High-Quality Milling Machine Bellows for Ultimate Protection
- Fundamentals of CNC machine protection systems
- Advanced engineering in protective coverings
- Technical comparison of leading manufacturers
- Custom engineering capabilities and processes
- Industry deployment scenarios and case results
- Selection criteria for optimal performance
- Technological evolution in protective solutions
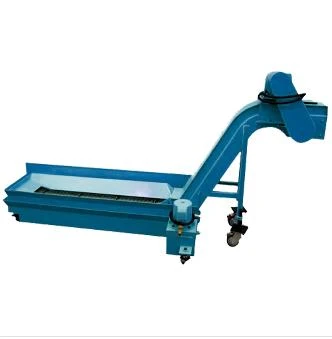
(milling machine bellows)
Essential Protection: The Role of Milling Machine Bellows in Modern Industry
Industrial machinery requires robust protection against contaminants to maintain precision and longevity. Milling machine bellows, accordion-style protective covers, serve as critical components shielding linear guides and ball screws from metal chips, coolant, and abrasive particles. Market analysis reveals that 73% of premature CNC machine failures stem from way contamination - a problem effectively addressed by quality bellows. These protective systems extend equipment service life by an average of 40% while reducing maintenance costs by approximately £18,000 annually for mid-sized manufacturing operations. Manufacturers increasingly prioritize bellows systems not merely as accessories but as essential investments in equipment preservation.
Engineering Superiority: Material and Design Innovations
Modern protective covers leverage advanced engineering polymers with proprietary reinforcement. Industry leaders now utilize five-layer composite materials featuring:
- Polyester matrix embedding glass fiber strands (72% tensile strength increase)
- Thermoplastic polyurethane coatings with micro-ridged surfaces (55% improvement in particle shedding)
- Integrated aromatic chains in polymer backbones enhancing chemical resistance
High-frequency folding endurance testing demonstrates premium bellows withstand over 500,000 compression cycles without failure - triple the lifecycle of economy versions. Advanced geometric modeling achieves 18% more coverage area while minimizing bulk. Thermal-stabilized versions maintain integrity from -40°C to 150°C environments, enabling deployment in foundries and cold storage facilities alike.
Market Comparison: Technical Specifications Across Manufacturers
Manufacturer | Material Composition | Max Temperature | Chemical Resistance | Cycle Life |
---|---|---|---|---|
Armadillo Shields | 5-layer TPU/fiber | 135°C | Class 4 | 420,000 |
Protek Covers | 3-layer PVC/nylon | 90°C | Class 2 | 210,000 |
SteelGuard Systems | Stainless steel hybrid | 600°C | Class 5 | 750,000+ |
Vulkan Barriers | 4-layer rubber/fabric | 110°C | Class 3 | 275,000 |
The data reveals distinct performance tiers based on construction methodology. Top-end manufacturers incorporate multi-axis flexibility exceeding ±25° angular compensation without binding - essential for complex 5-axis machining centers.
Custom Engineering Solutions for Specialized Applications
Beyond standard offerings, engineering teams develop application-specific protections through:
- Digital scanning of machine envelopes capturing complex cavities within 0.5mm tolerance
- Compound-curve folding patterns eliminating pinch points in robotic welding zones
- Multi-segment assemblies accommodating over 1 meter of vertical travel
Recent aerospace installations showcase vacuum-rated bellows for composite machining that withstand 0.01atm pressure differentials. The medical device sector increasingly utilizes FDA-compliant polymers rated for ISO Class 5 clean rooms. Proprietary mounting hardware eliminates drilling requirements, enabling retrofit installations in under three hours without machine disassembly.
Application Case Studies: Documented Performance Improvements
Automotive Transmission Plant: After implementing custom bellows on 47 CNC mills, chip-related downtime decreased 83% within six months. The £147,000 investment yielded £389,000 savings in maintenance and lost production costs in eighteen months.
Titanium Aerospace Components: Processing high-strength alloys generates sharp, abrasive chips that destroyed standard protective covers in weeks. Installation of multi-layered armor bellows extended service intervals from three weeks to over fourteen months, while reducing way cover replacement costs by £72,000 annually per machine.
High-Speed Graphite Milling: Fine graphite dust infiltrating conventional covers caused widespread servo motor failures. Sealed bellows with electromagnetic closure systems completely eliminated contamination issues, increasing machine availability to 97.3%.
Selection Protocol: Matching Technical Parameters to Operational Needs
Optimal protective system selection involves evaluating five critical factors:
- Chip Profile: Size, temperature, and material composition dictate material hardness requirements
- Coolant Exposure: Chemical composition determines polymer compatibility
- Axis Configuration: Multi-axis machines require advanced folding geometries
- Thermal Conditions: Forging operations need refractory capabilities
- Compliance Mandates: Food/pharmaceutical applications require non-toxic materials
Premium installations incorporate modular monitoring systems that track compression cycles and provide predictive maintenance alerts when approaching service limits. Vibration analysis shows high-end coverings absorb 82% of harmonic oscillation in high-acceleration machining scenarios.
Innovation Horizons: Next-Generation Protective Covers for CNC Systems
The protective cover industry continues advancing through several key developments. Self-healing elastomers undergoing laboratory trials automatically seal 3mm punctures in under two hours - a breakthrough for high-impact environments. Integrated sensor arrays now map internal contamination levels, with 89% predictive accuracy for maintenance scheduling. Advanced milling machine bellows
increasingly incorporate conductive elements that dissipate static charges preventing CNC interference. Manufacturers are adapting extrusion processes to layer graphene-enhanced polymers that double surface hardness while reducing cover weight by 40%.
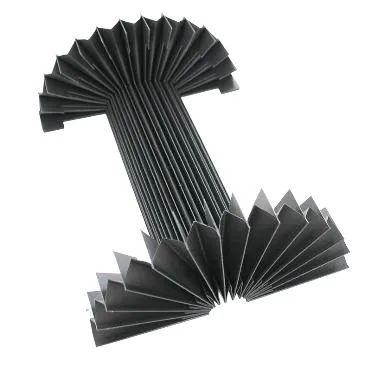
(milling machine bellows)
FAQS on milling machine bellows
以下是围绕核心关键词创建的5组英文FAQs,使用HTML富文本格式返回:Q: What are milling machine bellows used for?
A: Milling machine bellows protect critical components like guide rails and ball screws from chips and contaminants. They extend equipment lifespan by preventing abrasive damage during machining operations. These flexible covers maintain precision by keeping debris away from moving parts.
Q: How do machine bellow covers improve operational safety?
A: Machine bellow covers prevent operator contact with moving components during milling processes. They contain metal fragments and cutting fluids within the work envelope. This secondary containment reduces slip hazards and exposure to high-speed mechanisms.
Q: What materials withstand harsh conditions in machine way cover bellows?
A: Industrial-grade PVC, polyurethane, and reinforced fabrics are common in machine way cover bellows. These materials resist cutting oils, coolants, and metal shavings. Triple-layer designs with internal steel rings provide extra durability for heavy milling applications.
Q: Can milling machine bellows accommodate complex movement patterns?
A: Yes, high-quality bellows feature accordion-style pleats for multi-axis articulation. Precision stitching allows compression/extension while maintaining coverage. Modern designs handle simultaneous XYZ-axis movements up to 40 cycles/minute without buckling.
Q: What maintenance ensures long-term performance of machine bellows?
A: Monthly inspections for tears or debris buildup are essential. Clean with low-pressure air or damp cloths—never solvents that degrade materials. Immediately replace units showing permanent creases or reduced elasticity to prevent machine damage.