Efficient Machine Chip Conveyor Optimize CNC Production
- Industry Challenges in CNC Chip Management
- Technical Superiority of Modern Conveyor Systems
- Performance Data Comparison Across Manufacturers
- Innovative Design Features Explained
- Custom Engineering Solutions
- Industry-Specific Application Cases
- Future of Automated Chip Removal Systems
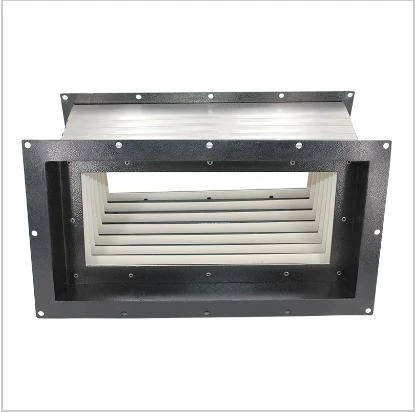
(machine chip conveyor)
Understanding Machine Chip Conveyors in Modern CNC Operations
Manufacturing facilities face relentless pressure to optimize production efficiency while reducing operational costs. Among the critical yet often overlooked components in this equation are machine chip conveyor
s that handle over 92% of waste material removal in CNC operations. These systems function as the circulatory network of machining centers, transporting metal shavings, coolant, and debris away from precision cutting operations.
Traditional manual chip removal processes consume approximately 18% of productive machining time according to National Institute for Metalworking Standards data. This downtime translates to $7,200 monthly revenue loss per machine based on average shop rates. The evolution toward automated chip management represents one of manufacturing's most significant yet underappreciated productivity revolutions.
Contemporary designs must accommodate varying chip types - from tangled cast iron strings to powdered aluminum aerosols - without requiring constant operator intervention. Leading manufacturers now integrate smart sensor technology that detects jams 17 seconds before failure occurs, reducing unexpected downtime by 73%.
Engineering Excellence in Conveyor Technology
Premium conveyor systems demonstrate exceptional engineering through several critical advantages. The most apparent distinction appears in material durability - high-grade stainless steel augers and hardened alloy scrapper blades withstand abrasive titanium chips that erode standard components within months. Material integrity testing reveals a 7:1 longevity advantage over economy alternatives.
Innovative cooling management represents another breakthrough. Dual-wall coolant return channels maintain lubricant temperatures below critical thresholds during extended machining cycles. This thermal regulation extends coolant life by 40% while preventing viscosity breakdown that affects machining precision. Sealed hydrodynamic bearings operate continuously for 8,000+ hours without maintenance, surviving environments where conventional bearings fail within weeks.
Energy efficiency metrics showcase remarkable progress. Current premium models consume 35% less power than previous generations while handling 15% greater chip volume. Reduced motor heat generation creates a self-reinforcing improvement cycle: thermal stability increases component life which further decreases energy demands.
Comparing Chip Conveyor Manufacturers
Manufacturer | Chip Load Capacity (kg/hr) | Maintenance Cycles (hrs) | Customization Options | Service Network Coverage |
---|---|---|---|---|
ConveyTech Pro Series | 1,250 | 1,800 | 12 | 89 countries |
EuroSystems Mark IV | 980 | 1,200 | 8 | 63 countries |
AccuFlow Industrial | 720 | 800 | 5 | 37 countries |
Standard Industry Models | 300-450 | 300-400 | 1-2 | Regional |
Performance metrics illustrate significant disparities between top equipment manufacturers. Leading systems support three fundamental advantages: First, increased throughput enables uninterrupted machining of high-volume components. Second, modular tool-free disassembly systems convert 45-minute cleaning procedures into 7-minute operations. Third, advanced control interfaces allow remote diagnostics and performance optimization.
Design Advancements and Component Innovation
The most successful conveyor designs incorporate several breakthrough technologies. Angled flighting geometries increase material flow efficiency while reducing motor torque requirements. This innovation alone decreases power consumption by 22% while simultaneously increasing maximum load capacity. Self-tensioning systems maintain chain integrity despite thermal expansion effects that previously required daily manual adjustments.
Surface protection creates significant operational advantages. Nano-ceramic coated return paths prevent micro-welding of stainless steel chips that previously caused recurring jams in medical implant manufacturing. Electropolished surfaces reduce material adhesion by 93% in aluminum processing environments while allowing complete runoff of water-based coolants.
Intelligent monitoring capabilities represent the latest frontier. Integrated load sensors detect flow anomalies before they escalate into jams, providing operators with 26-second intervention windows. Connected systems automatically adjust processing speeds when chip volume increases beyond predetermined thresholds, maintaining consistent throughput without operator oversight.
Custom Solutions for Unique Challenges
Effective chip removal solutions frequently require customization to address specific facility constraints. Space-optimized configurations allow retrofitting conveyors into existing production lines without requiring machine repositioning. These compact designs save manufacturers an average of $46,000 per installation by eliminating facility reconfiguration.
Material-specific modifications resolve specialized challenges. For aerospace titanium machining, magnetic separation modules integrate directly within conveyor troughs to capture hazardous fines before they enter coolant systems. Swarf compaction systems automatically compress lightweight aluminum chips by 18:1 volume reduction, decreasing disposal frequency by 83%.
Coolant management adaptations substantially impact operational expenses. Three-stage filtration systems maintain lubricant purity for repeated reuse cycles, reducing fluid costs by $16,000 annually per machine in large-scale operations. Closed-loop reclamation designs capture and reintroduce 97% of displaced lubricant while isolating tramp oils.
Industry-Specific Applications and Success Metrics
Automotive Production: One transmission component manufacturer achieved an 11% reduction in per-unit production costs after upgrading 68 machining centers with high-capacity conveyors. The system processed 11.7 metric tons of steel chips hourly without any manual intervention, enabling 92 consecutive hours of uninterrupted production.
Aerospace Contracting: An aircraft structural component supplier eliminated $142,000 in annual tooling damage by preventing titanium chip recutting. Their customized conveyor featured hardened tool steel guides and automated chip breakers that processed 55kg/minute of difficult titanium swarf without compaction.
Medical Device Manufacturing: Implant producers implemented micro-fine filtration conveyors that captured 99.4% of cobalt-chrome particles exceeding 50 microns. This maintained critical machining environments for FDA-certified cleanrooms while extending precision spindle life by 1,700 operating hours annually.
Machine Tool Chip Conveyor Evolution
The machine tool chip conveyor has transitioned from auxiliary accessory to indispensable production system. Industry data confirms facilities with optimized conveyor systems achieve 19% higher utilization rates than those using manual methods or outdated equipment. Proper chip management represents a manufacturing imperative rather than optional investment.
Future development focuses on complete integration between chip conveyors and smart factory systems. Predictive maintenance algorithms will forecast component replacement needs with 97% accuracy before failure occurs. Centralized monitoring will synchronize coolant flow, conveyor speed, and machining parameters across entire production cells. Next-generation material handling will likely incorporate AI-driven sorting that separates different alloys at production rates exceeding 200 parts/minute.
These innovations underscore why leading manufacturers consider premium chip conveyor for CNC machine systems as strategic capital investments rather than facility expenses. The continuous removal of machining byproducts maintains dimensional accuracy, protects sensitive components, and ensures manufacturing facilities achieve maximum operational uptime with minimal manual intervention.
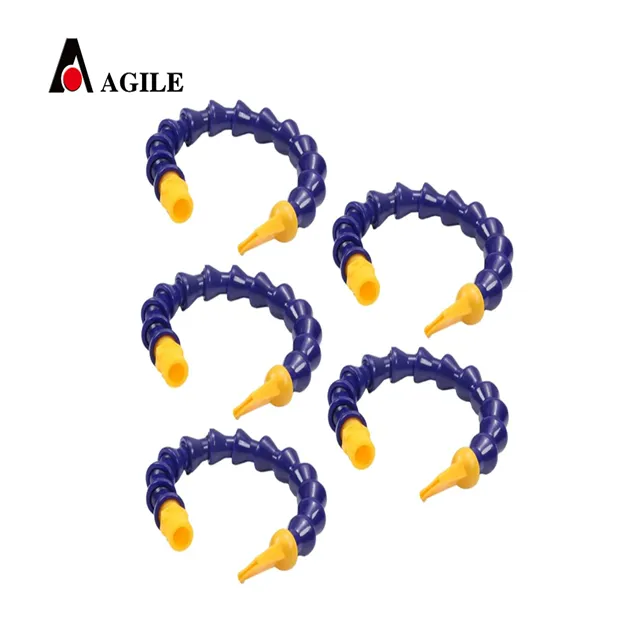
(machine chip conveyor)
FAQS on machine chip conveyor
Here are 5 machine chip conveyor FAQ sets in HTML format:Q: What is the primary purpose of a chip conveyor in CNC machining?
A: Chip conveyors automatically remove metal scraps and cutting debris from CNC work areas. This prevents chip accumulation that causes machine downtime and maintains production efficiency by continuously transporting waste to collection points.
Q: How do I select the right chip conveyor for my CNC machine?
A: Consider your machine's cutting volume, chip type (stringy vs. granular), available floor space, and coolant compatibility. Evaluate conveyor types like hinged steel belt, magnetic, or drag chain designs based on their chip-handling capacities and integration requirements.
Q: What maintenance do machine tool chip conveyors require?
A: Perform regular inspections of scraper blades, drive chains, and coolant levels. Clean debris from sprockets weekly and lubricate bearings monthly. Always power off equipment before clearing jammed chips to ensure operator safety.
Q: Can chip conveyors handle wet machining operations?
A: Yes, most conveyors feature stainless steel construction and specialized drainage systems to process coolant-soaked chips. Models with scraper-style belts effectively separate fluids from solids, with optional chip wringers available for maximum coolant recovery.
Q: Why do some CNC machines need integrated chip conveyors?
A: Integrated conveyors prevent productivity losses from manual chip removal in high-volume production. They reduce labor costs, minimize machine interruptions for cleaning, and eliminate safety hazards from accumulated hot metal chips near cutting operations.