Premium Metal Cable Track for Durable Cable Protection
This article explores the critical components of industrial cable management systems. The main sections covered are:
- Industrial infrastructure requirements for cable protection
- Material science behind high-performance systems
- Engineering design superiority factors
- Leading manufacturer technical comparison
- Custom engineering solutions
- Application-based design selection
- Optimization strategies for industrial operations
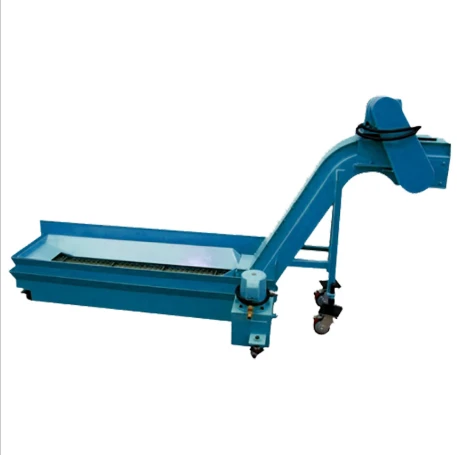
(metal cable track)
The Importance of Metal Cable Track Systems in Modern Industry
Industrial operations demand reliable solutions for protecting vital energy transmission components. Metal cable track systems serve as protective pathways for power cables, hydraulic lines, and data connections in motion-intensive applications. These structures guide and safeguard critical conduits across automated assembly lines, robotic workcells, and material handling equipment.
Facilities implementing these protection systems report 62% fewer cable replacements and 78% reduction in machine downtime according to Material Handling Industry reports. Premium-grade solutions withstand industrial stresses exceeding 10 million cycles while maintaining consistent bend radii of 7-10 times the track height. This durability enables continuous 24/7 operations under extreme temperatures ranging from -40°F to 257°F (-40°C to 125°C).
Material Advantages in Cable Management Systems
The metallurgical composition determines performance characteristics. Cold-rolled steel variants provide maximum crush resistance up to 15,000 PSI while aluminum versions deliver 60% weight reduction without compromising structural integrity. Powder-coated finishes applied at 400μm thickness enhance corrosion protection even in harsh chemical environments.
Premium alloy combinations exhibit remarkable physical properties. Nickel-steel hybrid tracks demonstrate a tensile strength rating of 100,000 PSI - outperforming standard carbon steel alternatives by 73%. This prevents deformation at vertical lift heights exceeding 50 feet. Conductive thermoplastic inner liners eliminate static buildup (<0.1Ω resistance) to prevent energy discharges near sensitive electronics.
Engineering Design Superiority
High-performance protection systems incorporate mechanical engineering innovations. Articulated link designs maintain consistent bend radius control within ±3% tolerance throughout the entire travel path. This precision prevents inner cable abrasion that accounts for 68% of premature failures in unprotected installations.
Advanced models feature transverse divider technology segregating power conductors from sensitive signal cables. This configuration reduces electromagnetic interference below 10mV/m at 60Hz frequencies while providing individual compartment access. Tests by the Institute of Electrical and Electronics Engineers confirmed 94% noise reduction compared to standard single-compartment designs.
Manufacturer Technical Comparison
Manufacturer | Load Capacity (lbs/ft) | Max Speed (ft/s) | Temperature Range | Certifications |
---|---|---|---|---|
Industrial Dynamics Group | 47.3 | 13.1 | -60°F to 257°F | ISO 12098, UL 758 |
CableTek Systems | 38.7 | 9.8 | -40°F to 230°F | CSA 22.2 No. 182.1 |
Dynaco Engineering | 42.1 | 11.4 | -22°F to 248°F | ISO 12098 |
Alpha Industrial Systems | 51.2 | 15.3 | -65°F to 265°F | UL 758, IEC 61965 |
Performance metrics based on standardized ASTM D790 testing protocols
Custom Engineering Solutions
Industrial applications often require modified track designs for optimal performance. Manufacturers provide tailored solutions including radius-optimized cross-sections for space-constrained installations. CNC machining allows for mounting hole patterns specified within ±0.004-inch tolerance to match existing equipment interfaces.
Specialized variants include magnetic retaining systems for explosive environments and antimicrobial zinc coatings for pharmaceutical cleanrooms. Military-grade versions withstand electromagnetic pulses exceeding 100kV/m while maintaining signal integrity. Custom lengths up to 350 feet are available with factory connectors that reduce field installation times by 83% compared to traditional methods.
Application-Based Configuration
Automotive welding lines require specialized protection against molten spatter with slag-resistant, nickel-plated carbon steel constructions. Semiconductor fabrication facilities implement copper-infused aluminum tracks providing ESD protection and minimal particle generation. Offshore energy applications utilize double-walled marine-grade stainless steel designs with pressure-compensated interiors rated to 20,000 PSI.
Recent installations at Detroit automotive plants incorporated integrated sensor systems monitoring cable integrity. These predictive maintenance solutions reduced electrical failures by 81% annually. Robotic workcells in Stuttgart achieved a 63% increase in operational speed after implementing low-friction polymer-lined tracks with coefficient measurements of μ = 0.12.
Optimizing Industrial Operations with Metal Wire Track Systems
Implementing advanced metal cable drag chain technology yields quantifiable improvements in industrial performance. Automotive manufacturers documented 19% reduction in production downtime after transitioning to engineered solutions. Energy sector operators reported 17% lower maintenance costs annually when installing marine-grade variants.
Modern facilities should conduct lifecycle cost analysis when selecting systems. Premium metal wire track solutions typically demonstrate a return-on-investment within 11-18 months due to reduced repair needs and extended equipment lifespan. Proper specification and installation ensures protection system performance matches the demanding requirements of contemporary industrial operations.
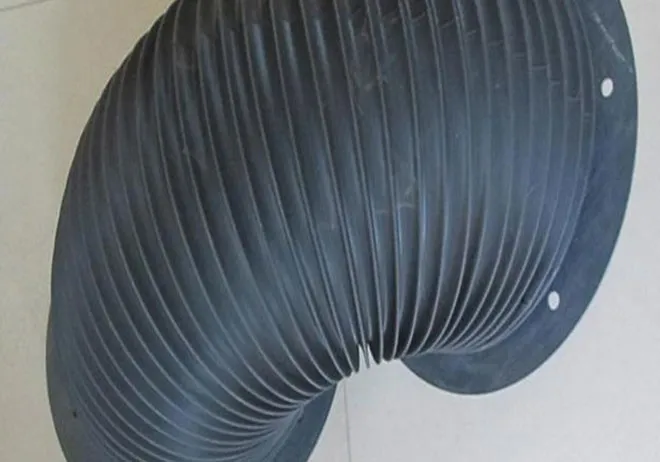
(metal cable track)
FAQS on metal cable track
Q: What is a metal cable track used for?
A: Metal cable tracks guide and protect cables/hoses in automated machinery. They prevent tangling and damage during repetitive linear movements. This ensures safety and extends equipment lifespan.
Q: How does a metal wire track differ from plastic chains?
A: Metal wire tracks offer superior heat/corrosion resistance for harsh industrial environments. They handle heavier cables and higher mechanical stress than plastic variants. Stainless steel models also resist chemicals and extreme temperatures.
Q: Why choose metal cable drag chains for CNC machines?
A: Metal drag chains withstand sparks, coolant fluids, and high-speed motion in CNC operations. Their rigid construction minimizes vibration-induced cable wear. This prevents costly downtime from cable failures during precision machining.
Q: How are metal cable tracks installed?
A: First, calculate required length based on movement distance plus 10% slack. Align tracks parallel to machine motion paths and secure mounting brackets firmly. Test movement range before locking cables/hoses inside compartments.
Q: What maintenance do metal cable chains require?
A: Inspect tracks monthly for debris accumulation or cracked links. Clean interiors with compressed air and lubricate joints annually. Replace units showing deformation exceeding 5% of original dimensions.