High-Quality Metal Corrugated Conduit for Efficient Protection & Cable Management
- Introduction: Exploring metal corrugated conduit
and its significance in industrial cabling - Understanding Technical Advantages and Defining Features
- Analyzing Industry Data and Current Market Impact
- Manufacturer Comparison and Product Quality Assessment
- Customized Solutions for Various Industrial Needs
- Application Scenarios and Case Studies
- Conclusion: The Future of Metal Corrugated Conduit in Industrial Environments
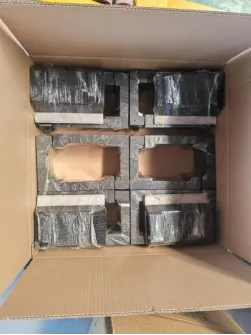
(metal corrugated conduit)
Introduction: The Critical Role of Metal Corrugated Conduit
Metal corrugated conduit has continuously gained prominence within modern industries due to its flexibility, durability, and protective capabilities for electrical and communications cabling. As industrial environments increasingly demand more robust protection against mechanical wear, heat, and electromagnetic interference, the adoption of metal corrugated conduit becomes a strategic necessity. Whether deploying complex metal chip conveyor systems or ensuring seamless integration within automated manufacturing lines, these conduits provide unparalleled shielding and longevity for wiring infrastructures. In this comprehensive analysis, we examine the defining factors that set metal corrugated conduit apart from conventional solutions and explore its expanding role in supporting advanced industrial operations.
Technical Advantages and Defining Features
The engineering behind corrugated metal conduit means it possesses a unique blend of strength, bendability, and resistance to harsh operational stresses. Typically manufactured from high-grade galvanized steel or stainless steel, the conduit’s corrugation facilitates ease of routing, absorbing vibrations, and withstanding dynamic loads without deformation. It also serves as a robust barrier against moisture, chemicals, oil mist, and physical impact.
Among the most notable advantages are:
- Superior Flexibility: Allows easy installation along complex cable routes, minimizing the risk of strain or breakage.
- Thermal Resistance: Withstands temperatures ranging from -40°C to +250°C, making it suitable for extreme environments.
- EMI and RFI Shielding: Ensures high-level electromagnetic and radio frequency interference protection, safeguarding sensitive electronics.
- Fire Resistance: Meets leading safety standards, minimizing fire hazard and maintaining structural integrity during emergencies.
Industry Data and Market Impact
The global market for corrugated metal conduit was valued at $3.2 billion in 2023, according to MarketsandMarkets. Demand is driven by rising automation across manufacturing, automotive, and logistics. Urban infrastructure upgrades and renewable energy installations increasingly specify metal conduits for superior protection and compliance.
Below is a comparative analysis of application sectors and growth projections:
Sector | 2023 Market Share | Growth Rate (CAGR 2023-2028) | Key Drivers |
---|---|---|---|
Industrial Automation | 35% | 7.8% | Factory modernization, increased process control complexity |
Automotive Manufacturing | 22% | 6.4% | Robotic systems, conveyor integration |
Construction & Infrastructure | 18% | 8.1% | Smart buildings, urban renovation |
Renewable Energy | 13% | 9.0% | Solar, wind installations, cable safety |
Others | 12% | 4.2% | Specialty machinery, defense |
Manufacturer Comparison and Product Quality Assessment
Choosing the right supplier is pivotal for ensuring conduit longevity and compliance. Leading manufacturers design their corrugated metal conduit to adhere to international standards (such as IEC 61386 and UL 360), yet their offerings vary in mechanical performance, corrosion resistance, and value-added features.
The table below summarizes top suppliers:
Manufacturer | Material Options | Bending Radius | EMI Shielding | Notable Certifications |
---|---|---|---|---|
Atkore | Galvanized Steel, Stainless Steel | 30-120 mm | High | UL, IEC, CSA |
Adaptaflex | Stainless Steel | 40-100 mm | Very High | IEC, BS EN |
Phoenix Mecano | Galvanized Steel, Aluminum | 35-140 mm | High | UL, VDE |
HellermannTyton | Galvanized Steel | 45-130 mm | Moderate | REACH, RoHS |
Customized Solutions Tailored to Industrial Needs
Modern industries increasingly require customized conduit systems, particularly for integrating metal chip conveyor systems where flexibility and robustness are critical. Customization may involve:
- Non-standard diameters for high-capacity cable bundles
- Specialized coatings, such as PVC or fluoropolymer layers, to withstand aggressive chemicals
- Reinforced fittings for vibration-intensive applications
- Integrated connectors compatible with both legacy and current control systems
Application Scenarios and Real-World Case Studies
Corrugated metal conduit is a foundation element in protecting both low-voltage and high-voltage wiring in diverse sectors. Notable application scenarios include:
- Automated Assembly Lines: Car manufacturers utilize metal corrugated conduit to route power and control cables for robotic welding stations, achieving up to 39% fewer cable replacement incidents year-over-year.
- Metal Chip Conveyor Systems: Foundries and CNC manufacturing facilities implement corrugated conduit for motor and sensor cabling, where exposure to oil mist, hot metal fragments, and abrasion is constant.
- Renewable Energy Farms: Solar array installations benefit from stainless steel conduit, offering superior UV and weathering protection for inverter and monitoring connections.
Case Study 2: A Southeast Asian port authority upgraded its automated cargo conveyor units with heavy-duty galvanized conduit. The retrofitted system reduced cable failure rates from 14 per month to less than 1, yielding substantial savings and boosting operational resilience in a coastal, humid environment.
These cases demonstrate not only broad applicability but significant cost and reliability enhancements across mission-critical processes.
Conclusion: The Future for Metal Corrugated Conduit Applications
The ongoing industrial shift toward automation, smarter infrastructure, and higher-performance safety standards cements the role of metal corrugated conduit in critical systems worldwide. As industries scale deployment of metal chip conveyor systems, smart production cells, and renewable energy infrastructure, the demand for rugged, reliable cable protection will remain paramount. By leveraging advanced material science, real-world performance data, and tailored solution design, stakeholders can drive significant efficiency gains while safeguarding their investment over the long term. With continuous innovation from leading manufacturers and integrators, metal corrugated conduit is set to define the next generation of cable management protocols in the world's most challenging environments.
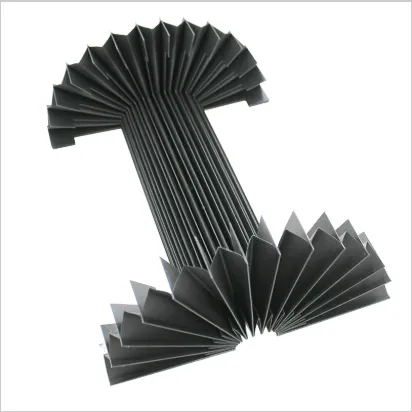
(metal corrugated conduit)