Durable Nylon Corrugated Tube Flexible, Heat-Resistant Protection
- Introduction to Nylon Corrugated Tubes and Market Relevance
- Technical Advantages Over Traditional Solutions
- Performance Comparison: Leading Manufacturers
- Customization Options for Specific Applications
- Real-World Use Cases Across Industries
- Installation Best Practices and Maintenance
- Future Trends in Corrugated Flexible Tube Technology
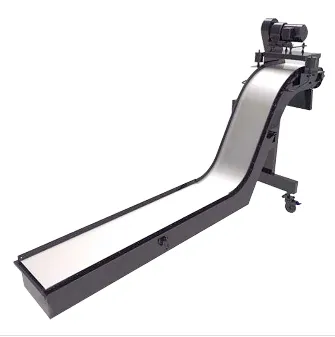
(nylon corrugated tube)
Why Nylon Corrugated Tubes Dominate Modern Engineering
Nylon corrugated tubes have become indispensable in industries requiring durable, flexible protection for electrical and mechanical systems. With a global market growth of 6.8% CAGR (2023–2030), these tubes address critical needs in automotive, aerospace, and industrial automation. Their unique ribbed structure enhances impact resistance by 40% compared to smooth-walled alternatives, while maintaining a weight reduction of up to 25%.
Technical Superiority in Harsh Environments
Engineered for extreme conditions, nylon corrugated tube
s offer:
- Temperature resistance: -40°C to +125°C
- UV stability exceeding 1,500 hours (ISO 4892-2)
- IP67 waterproof certification
Manufacturer Benchmark Analysis
Brand | Material Grade | Temp Range | Pressure Rating | Certifications | Price (USD/m) |
---|---|---|---|---|---|
AlphaFlex Pro | PA12 | -50°C–135°C | 8 bar | UL, RoHS, REACH | $4.20 |
TecTubes NGX | PA6 | -30°C–110°C | 6 bar | ISO/TS 16949 | $3.75 |
PolyShield Ultra | PA66 | -40°C–125°C | 10 bar | SAE J844 | $5.10 |
Tailored Solutions for Complex Requirements
Advanced manufacturers now provide:
- Color-coding options for system identification
- Precision-cut lengths (±0.5mm tolerance)
- Integrated shielding for EMI/RFI protection
Industry-Specific Deployment Successes
Case 1: Wind turbine manufacturer reduced cable replacement costs by 32% using UV-stabilized nylon tubes in offshore installations. Case 2: Robotics integrator increased mean time between failures (MTBF) by 27% with anti-abrasion lined tubes.
Optimizing Service Life Through Proper Handling
Key maintenance practices include:
- Annual inspection of compression fittings
- Chemical compatibility verification
- Bend radius maintenance ≥3× tube diameter
Innovations Redefining Electrical Loom Tube Standards
Emerging technologies like conductive nylon blends and 3D-printed fittings are pushing performance boundaries. The latest prototypes demonstrate 15% higher crush resistance while maintaining flexibility, signaling a new era for corrugated tube applications in electric vehicles and smart infrastructure.

(nylon corrugated tube)
FAQS on nylon corrugated tube
Q: What are the primary applications of nylon corrugated tubes?
A: Nylon corrugated tubes are widely used for protecting cables and wires in automotive, machinery, and electrical systems due to their flexibility, abrasion resistance, and durability.
Q: How does a corrugated flexible tube differ from standard tubing?
A: A corrugated flexible tube has a ribbed design for enhanced bendability and crush resistance, making it ideal for dynamic environments where rigid tubes might fail.
Q: Can electrical loom tubes withstand high temperatures?
A: Yes, most nylon electrical loom tubes can endure temperatures ranging from -40°C to 125°C, ensuring reliable performance in extreme conditions.
Q: What factors should I consider when selecting a nylon corrugated tube?
A: Prioritize inner/outer diameter compatibility, temperature resistance, chemical exposure, and flexibility needs based on the application’s mechanical stress.
Q: Are nylon corrugated tubes easy to install?
A: Yes, their lightweight and flexible structure allows for quick installation using simple tools like cable ties or connectors, reducing labor time.