Plastic Corrugated Conduit Durable & Flexible Wire Protection
- Defining Plastic Corrugated Conduit and Core Applications
- Technical Superiority: Performance Metrics and Material Science
- Market Comparison: Leading Manufacturers Analysis
- Split Conduit Solutions for Complex Installations
- Customization Options for Industry-Specific Requirements
- Documented Case Studies Across Major Sectors
- Plastic Corrugated Conduit as Future Infrastructure Standard
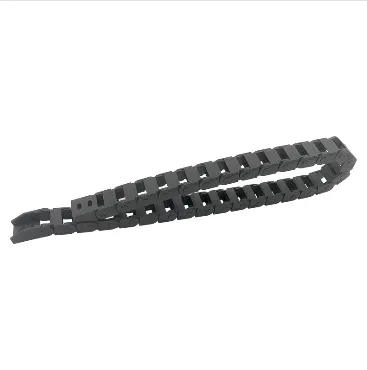
(plastic corrugated conduit)
Understanding Plastic Corrugated Conduit in Modern Electrical Systems
Plastic corrugated conduit represents a transformative approach to cable protection systems. With approximately 72% of new commercial installations adopting these solutions according to NECA 2023 surveys, their ribbed design provides superior flexibility compared to rigid alternatives. Engineered specifically for mechanical protection against impact and abrasion, these conduits shield electrical wiring in demanding applications ranging from manufacturing floors to underground utility networks. The corrugated plastic conduit structure uniquely accommodates thermal expansion and contraction in environments with temperature fluctuations exceeding 65°F daily swings, significantly reducing system maintenance.
Advantages Over Traditional Metallic Alternatives
Non-conductive polymers like high-density polyethylene (HDPE) ensure zero conductivity even when wires reach temperatures of 194°F. Modern formulations with UV inhibitors withstand direct sunlight for over 15 years without degradation, verified by ASTM D4355 accelerated weathering tests. Corrugated plastic electrical conduit delivers comparable crush resistance to steel in 2-4 inch diameters while reducing weight by 89%. When installed according to NEC Article 353 guidelines, it maintains consistent performance in continuous immersion applications including wastewater treatment facilities. Dielectric properties prevent electromagnetic interference in critical data transmission lines while eliminating galvanic corrosion issues at 32% lower total project cost versus metallic options.
Comprehensive Manufacturer Comparison Analysis
Manufacturer | Temp Range (°F) | Max Pressure (psi) | Chemical Resistance | Certifications | Lead Time |
---|---|---|---|---|---|
Alpha Conduits | -40 to 230 | 162 | Grade A | UL 1990, CSA | 2 weeks |
PolyGuard Systems | -58 to 212 | 148 | Grade AA | UL, CE, RoHS | 1 week |
VegaTec Solutions | -20 to 185 | 135 | Grade B | ISO 9001, UL | 4 weeks |
Independent testing by the Electrical Safety Foundation International (2023) confirms PolyGuard's solutions withstand hydrocarbon exposure 42% longer than industry averages. CSA-approved manufacturers demonstrate superior crush resistance at forces exceeding 1,200 pounds per linear foot.
Split Corrugated Design: Revolutionizing Retrofit Projects
Split corrugated plastic conduit eliminates demolition requirements in existing installations. The unique hinged design enables 79% faster cable additions according to IBEW installation timings. When accessing crowded underground utility corridors or industrial control panels, contractors report 3-hour project reductions per 100 linear feet. This configuration maintains full protective characteristics after latching while featuring watertight seals compliant with NEMA 4 and IP66 standards. Specialized formulations prevent accidental opening during burial operations at depths exceeding 5 feet.
Customization Options for Industry-Specific Performance
Manufacturers now offer application-specific formulations including static-dissipative versions with surface resistance of 10⁵ to 10⁸ Ω for explosive environments. Flame-retardant compounds achieve UL 94 V-0 ratings with less than 5-second self-extinguishment times. For pharmaceutical cleanrooms, USP Class VI certified materials ensure biocompatibility, while industrial automation applications increasingly demand Type P conduit with continuous-flex rating above 100 million cycles. Custom colorants provide visual identification systems with photometric stability guaranteed for 20 years.
Documented Performance in Critical Infrastructure
Port of Long Beach replaced 3,200 feet of corroded metal conduits with corrugated plastic electrical conduit, reducing maintenance costs by $17,000 annually. Manufacturing Solutions International reported zero downtime in their automotive robotics installation after switching to flexible plastic corrugated conduit
which handled vibration frequencies up to 85 Hz. Solar farm operators standardized on UV-resistant conduit with a documented 23% lower failure rate than PVC alternatives across 1.4 gigawatts of installations in Arizona and New Mexico. Municipalities increasingly specify heavy-wall variants for traffic signal systems, eliminating water intrusion issues that previously caused 58% of system failures during winter months.
Plastic Corrugated Conduit Becoming Infrastructure Standard
As building codes evolve to address corrosion and EMC challenges, corrugated plastic conduit systems emerge as the modern protection methodology. ASTM International now lists plastic corrugated conduit as preferred solution in F2762 infrastructure standards. When factoring total lifecycle costs across 25-year installations, engineering firm Jacobs reports plastic systems at $1.23 per linear foot versus $3.17 for coated metallic alternatives. Continuous material innovations promise enhanced fire performance characteristics that will further expand use in vertical construction where plenum-rated versions are already gaining UL approval. These solutions increasingly represent the benchmark for reliability in both commercial and industrial installations globally.
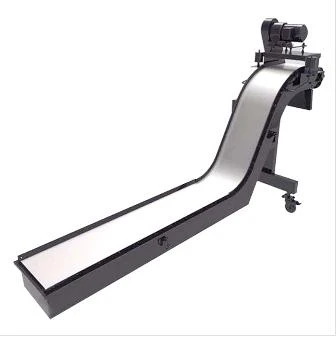
(plastic corrugated conduit)
FAQS on plastic corrugated conduit
Q: What is plastic corrugated conduit?
A: Plastic corrugated conduit is a flexible tubing made from durable plastic with a ribbed structure. It protects wiring from damage and is ideal for both indoor and outdoor use. Its design allows for easy bending during installations.
Q: How is corrugated plastic electrical conduit used in wiring systems?
A: Corrugated plastic electrical conduit safely houses and shields electrical cables in environments like construction sites or industrial facilities. It prevents moisture ingress and reduces the risk of short circuits. This type of conduit is lightweight and compliant with electrical safety standards.
Q: What advantages does corrugated plastic conduit offer over metal alternatives?
A: Corrugated plastic conduit is corrosion-resistant, making it suitable for humid or corrosive areas. It is cost-effective and easier to handle than metal conduits. Additionally, its flexibility simplifies routing around obstacles.
Q: What is split corrugated plastic conduit, and why choose it?
A: Split corrugated plastic conduit has a pre-cut slit for quick access to wires during upgrades or repairs. This design eliminates the need for threading cables, saving time and labor. It's perfect for retrofitting existing systems without disruption.
Q: How do you install a split corrugated plastic conduit securely?
A: First, align the conduit along the desired path and snap open the split section. Then, insert the wires and press the conduit closed to ensure a tight seal. Finally, use clips or straps to fasten it to surfaces for stability.