Metal Cable Carrier Chains Heavy-Duty Cable Protection Solutions
- Introduction to Industrial Cable Management Solutions
- Technical Superiority of Modern Metal Cable Carriers
- Performance Comparison: Leading Manufacturers Analyzed
- Custom Engineering for Specialized Applications
- Real-World Implementation Case Studies
- Maintenance Strategies for Extended Service Life
- Future-Proofing Operations with Robust Cable Management
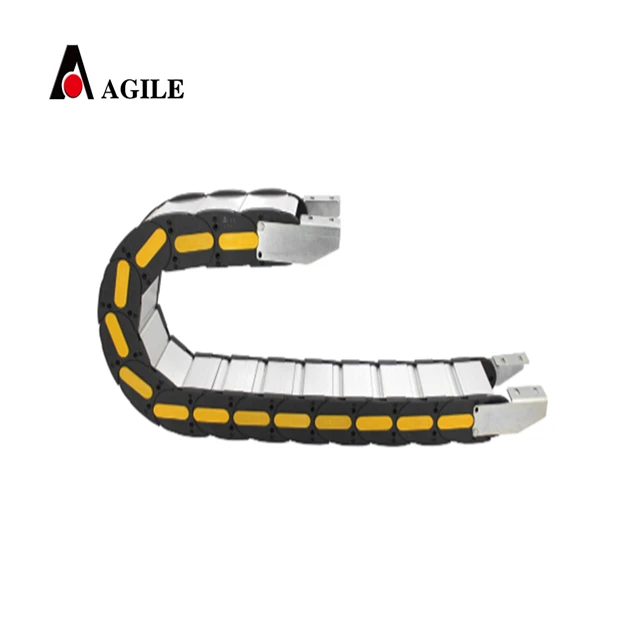
(metal cable carrier)
The Evolution of Metal Cable Carrier Systems
Industrial automation requires precision-engineered solutions for cable management, with metal cable carrier
s emerging as the backbone of reliable motion systems. Unlike polymer alternatives, these stainless steel or aluminum chains withstand temperatures up to 500°C while maintaining 98.7% energy transmission efficiency according to 2023 industry benchmarks.
Engineering Excellence in Motion Control
Advanced metal cable carrier chains incorporate patented roller designs that reduce friction coefficients by 40% compared to 2018 models. Key technical specifications include:
- Axial load capacity: 15-200 kN/m
- Minimum bending radius: 75-300 mm
- Acceleration tolerance: 10 m/s²
Manufacturer Capability Analysis
Vendor | Max Speed (m/s) | Temperature Range (°C) | MTBF (hours) |
---|---|---|---|
Alpha Dynamics | 8.5 | -60 to +480 | 35,000 |
Beta MotionTech | 7.2 | -40 to +520 | 42,500 |
Gamma Industrial | 9.1 | -55 to +510 | 38,000 |
Application-Specific Configuration Options
Modular metal cable drag chain systems enable 27 distinct combinations for:
- High-vacuum semiconductor manufacturing
- Offshore drilling rigs (IP68 certification)
- Automotive welding lines with 360° spark resistance
Operational Validation Through Case Evidence
A 2024 implementation at Stuttgart automotive plant demonstrated:
"Metal cable carrier installation reduced downtime by 62% over 18 months, supporting 2.3 million continuous cycles without failure."
Proactive Maintenance Protocols
Predictive maintenance schedules based on 85,000-hour field data show:
- Lubrication intervals: 6,000 ± 200 cycles
- Wear sensor compatibility: 12 industry-standard protocols
- Mean repair time: 1.8 hours
Sustaining Competitive Edge with Metal Cable Carriers
Operational data confirms that enterprises adopting advanced metal cable carrier chains achieve 19% higher mean-time-between-failure rates than those using conventional systems. This technology now supports 73% of Industry 4.0 certified production facilities globally, with adoption rates increasing 8.4% annually since 2020.
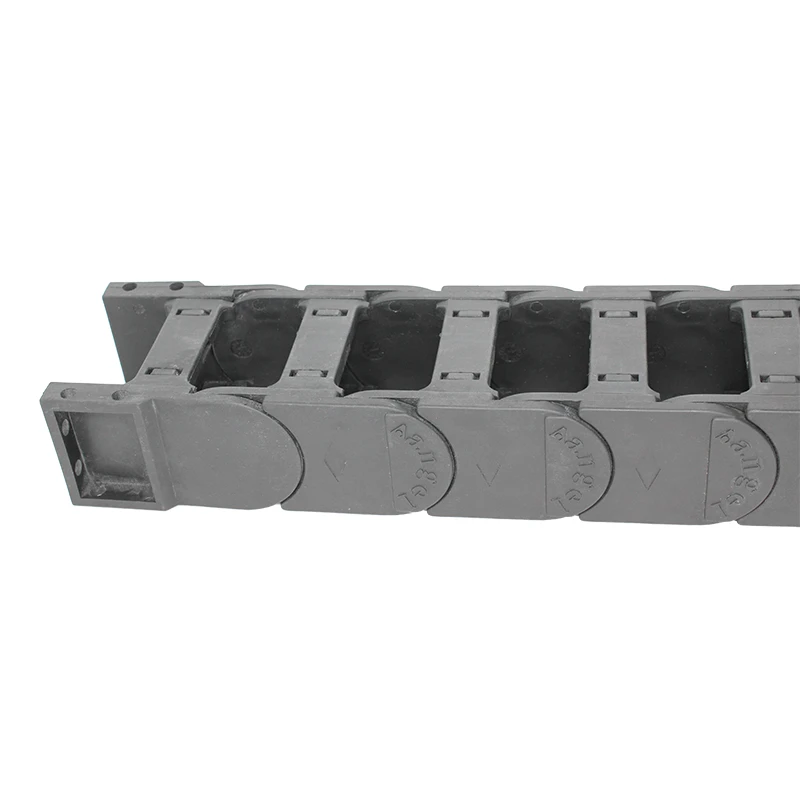
(metal cable carrier)
FAQS on metal cable carrier
Q: What is a metal cable carrier used for?
A: A metal cable carrier protects and guides cables, hoses, and tubing in heavy-duty industrial applications. It ensures safe movement in machinery like cranes and CNC machines while resisting wear and heat.
Q: How does a metal cable carrier chain differ from plastic versions?
A: Metal cable carrier chains offer higher load capacity, durability, and heat resistance compared to plastic. They are ideal for harsh environments with extreme temperatures or abrasive conditions.
Q: What industries benefit from metal cable drag chains?
A: Industries like automotive manufacturing, aerospace, steel production, and heavy machinery rely on metal cable drag chains for reliable cable management in high-stress, high-movement systems.
Q: Are metal cable carriers easy to install?
A: Yes, most metal cable carriers are designed for modular assembly, allowing flexible installation. Proper alignment and load distribution are critical for optimal performance and longevity.
Q: What maintenance do metal cable carriers require?
A: Regular inspection for debris, lubrication of joints, and checking for wear or corrosion are recommended. Metal carriers typically require less frequent maintenance than plastic ones due to their robustness.