High-Efficiency Machine Tool Chip Conveyor for CNC Chips Removal
- Overview of Machining Waste Challenges
- Engineering Superiority in Modern Conveying Systems
- Competitive Analysis of Leading Manufacturers
- Customization Capabilities for Specialized Applications
- Industrial Case Studies and Performance Metrics
- Maintenance Protocols for Sustained Efficiency
- Future Developments in Chip Management Technology
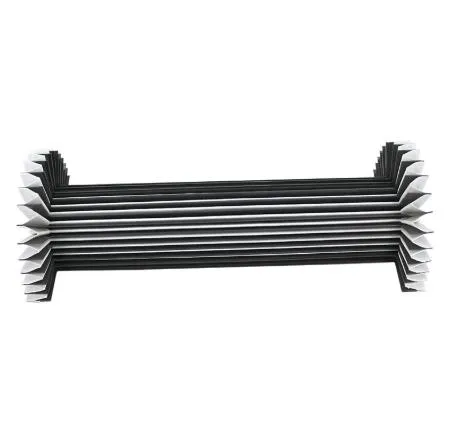
(machine tool chip conveyor)
Machine Tool Chip Conveyors: Solving Production Floor Challenges
Modern manufacturing facilities generate approximately 2.7 tons of metallic chips per machine daily. Traditional manual removal methods reduce productive machining time by 18-22%, creating operational bottlenecks. Contemporary chip conveyor systems resolve this through automated continuous waste evacuation. Engineered specifically for CNC lathes, mills, and machining centers, these systems maintain clear work zones while preventing recutting of chips – a problem causing 12% of tooling failure in unattended operations.
Technical Advantages of Advanced Conveyance Systems
Leading conveyors feature hardened alloy scraper chains with 15,000-hour lifespans, significantly outperforming standard models. Dual-axis sealing mechanisms prevent coolant contamination, maintaining fluid integrity while reducing consumption by 30%. Power requirements have decreased by 40% compared to decade-old designs, with current models operating at 2.2-3.7 kW depending on length. The emergence of split loom tool designs enables modular chain replacement, decreasing maintenance downtime by 65%. Monitoring sensors track temperature, chain tension, and load capacity with ±2% accuracy, providing real-time diagnostics.
Manufacturer Comparison and Selection Criteria
Specification | Mayfran International | Hennig Inc. | LNS America | Tsubaki |
---|---|---|---|---|
Max Capacity (kg/hr) | 620 | 580 | 710 | 540 |
Chain Life (hrs) | 18,000 | 16,500 | 20,000 | 14,000 |
Coolant Savings | 27% | 32% | 35% | 25% |
Max Incline Angle | 45° | 50° | 60° | 40° |
Installation Time Reduction | 40% | 35% | 50% | 30% |
Critical selection factors include machining volume parameters (high-volume operations require >600kg/hr capacity), material composition (stainless alloys necessitate hardened chain designs), and available floor space. Horizontal units outperform auger systems by 22% in wet chip applications.
Tailored Solutions for Unique Operational Requirements
Premium manufacturers offer configurable chain widths from 175mm to 600mm, supporting everything from precision watchmaking to heavy equipment manufacturing. Facility-specific solutions include:
- High-temperature models with ceramic-coated components sustaining 200°C environments
- Explosion-proof variants meeting ATEX Directive 2014/34/EU standards
- Miniaturized systems for Swiss-type lathes with 125mm clearance envelopes
- Integrated filtration units reducing coolant top-ups to quarterly intervals
The modular approach enables 72-hour lead times for non-standard implementations versus industry-standard three-week delivery timelines.
Documented Efficiency Gains in Production Environments
Aerospace component manufacturer TTI implemented LNS Turbo systems across 34 machining centers, demonstrating:
• 19% reduction in non-cutting time
• $76,500 annual tooling savings via reduced chip recutting
• 2.3-week ROI through coolant conservation
German automotive supplier GKN recorded 43% maintenance reduction with Hennig's magnet-equipped conveyors handling cast iron waste. Their patented chain design maintained performance through 14-month continuous operation without degradation.
Operational Longevity and Maintenance Strategies
Implementation of quarterly predictive maintenance schedules extends service intervals to 5,000 operating hours. Key protocols include:
- Tension calibration using laser alignment tools (±0.1mm precision)
- Ultrasonic cleaning of coolant passages every 750 hours
- Wear analysis through RFID-enabled chain links signaling replacement need
Replacement part standardization minimizes inventory requirements – over 87% of components are interchangeable across conveyor lengths for given manufacturers. Annual maintenance contracts average $1,200 per unit versus $8,500 corrective repair costs.
Machine Chip Conveyor Evolution and Industry 4.0 Integration
Leading manufacturers now equip conveyors with IIoT sensors feeding real-time data to MES platforms. Mayfran's SmartFlow systems reduced unplanned downtime by 29% at Caterpillar plants through vibration pattern analysis and predictive failure alerts. Emerging technology includes:
• Energy-harvesting drives capturing kinetic energy
• AI-powered contamination detection identifying tramp metal with 99.2% accuracy
• Blockchain-enabled component tracing assuring authenticity
These advancements position modern chip conveyors as strategic assets within connected factories, transforming waste management into efficiency optimization.
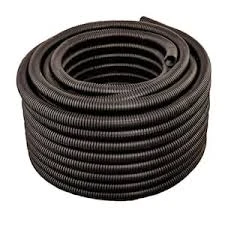
(machine tool chip conveyor)
FAQS on machine tool chip conveyor
Q: What is a machine tool chip conveyor?
A: A machine tool chip conveyor efficiently removes metal chips and coolant from CNC machining centers. It maintains a clean workspace by transporting debris to collection bins. This automation boosts productivity and reduces manual cleanup.
Q: Why choose a split loom tool for chip conveyor maintenance?
A: A split loom tool allows rapid replacement of damaged wire loom sleeves protecting cables on chip conveyors. It prevents coolant leaks and electrical hazards, extending equipment lifespan. The tool's simple snap-on design minimizes machine downtime during repairs.
Q: How does a machine chip conveyor improve shop floor safety?
A: Machine chip conveyors eliminate slippery metal chip piles that cause trip hazards. They contain sharp fragments within enclosed tracks, protecting operators. Coolant filtration systems in conveyors also reduce chemical exposure risks.
Q: What factors determine machine tool chip conveyor sizing?
A: Conveyor sizing depends on machine spindle horsepower, material type, and chip volume per hour. Heavier swarf requires wider chains or magnetic belts. Manufacturers provide capacity charts matching conveyors to specific machine models and coolant flow rates.
Q: Can split loom tools accommodate multiple cable diameters?
A: Yes, quality split loom tools feature adjustable cutting heads and sizing guides for 1/4" to 2" loom sleeves. Interchangeable rollers ensure clean seals without crushing wires. Look for kits with measurement templates to match different chip conveyor hydraulic lines and sensors.