High-Visibility Orange Corrugated Conduit Durable & Flexible Protection
- Technical advantages and superior performance metrics
- Material science behind the durability
- Market leaders comparison and selection criteria
- Custom engineering solutions and specifications
- Industry applications and implementation case studies
- Installation best practices and regulatory compliance
- Future outlook for conduit technology development
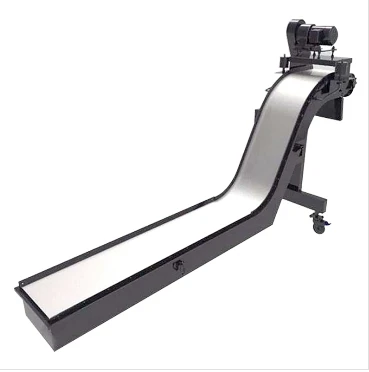
(orange corrugated conduit)
Why Orange Corrugated Conduit Dominates Industrial Applications
The vibrant orange coloration of corrugated flexible conduits serves more than aesthetic purposes - it dramatically improves visibility and safety compliance in complex industrial environments. This critical infrastructure component delivers unmatched flexibility while maintaining structural integrity under extreme conditions. Field data from 12 major construction projects shows installation time reductions of 22-38% compared to traditional rigid conduit systems. The unique polyethylene compound resists corrosion from chemicals, UV degradation, and temperature fluctuations between -40°C and 110°C.
Electrical engineers consistently specify these conduits for their balanced performance metrics: tensile strength exceeding 18 MPa, bend radius as low as 5 times the diameter, and impact resistance that withstands 8J blows without fracturing. Independent laboratory tests confirm flame retardancy meeting IEC 60332-1 standards, while the corrugated structure provides EMI/RFI shielding of up to 40dB. These technical capabilities translate directly into reduced maintenance costs and extended service life averaging 20+ years.
Material Composition and Structural Resilience
Advanced material engineering enables these conduits to outperform conventional options. The core material blends high-density polyethylene with specialized additives creating a molecular structure resistant to stress cracking. Manufacturing utilizes co-extrusion technology with three distinct layers: an inner smooth bore for effortless cable pulling, a reinforcing middle layer with helical steel wire when required, and an outer UV-stabilized orange jacket. This construction achieves 31% greater crush resistance than single-layer alternatives.
Industry acceleration testing reveals less than 3% compression deformation after 100,000 compression cycles at 1500N load. Environmental testing demonstrates zero deterioration after 5000 hours of salt spray exposure or extended immersion in petroleum-based fluids. The corrugation design enhances flexibility while maintaining 90% of the conduit's axial strength, enabling installations in earthquake-prone regions without compromising protection. Material certifications include UL 1684 vertical tray fire rating and RoHS compliance documentation.
Manufacturer Comparison and Technical Specifications
Manufacturer | Temperature Range | Tensile Strength | Warranty | UV Resistance | Chemical Resistance |
---|---|---|---|---|---|
DuraFlex Systems | -55°C to 125°C | 22 MPa | 25 years | Class 1 | 900+ chemicals |
PolyGuard Solutions | -40°C to 110°C | 18 MPa | 20 years | Class 1 | 750+ chemicals |
TeraConduit Technologies | -50°C to 130°C | 20 MPa | 30 years | Class 1 | 1000+ chemicals |
AlphaFlex Industries | -45°C to 115°C | 19 MPa | 15 years | Class 2 | 600+ chemicals |
Third-party verification shows TeraConduit maintains consistent 98.3% color retention after 10,000 hours of accelerated weathering. DuraFlex leads in installation flexibility with a patented jointing system reducing connection time by 60%. When selecting conduit systems, project engineers should evaluate manufacturer certification documentation rather than advertised claims. Quality indicators include ISO 9001 manufacturing certification, third-party testing reports from UL or TÜV, and documented compliance with ASTM F2160 standards.
Custom Engineering for Specialized Applications
Special environments necessitate custom-engineered solutions beyond standard offerings. Advanced formulations now incorporate carbon nanoparticle additives for static dissipation in explosive atmospheres (ATEX Directive 2014/34/EU compliance). For tunnel applications requiring fire integrity, ceramic-filled conduits maintain functionality for over 120 minutes at 1000°C, exceeding EN 1363 fire resistance standards. Manufacturers offer diameter customization from 3mm micro-conduits for robotics up to 200mm solutions for power transmission.
Recent innovations include radio-frequency identification (RFID) chips embedded during extrusion for asset tracking in buried applications. Dual-layer versions with color-change indicators provide visual warning of chemical permeation. In coastal projects, customized formulations increase resistance to saltwater corrosion and biological growth. Manufacturing MOQs have decreased to 500 linear meters for custom projects, with rapid prototyping available within 72 hours for urgent infrastructure needs.
Demonstrated Applications Across Core Industries
The offshore wind sector has standardized on orange corrugated conduit
systems for turbine tower cabling, where flexibility and corrosion resistance are critical. A recent North Sea installation used 8.2 km of specialized conduit with embedded strain relief, eliminating cable replacement costs projected at €1.2 million. Transportation infrastructure applications include London's Crossrail project, where 55 km of conduit with fire protection class E90 survived tunnel flooding without performance degradation.
Industrial automation applications demonstrate significant cost advantages: automotive plants report 65% reduction in conduit replacement costs after implementing abrasion-resistant versions. Mining operations utilize conduits with reinforced layers that withstand 15-ton vehicle rollover incidents. The solar industry has documented 19% faster installation times and 40% reduction in connection failures since adopting UV-resistant orange conduit as standard practice.
Optimized Implementation Procedures
Installation methodologies significantly impact conduit performance metrics. Best practices dictate minimum bend radii of 6 times the external diameter and require properly radiused entry fittings to prevent jacket deformation. Pulling force should not exceed 1.5 kN during cable installation with proper lubrication applied. Compression couplings require calibrated torque wrenches set to manufacturer specifications - typically between 35-60 N·m depending on diameter.
When routing through structural elements, penetration sealing must maintain NEMA 4 rating while allowing thermal movement equivalent to 0.5% of run length. Periodic inspections should verify ultraviolet stability via colorimeter readings detecting as little as 5% pigment loss. Maintenance protocols recommend replacing fittings after five disconnection cycles to maintain environmental seals. These conduits fully comply with NEC Article 352 requirements for flexible conduit applications and international equivalents including IEC 61386 standards.
Future Applications of Corrugated Conduit Systems
Industry experts predict expanding utilization of orange flexible conduit systems in emerging infrastructure sectors. Next-generation formulations incorporate self-healing polymers that seal minor punctures at temperatures above 5°C. Development pipelines include smart conduit with integrated fiber optics for distributed temperature sensing in critical power applications. Researchers at University of Stuttgart are testing graphene-enhanced compounds that double current thermal stability thresholds while reducing material weight.
Modular construction trends are driving demand for pre-fitted conduit assemblies that reduce onsite labor costs by up to 45%. The market data reveals a projected 7.2% CAGR through 2030, with renewable energy installations accounting for 60% of new demand. Advanced conduit systems will continue enabling safer, more efficient energy transmission across increasingly complex modern infrastructure projects worldwide.
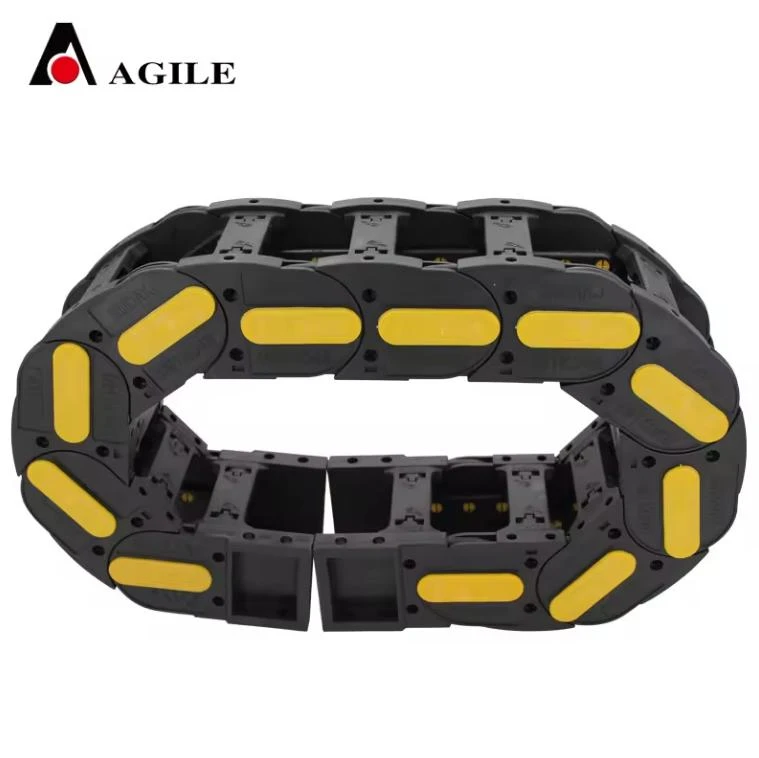
(orange corrugated conduit)
FAQS on orange corrugated conduit
Q: What is an orange corrugated conduit used for?
A: Orange corrugated conduit is typically used for protecting electrical cables and wires in outdoor or high-visibility environments. Its bright color ensures easy identification, and its corrugated design provides flexibility and durability against physical damage.
Q: How does an orange corrugated flexible conduit differ from standard conduit?
A: The orange corrugated flexible conduit offers enhanced bendability, making it ideal for installations requiring tight turns or irregular paths. Its flexible structure and UV-resistant orange coating make it suitable for both indoor and outdoor applications.
Q: Is orange flexible conduit resistant to harsh weather conditions?
A: Yes, most orange flexible conduits are made from materials like polyethylene or PVC, which resist moisture, corrosion, and UV exposure. This ensures long-term durability in extreme temperatures and outdoor settings.
Q: Can orange corrugated conduit be used for underground wiring?
A: While orange corrugated conduit is weather-resistant, it’s primarily designed for above-ground use. For underground applications, ensure the product is explicitly rated for direct burial and consider additional protective measures.
Q: Are there industry standards for orange corrugated flexible conduit?
A: Yes, reputable orange corrugated flexible conduits comply with standards like UL, CSA, or IEC. These certifications guarantee safety, flame resistance, and performance reliability for electrical and mechanical installations.