Protective Bellow Covers for Enhanced Equipment Safety and Reliability in Industrial Applications
Understanding Protective Bellows Essential Components for Equipment Safety
In the realm of machinery and equipment design, protective bellows play a crucial role in safeguarding vital components from environmental contaminants. These flexible covers are engineered to shield moving parts from dust, debris, moisture, and other harmful elements that can drastically reduce the life span and operational efficiency of machinery. Understanding the importance of protective bellows and their applications can help engineers and maintenance teams make informed decisions for equipment protection.
What Are Protective Bellows?
Protective bellows are flexible enclosures typically made from materials such as rubber, polyurethane, or metal. They are designed to cover vulnerable parts, such as linear guides, spindles, and shafts, providing a barrier against external threats. The primary function of these bellows is to prevent the ingress of foreign materials, which could result in wear, corrosion, or operational failures.
These components come in various shapes and sizes, each tailored to meet specific applications. Some common types include accordion bellows, cylindrical bellows, and custom-designed solutions that fit particular machinery. Their flexibility allows them to expand and contract with the movement of the equipment, ensuring consistent protection without hindering performance.
Applications of Protective Bellows
Protective bellows are widely used across numerous industries, including manufacturing, automotive, aerospace, and robotics. In manufacturing environments, for instance, bellows safeguard machinery such as CNC machines and lathes. By preventing particulate matter from entering the moving parts, they help maintain precision and prolong the machine's operational lifespan.
protective bellow cover
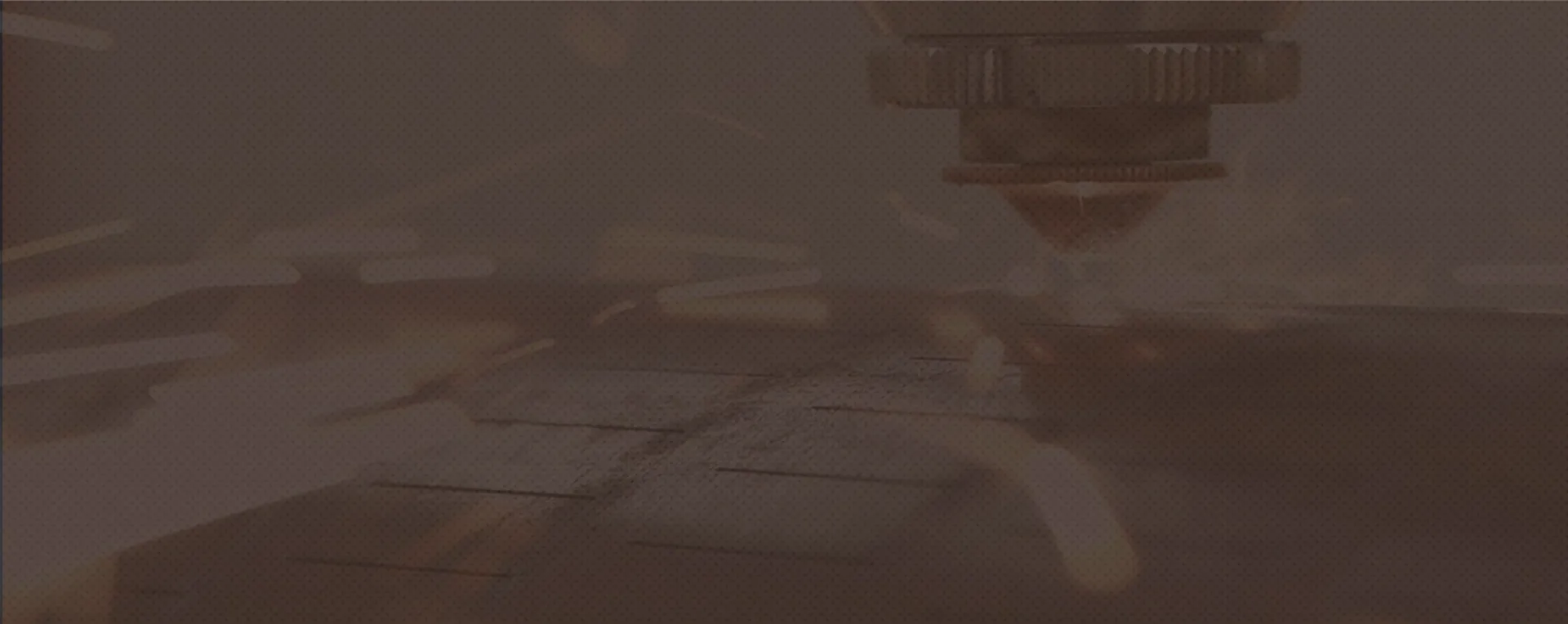
In the automotive sector, protective bellows are essential for safeguarding critical components like steering systems and suspension setups. They protect against dust and moisture, which can lead to issues such as rust and mechanical failure. Additionally, in aerospace applications, where reliability is paramount, bellows help protect sensitive instruments and control systems from harsh environmental conditions.
Benefits of Using Protective Bellows
The adoption of protective bellows can lead to multiple benefits for businesses and equipment designers. Firstly, they significantly reduce maintenance costs by minimizing wear and tear on machinery. Maintenance teams often face costly downtime due to repairs stemming from contamination, but with protective bellows in place, the likelihood of such incidents diminishes.
Secondly, these components enhance safety by preventing debris from causing accidents or failures. In high-speed machines, even a small piece of foreign material can lead to catastrophic breakdowns. The installation of bellows helps mitigate this risk, providing peace of mind for operators and management alike.
Moreover, protective bellows contribute to the overall efficiency of machinery. By ensuring clean operation environments, machines can work optimally without the hindrances caused by dirt and contaminants. This efficiency translates to better productivity, ultimately affecting the bottom line positively.
Conclusion
In summary, protective bellows are integral to the longevity and efficiency of industrial machinery across various sectors. Their ability to shield moving parts from detrimental environmental factors cannot be overstated. As technology continues to advance and machine design evolves, the role of protective bellows will likely grow in importance. Investing in quality bellows not only enhances equipment performance but also ensures safer and more reliable operations, making them a wise choice for any business focused on maintaining operational integrity.