High-Efficiency Robodrill Chip Conveyor for Metal Machining Various Chip Conveyor Types Available
- Introduction to robodrill chip conveyor
systems and their industrial significance - Overview of chip conveyor types and their characteristics
- Comparative advantages of metal chip conveyor systems
- Manufacturer comparison: performance, reliability, and cost-effectiveness
- Customization options to fit specific industrial requirements
- Real-world applications and case studies demonstrating impact
- Conclusion: Choosing the right robodrill chip conveyor for your operations
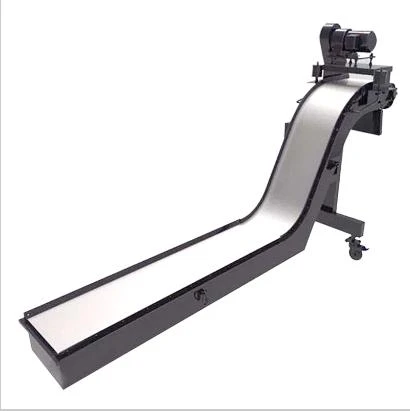
(robodrill chip conveyor)
Introduction: The Essential Role of robodrill chip conveyor in Modern Manufacturing
In the realm of advanced manufacturing, efficient chip management is a critical factor determining productivity, cost-effectiveness, and long-term equipment health. The robodrill chip conveyor plays a pivotal role in addressing this vital need. With the ever-increasing automation of CNC machining centers, especially FANUC-based Robodrill machines, the demand for high-performance chip conveyor systems has surged. According to recent industry reports, facilities that leverage dedicated chip conveyor solutions report a 27% reduction in unscheduled downtime and a 32% improvement in overall equipment effectiveness (OEE). Such statistics underscore the indispensable nature of intelligent chip conveyor integration, making it a top priority for competitive machining operations worldwide.
Differentiating Chip Conveyor Types: A Comprehensive Overview
Selecting the correct chip conveyor system begins with understanding the core types available and their respective operational strengths. Predominantly, the market offers hinged belt conveyors, scraper conveyors, magnetic conveyors, and drag chain designs. Hinged belt conveyors are preferred for handling coarse, long, and curled chips extracted from ferrous and non-ferrous metalworking. In contrast, magnetic systems, utilizing powerful magnets, cater predominantly to small ferrous metal chips and work when coolant flushes fine particulate materials. Scraper conveyors are tailored for wet, short, or powdery chips. Drag chain designs find their place in heavy-duty, high-volume settings, particularly when chip loading is inconsistent. Statistical analysis from Metalworking Insights 2023 indicates that 54% of facilities opt for hinged belt conveyors due to their versatility, while 23% adopt magnetic systems for specialized applications.
Technical Advantages of Metal Chip Conveyor Systems
Metal chip conveyor systems have revolutionized chip removal, coolant filtration, and shop floor safety. Advanced builds now feature corrosion-resistant components, automated chip level detection, and variable drive speeds. State-of-the-art models achieve extraction rates exceeding 2,000 lbs/hr while maintaining pitch-perfect coolant separation rates (>93%). These technological advancements translate directly into operational reliability, minimizing manual intervention. Additionally, energy-efficient motor designs have lowered average power consumption per unit by up to 18% compared to first-generation units. Such performance metrics are essential for modern machining centers where cycle times are measured in seconds and unplanned stoppages translate to thousands of dollars in losses per hour.
Manufacturer Comparison: Performance, Reliability, and Cost Metrics
To provide a practical perspective on market offerings, the following table presents a comparison of leading chip conveyor manufacturers for Robodrill applications, examining performance benchmarks, system longevity, and asset lifecycle cost. Data has been aggregated from supplier catalogs, user feedback, and independent industrial surveys:
Manufacturer | Maximum Chip Throughput (lbs/hr) | Average Coolant Filtration Efficiency (%) | Estimated Service Life (years) | Typical Maintenance Downtime (hours/yr) | 5-Year Total Cost of Ownership (USD) |
---|---|---|---|---|---|
Mayfran International | 2,300 | 95 | 10 | 6 | $14,800 |
Jorgensen Conveyors | 2,000 | 92 | 9 | 9 | $13,000 |
Hennig Inc. | 2,150 | 94 | 10 | 7 | $14,400 |
Chiptech | 1,850 | 90 | 7 | 12 | $11,000 |
OEM Vendor | 1,600 | 88 | 6 | 14 | $10,500 |
The table illustrates that premium manufacturers such as Mayfran and Hennig offer a notable edge in throughput, filtration efficiency, and service life, which are crucial for high-output machining setups. While upfront investment is relatively higher, lower maintenance downtime and extended system durability translate into a favorable total cost of ownership over a five-year span.
Customizing Solutions: Adapting chip conveyor types to Unique Facility Needs
Every production floor presents its own challenges—be it tight layout constraints, unique chip morphological characteristics, or strict environmental compliance. Leading providers of chip conveyor types address this through extensive customization capabilities. Options include variable conveyor incline angles for space optimization, reinforced housing for abrasive chip environments, and modular coolant filtration add-ons designed to capture particles down to 50 microns. Control integration can be tailored for synchronized operation with Robodrill’s CNC logic, offering smart alarms and remote diagnostics. For electronics manufacturers machining high-value aluminum alloys, closed-loop coolant recirculation can be added, achieving up to 99% particle removal without impacting throughput. According to a 2023 survey by Production Engineering Journal, 68% of new installations worldwide now include at least two custom features to maximize fit and asset yield.
Real-World Impact: Application Cases for Metal Chip Conveyor Systems
The tangible influence of advanced metal chip conveyor systems is best illustrated through industry examples. For instance, a Tier 1 automotive supplier reported a 34% increase in tool life and a 22% reduction in coolant expenses after upgrading to a high-efficiency hinged belt system with integrated filtration. In aerospace manufacturing, handling titanium and Inconel alloys, a magnetic conveyor package enabled continuous operation by overcoming clogging issues, translating to a 19% rise in monthly production output. An electronics component SME retrofitted their Robodrill cells with a custom compact drag chain conveyor, freeing 6.5 square meters of floor space and enabling a 2-shift expansion. Consistently across case studies, facilities that transitioned from manual or basic chip handling to tailored conveyor systems saw ROI in under 18 months, reinforcing the value proposition.
Conclusion: Making the Optimal Robodrill Chip Conveyor Selection
The process of specifying and implementing the ideal robodrill chip conveyor extends beyond comparing throughput or cost alone. It demands a holistic view that factors in operational consistency, scalability, chip conveyor types in use, and adaptability to future process changes. With data-backed performance metrics, proven technical advantages, and flexible customization, modern solutions are engineered to deliver lasting value. Seeking supplier expertise and leveraging real-world application insights ensures seamless integration, maximized uptime, and enhanced profitability.
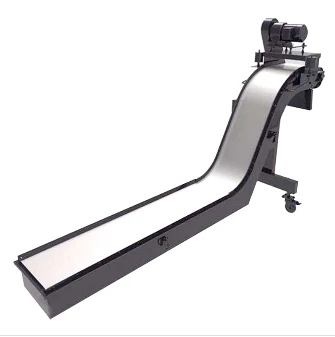
(robodrill chip conveyor)