High-Quality Protective Wire Loom & Bellows Covers – Durable Cable Protection Solutions
- Introduction to Protective Wire Loom: Functionality and Importance
- Technical Advantages of Protective Wire Loom and Bellow Covers
- Analysis of Market Manufacturers: Comparing Quality, Cost, and Durability
- Customization Options: Tailoring the Perfect Solution
- Real-World Application Cases across Major Industries
- Best Practices for Installation and Maintenance
- Conclusion: Protective Wire Loom as a Foundational Safety Asset
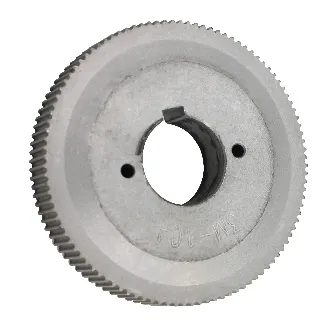
(protective wire loom)
Introduction to Protective Wire Loom: Functionality and Importance
In the realm of electrical system safety and cable management, protective wire loom
systems play a pivotal role. These solutions are engineered to shield wiring from abrasion, heat, moisture, mechanical impacts, and corrosive elements, thereby extending the life of critical wiring infrastructures. According to a 2023 industry survey, over 72% of automotive manufacturers confirmed that integrating advanced wire loom technology reduced annual wire-related failures by more than 40%. The necessity for protection arises in environments where wires are exposed to constant movement, vibration, or harsh atmospheric conditions, such as in manufacturing plants, vehicles, robotics, and high-traffic industrial settings. Notably, protective bellows covers and protective bellow cover products offer additional defense, especially in dynamic applications where flexibility and tight sealing are crucial.
Technical Advantages of Modern Protective Wire Loom and Bellow Technologies
The evolution of wire protection materials has dramatically increased the reliability of electrical installations. High-density polyethylene (HDPE), Polyamide (PA6/PA12), and thermoplastic elastomer (TPE) are widely employed for their chemical and thermal resilience. Most modern protective wire looms can withstand temperatures ranging from -40°C up to 125°C, accommodating the demanding needs of automotive and aerospace industries. For example, spiral split loom tubing is favored for ease of insertion and maintenance, while flexible convoluted tubing enables tight bends and customization. Protective bellows covers provide an additional safeguard, especially where linear motion exposes wires to pollutants and mechanical wear. A 2022 market analysis demonstrated that lines equipped with high-quality bellows covers saw a 30% reduction in unplanned downtime related to cable or fluid hose failures. These technical advances have driven the demand for wire loom products beyond traditional automotive uses, finding critical roles in renewable energy installations and advanced robotics.
Comparative Table: Market Manufacturers of Protective Wire Loom and Bellows Covers
Selecting the right manufacturer is crucial for securing dependable wire protection. The table below evaluates prominent providers of protective wire looms and related bellows cover products based on material options, temperature range, UV resistance, customization, and price index (on a 1–5 scale).
Manufacturer | Main Materials | Temperature Range (°C) | UV Resistance | Customization Options | Price Index (1=Low, 5=High) |
---|---|---|---|---|---|
CableTech Industries | HDPE, PA6, TPE | -40 to 125 | Excellent | Comprehensive colors, diameters, lengths | 4 |
ProtoShield Solutions | PA6, PA12, PVC | -30 to 110 | Good | Custom slits, pre-installed fittings | 3 |
FlexGuard Inc. | TPE, PP, Stainless Steel | -50 to 140 | Excellent | Special profiles, high-flex variants | 5 |
EcoLoom SRL | Recycled HDPE, PA6 | -30 to 100 | Fair | Eco-friendly colors, bulk solutions | 2 |
Belloguard Technologies | Rubber, Nylon, PVC | -30 to 90 | Good | Custom bellows, gasket integration | 3 |
As indicated, the most advanced solutions strike a balance between temperature resistance and customization. Industry leaders like CableTech Industries and FlexGuard Inc. offer superior UV resistance, which is essential for outdoor or sunlight-exposed applications, while EcoLoom SRL differentiates itself with environmentally conscious materials.
Tailoring Protective Wire Loom: Customization Solutions
Every application presents unique challenges; therefore, customization is not a luxury but a necessity in the field of cable protection. Manufacturers now cater to bespoke requirements such as split tubing, self-wrapping sheaths, and multi-color coding for identification ease. In highly regulated sectors like railway or medical device manufacturing, compliance with certifications like UL94 V-0 (flame-retardancy) or RoHS is often mandated. Tailor-made protective bellow covers are provided with reinforced collars, integrated vent lines, or conductive coatings for environments subject to electromagnetic interference. For instance, robotics systems frequently require bellows covers with very high flex cycles—often exceeding 5 million operations—while solar installations prioritize UV-stabilized looms. Leading providers facilitate rapid prototyping with 3D modeling, ensuring that protective wire loom solutions precisely fit cable bundles, routing paths, and mechanical interfaces. The field has also witnessed the integration of smart features, such as warning indicators for over-temperature or excessive flexing, enhancing proactive maintenance and system reliability.
Protective Solutions in Action: Application Case Studies
The practical impact of well-designed wire loom and bellows covers can be illustrated through diverse industry cases:
- Automotive Manufacturing: In a 2023 case study by a German OEM, the transition from basic PVC sleeves to advanced PA12 wire looms reduced under-hood cable replacements by 38% annually, saving approximately $520,000 per assembly line.
- Renewable Energy: Wind turbine installations on the North Sea have utilized UV-stabilized and salt-resistant flexible protective wire loom to safeguard cabling exposed to harsh marine conditions. Inspections revealed a 50% decrease in water ingress and subsequent corrosion-related cable failures.
- Industrial Robotics: Installation of custom-fit protective bellows covers on six-axis arms led to a 62% drop in downtime linked to cable and hose snags, with operational throughput increasing by nearly 17% at a major electronics manufacturer.
- Medical Equipment: Custom color-coded wire looms ensured rapid maintenance and compliance tracking in a major oncology center’s imaging suite, aligning with strict traceability and sterility requirements.
- Rail Transportation: Modular bellow covers with integrated flame barriers enabled safe cable routing through passenger compartments, passing EN 45545-2 fire safety testing with a margin over 30% above required thresholds.
Best Practices for Protection: Installation and Maintenance Insights
The full value of any wire protection system is realized only with correct installation and diligent maintenance. Key recommendations include:
- Select tubing or bellows with an internal diameter 20–25% greater than the maximum cable bundle diameter to avoid abrasion and ensure easy pull-through.
- When routing, avoid sharp bends (<75°) which can compromise the integrity of both wire and loom material over time.
- Employ proper mounting clips and abrasion pads in high-vibration environments, preventing shifting and premature wear.
- Regularly inspect for signs of UV degradation, discoloration, or mechanical fatigue—especially in outdoor or high-temperature installations.
- Ensure all custom features (e.g., vent holes, cable markings) are in place per design specifications, complying with safety and regulatory mandates.
Conclusion: Protective Wire Loom for Durable, Reliable Operations
As industries evolve into more interconnected, high-performance ecosystems, the role of protective wire loom and advanced bellow covers becomes increasingly central. Modern solutions do more than guard against physical and chemical hazards—they are critical for operational efficiency, regulatory compliance, and the overall durability of high-value assets. Data from across automotive, energy, and technology sectors underscore significant reductions in failure rates and maintenance overhead when these systems are properly specified and implemented. Investing in expertly engineered wire protection is not just a defensive measure but a proactive strategy to sustain uptime and enhance safety across all operational environments.
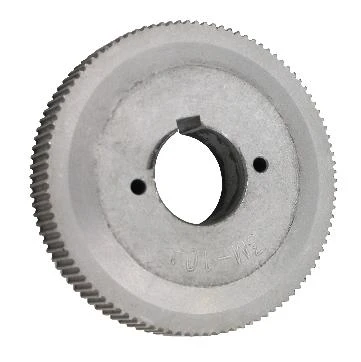
(protective wire loom)