Innovative Solutions for Efficient Cable Carrier System Design and Implementation
Cable Carrier Systems An Overview
In today's industrial landscape, efficient management of cables is a crucial aspect of maintaining operational productivity and safety in various environments. Enter cable carrier systems, also known as cable drag chains or energy chains, which are instrumental in organizing and protecting cables and hoses that move or flex during machine operation. With a variety of applications across sectors such as manufacturing, aerospace, and automotive, these systems have become integral to modern engineering solutions.
What are Cable Carrier Systems?
Cable carrier systems are protective structures that house and guide cables and hoses as they move. They consist of interlinked segments that create a flexible chain-like configuration, allowing for movement along a predetermined path while minimizing wear and tear on the cables. This is particularly important in environments where cables may be subject to bending, twisting, or other forms of mechanical stress.
The primary function of these systems is to ensure that cables and hoses remain organized, prevent tangling, and protect them from potential damage due to environmental factors or mechanical movement. By doing so, cable carrier systems not only prolong the lifespan of cables but also enhance operational efficiency by reducing downtime related to maintenance and repairs.
Applications of Cable Carrier Systems
Cable carrier systems find their utility in a broad range of applications. In manufacturing environments, they are often utilized in assembly lines, CNC machines, and robotic arms, where dynamic movement is a constant factor. By securing cables in cable carriers, manufacturers can avoid costly disruptions due to cable-related issues, leading to more streamlined operations.
In the aerospace sector, these systems help manage cabling in aircraft, ensuring that vital communication and control systems function seamlessly, even during high-stress maneuvers. Similarly, the automotive industry employs cable carriers in assembly plants and robotic welding stations, where precise and uninterrupted movement is essential for high-quality production.
cable carrier systems
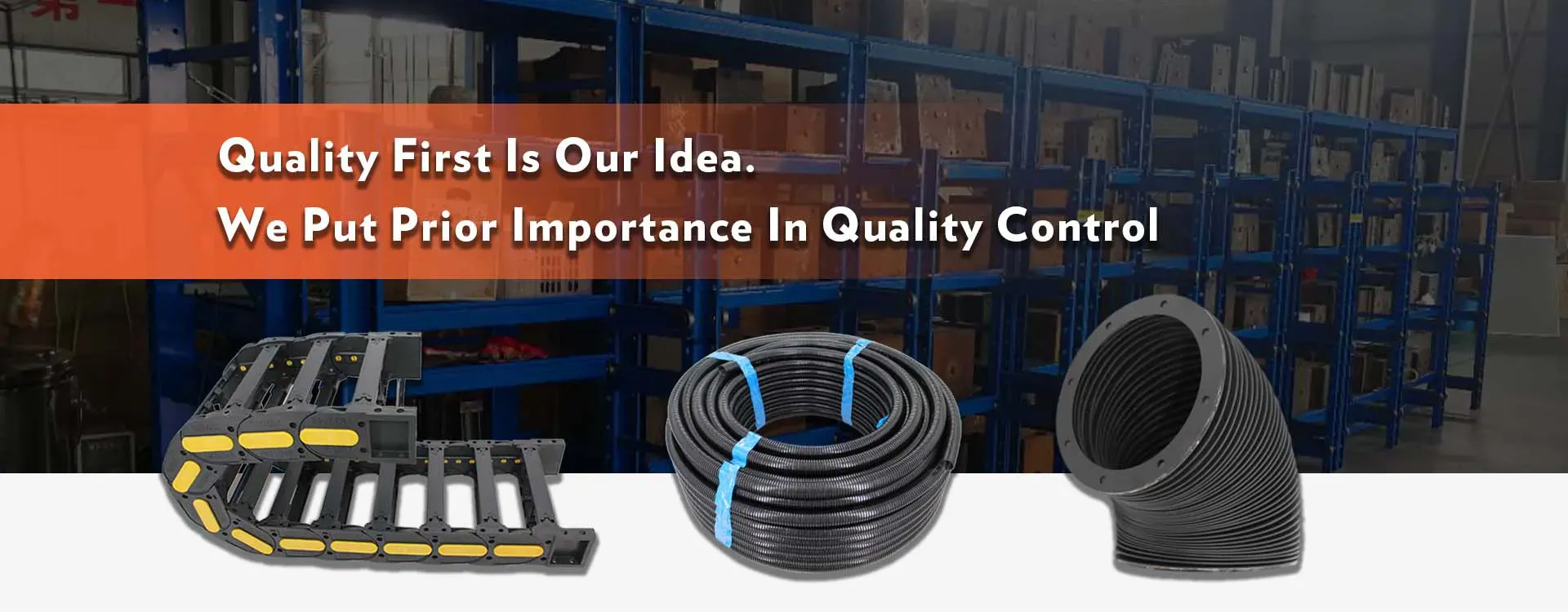
Beyond industrial use, cable carrier systems are also found in entertainment settings, such as theaters or concert venues, where they manage the complex rigging of lights and audio equipment
. Their versatility makes them invaluable across these diverse settings.Advantages of Using Cable Carrier Systems
The benefits of incorporating cable carrier systems into operational frameworks are significant. Firstly, they enhance safety by preventing cable damages that can lead to electrical hazards. Secondly, the organization of cables through these systems leads to a cleaner workspace, which is essential for optimizing productivity and maintaining an efficient workflow.
Additionally, cable carrier systems come in various sizes and materials, allowing customization for specific applications. They can be made from durable plastics, metals, or composite materials, each offering different advantages such as weight, strength, and resistance to environmental factors like temperature and chemicals.
Moreover, the ease of installation and maintenance further contributes to their appeal. Many modern cable carrier systems are designed for tool-free assembly and disassembly, making it easy to adjust configurations or replace cables as needed.
Conclusion
In summary, cable carrier systems represent a significant advancement in the management of industrial cables and hoses. Their role in enhancing safety, efficiency, and organization cannot be overstated, particularly in environments where dynamic movement is a norm. As industries continue to evolve and become more reliant on complex machinery and automation, the importance of cable carrier systems will only increase, cementing their status as an essential component of modern engineering solutions. With ongoing innovations in their design and application, these systems will undoubtedly continue to play a pivotal role in shaping the future of industrial operations.