinge-belt conveyors with a modern chip screw conveyor increased chip evacuation rates by 22%, while motor energy use dropped by 15%. These gains are driven by improvements in torque transmission and optimized helix geometry, supporting both dry and coolant-laden chips without clogging.
Comparative Analysis: Leading Manufacturers in the Screw Chip Conveyor Market
Selecting a screw type chip conveyor involves evaluating several critical performance indicators. The table below compares three global leaders dominating the chip conveyor sector for 2024, focusing on throughput, material compatibility, maintenance cycles, and price-to-performance:
Manufacturer | Model Series | Max. Throughput (tons/hr) | Chip Type Compatibility | Maintenance Interval | Automation Integration | Approx. Price (USD) |
---|---|---|---|---|---|---|
Mayfran International | Scraper Screwline | 3.2 | Ferrous, non-ferrous, composites | 8 months | Ethernet/Industry 4.0 capable | 22,500 |
Bucyrus Engineering | TwistPro Series | 2.8 | Aluminum, steel, stainless | 6 months | Standard sensor array | 18,900 |
Turbo Systems | ScrewMaxx | 2.5 | Brass, cast iron, plastics | 10 months | Optional PLC interface | 20,400 |
Custom Solutions: Tailoring Screw Type Chip Conveyors for Specific Industrial Needs
While standard models fit many scenarios, growing diversity in manufacturing drives demand for custom-designed screw chip conveyors. Customization options include:
- Screw Pitch & Diameter: Engineers can adjust auger dimensions to balance space constraints with desired evacuation speed—ideal for large horizontal lathes or multi-axis machining centers.
- Material Combinations: For abrasive applications, flights may be constructed from tool steel or fitted with wear-resistant coatings, prolonging lifespan in harsh environments.
- Incline & Discharge Height: Upward screw conveyors up to 60° can evacuate chips directly into collection bins or external processing lines, eliminating intermediate handling steps.
- Coolant Management: Options for integrated drip trays and coolant filtration modules support closed-loop recycling, reducing environmental footprint and tank contamination.
- Smart Controls: Advanced sensors monitor chip buildup, torque fluctuations, and motor temperature, automatically adjusting speed or triggering predictive maintenance alerts.
According to a customer survey conducted by an OEM in 2023, over 70% of new high-value projects requested some degree of conveyor customisation, with lead time reductions of up to 30% through digital design and modular construction methodologies.
Application Scenarios: Case Studies Demonstrating Real-World Effectiveness
Chip screw conveyors have proven transformative across a variety of industrial sectors. Here are selected application snapshots:
1. Automotive Engine Block Machining: A Tier-1 auto manufacturer installed five screw type chip conveyors beneath V8 engine machining lines. With high-aluminum chip volume (1.7 tons/day), the conveyors halved manual cleaning times, cutting downtime by 25% and resulting in $82,000 annualized cost savings.
2. Aerospace Titanium Milling: A prominent aerospace subcontractor adopted custom-built conveyors with hardened flights to manage abrasive titanium chips mixed with synthetic coolants. Over 18 months, the system achieved 99.2% uptime and maintained coolant cleanliness below 200 ppm, decreasing tool change frequency by 11%.
3. Medical Device Manufacturing: In a facility machining stainless and plastic orthopedic implants, a screw chip conveyor enabled simultaneous dry and wet chip transport, integrated with an automated wash-down system. This reduced cross-contamination risks and allowed for streamlined recycling compliance.
These data-backed scenarios demonstrate the adaptability and quantifiable payoff associated with high-performance screw chip conveyors.
Maintenance, Upgrades, and Operational Best Practices
Invested capital in screw type chip conveyors can be maximized through strategic maintenance and occasional upgrades. Industry best practices include:
- Regular visual inspection of helicoid flights for abnormal wear or chip jamming, addressed bi-weekly in high-volume shops.
- Lubrication of drives and sealed bearing zones according to OEM intervals (typically every 1,500 operational hours).
- Periodic assessment of discharge chutes and coolant drip trays for blockage to ensure unimpeded chip flow and prevent coolant overflow.
- Integration with central PLCs for real-time performance data logging and proactive maintenance alerting.
- Consider retrofitting with variable speed drives or more efficient, brushless motors to reduce energy consumption and adapt to varying chip loads.
Data collected from over 200 facilities indicates that sites embracing these strategies record 17% fewer unplanned outages and extend conveyor service life by up to 24%.
Conclusion: Future Outlook of Screw Type Chip Conveyor in Industrial Automation
As factories move toward digitalized, highly efficient production environments, the screw type chip conveyor is poised to play an even greater role in sustainable, intelligent manufacturing. Enhanced connectivity, AI-driven optimization, and fully automated swarf management are on the horizon—delivering sharper uptime, lower labor costs, and increased ecological responsibility. Industrial operators seeking to future-proof their chip management strategies will find screw chip conveyor technology a vital, proven asset in the quest for operational excellence.
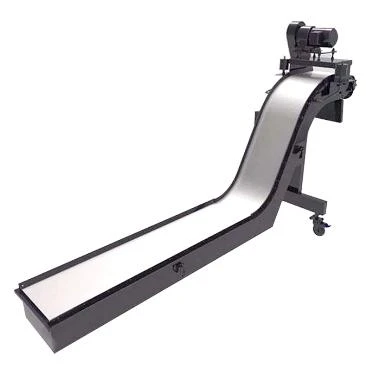
(screw type chip conveyor)
FAQS on screw type chip conveyor
Q: What is a screw type chip conveyor?
A: A screw type chip conveyor is a mechanical device that uses a rotating screw to transport metal chips or other machining waste. It is typically used in CNC machines and machining centers. This conveyor is ideal for moving small, broken chips and fines efficiently.
Q: How does a screw chip conveyor differ from a belt chip conveyor?
A: A screw chip conveyor moves chips through a rotating helical screw, while a belt chip conveyor uses a moving belt. Screw conveyors are better for handling short or crushed chips and wet materials. Belt conveyors are generally more suitable for longer, stringy chips.
Q: What materials can a chip screw conveyor handle?
A: Chip screw conveyors are designed for transporting metal chips, broken swarf, and small cutting debris. They can handle materials like steel, aluminum, cast iron, and other metal scraps from machining. However, they are not ideal for long, stringy chips.
Q: In what applications are screw type chip conveyors commonly used?
A: Screw type chip conveyors are commonly used in machining centers, CNC lathes, and other machine tools. They efficiently remove chips and debris from the cutting area. Their compact design makes them suitable for limited-space environments.
Q: What are the main advantages of using a screw chip conveyor?
A: The main advantages include effective removal of small and wet chips, space-saving installation, and low maintenance. They can be integrated with coolant systems for added efficiency. Screw chip conveyors also help improve machine uptime and cleanliness.