Nylon Split Loom Conduit Durable Wire Protection Solutions
- Fundamentals of cable organization using protective solutions
- Technical innovations enhancing nylon conduit performance
- Market analysis: Leading manufacturers compared
- Specialized modification options for unique requirements
- Implementation examples across industries
- Proper installation techniques and material handling
- Industry evolution and material advancements
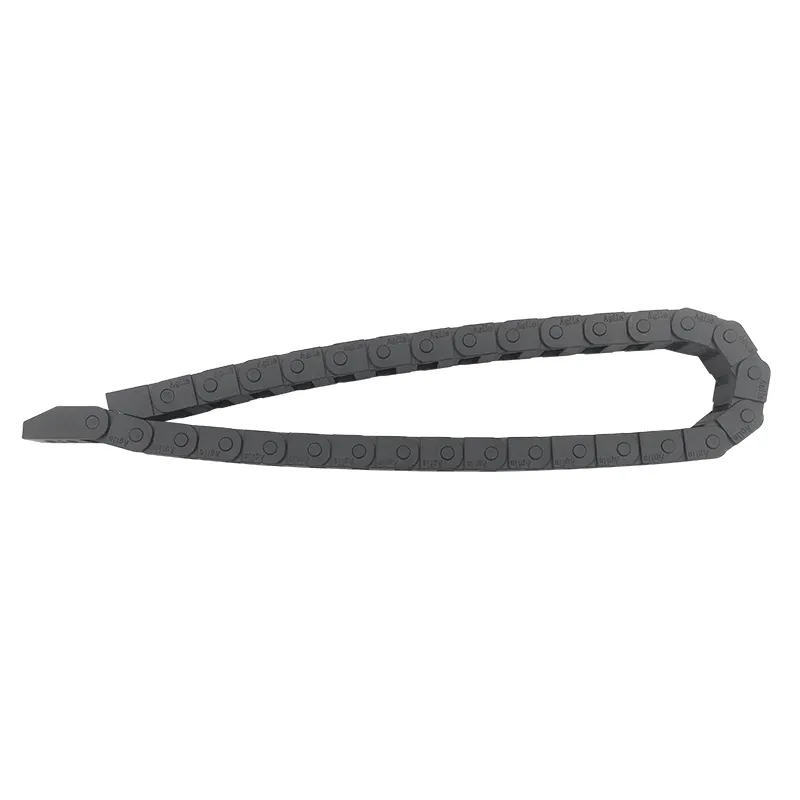
(nylon split loom)
Understanding Nylon Split Loom for Effective Cable Management
Engineering facilities require durable solutions for organizing complex wiring systems. Nylon split loom has transformed industrial cable protection approaches with its unique properties. This corrugated conduit features a longitudinal opening that allows post-installation insertion of wires. The material outperforms traditional options with greater flexibility than PVC and enhanced abrasion resistance compared to polyethylene. Industrial studies indicate 57% faster installation times when technicians use split design conduits versus solid-tube alternatives.
Corrugated nylon conduit adapts to dynamic operating environments that experience vibration or thermal cycling. The segmented structure allows natural bending while maintaining continuous coverage, preventing premature wear points. Automotive manufacturing plants report 73% reduction in wiring harness failures after transitioning to flexible nylon conduit systems from rigid plastic counterparts. Material integrity remains stable between -40°C to 115°C operational thresholds.
Engineering Advancements in Protective Sleeving Technology
Material science breakthroughs have significantly enhanced nylon split wire loom properties. Modern formulations incorporate UV stabilizers that extend outdoor service life beyond 10 years without brittleness development. Laboratory abrasion testing reveals contemporary nylon conduits withstand 48% more friction cycles than baseline products from five years ago. These improvements originate from polymer chain modifications that increase density while maintaining flexibility.
Flame-retardant grades now achieve UL VW-1 certification through phosphate-based additives that inhibit combustion spread. Manufacturing facilities processing combustible materials require these safety-rated conduits to prevent thermal events. Dielectric properties measure between 15-18 kV/mm depending on wall thickness, providing reliable electrical insulation for high-voltage applications. Chemical resistance specifications now cover 300+ industrial solvents and coolants.
Manufacturer Performance Comparison
Manufacturer | Temp Range (°C) | Flame Rating | Oil Resistance | Diameter Options (mm) | Warranty |
---|---|---|---|---|---|
FlexoTech Pro | -45 to 135 | UL V-0 | Excellent | 3-75 | 5 years |
DurableConduit Ltd | -40 to 120 | UL HB | Good | 5-50 | 3 years |
ShieldWrap Solutions | -50 to 150 | UL V-0 | Excellent | 4-100 | 7 years |
PolyArmor Inc | -30 to 110 | UL V-2 | Moderate | 6-60 | 2 years |
Specialized Modification Solutions
Customization delivers optimal nylon split loom
performance across diverse applications. Automotive harness manufacturers frequently order factory-applied foam inserts that eliminate wire rattling. Industrial plants processing abrasive materials specify wall thickness increases of 200-300% for high-wear zones. Available modification features include color-coded identification stripes, custom slit positioning options, and ESD-safe formulations dissipating static charges below 10^6 ohms.
Material composition adjustments serve extreme environments effectively. Hydrocarbon processing facilities utilize fluoropolymer-coated conduits that resist chemical permeation 90% longer than standard nylon. Cold storage operations implement plasticized compounds maintaining flexibility at -60°C temperatures. Aerospace applications require UL 94 V-0 rated nylon corrugated conduit with specialized flame-quenching properties for critical flight systems. Manufacturers supply cutting precision to ±0.2mm tolerances.
Industrial Implementation Case Studies
Robotics integration at German automotive plants demonstrates nylon split wire loom effectiveness. Production lines deploying corrugated nylon conduit recorded 43% fewer wiring issues annually compared to previous sleeving methods. Each robotic station employs custom-diameter conduits with 5.8mm internal channels allowing 23% faster component replacements during maintenance cycles.
Marine applications face unique challenges solved through specialized conduit configurations. Offshore drilling platforms implement salt-spray resistant nylon loom with zinc-chromate coatings, reducing corrosion-related failures by 81% in coastal environments. Below-deck installations use water-blocking gel-filled conduits creating moisture barriers between connections. Commercial vessels average 1,500 linear meters of corrugated nylon conduit per installation.
Optimal Installation Methodologies
Proper techniques maximize nylon split loom performance longevity. Ensure diameter selection exceeds bundled wire volume by 35-40% to prevent insulation abrasion during vibration exposure. Use dedicated closure clips spaced every 150mm to maintain slit integrity instead of makeshift solutions that compromise protection. When routing through metal surfaces, always install protective grommets with minimum 2.5mm wall thickness.
Environmental factors critically influence installation practices. Cold temperatures below 15°C necessitate material conditioning before routing to prevent polymer cracking. Dynamic bend points require radius calculations maintaining curvature above 8x conduit diameter. Avoid thermal expansion issues by allowing 30mm slack per linear meter in high-temperature zones. Technician training programs demonstrate correct separation techniques preventing damage to internal fire-retardant layers.
Advancements in Wire Protection Materials
Material research continuously improves nylon split loom capabilities. Recent polymer breakthroughs increase flexibility 45% while boosting cut resistance 15% through nanoclay additives. Future developments focus on self-healing formulations that seal minor abrasions without maintenance interventions. Recycling advances enable production using 70% recycled material content without performance compromise.
Emerging industrial standards require enhanced environmental compliance. Leading manufacturers now utilize closed-loop water systems reducing consumption 63% during nylon extrusion. Third-party audits verify adherence to REACH regulations, with premium-grade nylon corrugated conduit certified with ISO 14001 environmental management credentials. As technology evolves, nylon split loom remains central to industrial wiring protection strategies.
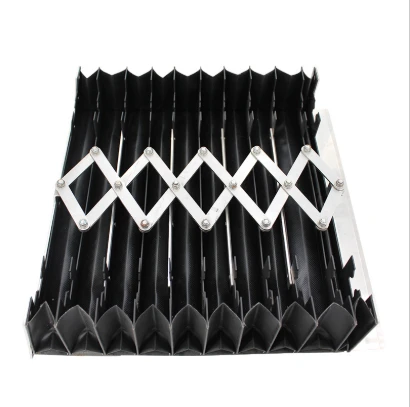
(nylon split loom)
FAQS on nylon split loom
Q: What is the primary purpose of a nylon split loom?
A: Nylon split loom protects and organizes wires or cables from abrasion, heat, and chemicals. It’s commonly used in automotive, industrial, and electrical applications. Its split design allows easy installation over existing wiring.
Q: How does a nylon split wire loom differ from corrugated nylon conduit?
A: Nylon split wire loom has a hinged opening for quick cable insertion, while corrugated nylon conduit is a fully enclosed, flexible tubing. Split loom suits retrofitting, whereas conduit is ideal for new installations requiring full protection.
Q: Can nylon split loom handle high-temperature environments?
A: Yes, most nylon split looms withstand temperatures up to 257°F (125°C). They resist melting and degradation, making them suitable for engine bays or machinery. Always check the product’s temperature rating before use.
Q: What sizes are available for corrugated nylon conduit?
A: Corrugated nylon conduit comes in diameters ranging from 1/4" to 2" to accommodate different wire bundles. Sizes vary by manufacturer, so match the conduit’s inner diameter to your cable’s outer diameter for a secure fit.
Q: Is nylon split loom reusable?
A: Yes, nylon split loom can be reused if undamaged. Simply open the split seam to add or remove cables. However, repeated bending or exposure to sharp edges may reduce its lifespan.