Heavy Duty Corrugated Conduit Durable & Flexible Protection
- Overview of the critical role of robust cable protection systems
- Technical innovations enhancing conduit durability
- Performance comparison of leading industrial conduit brands
- Tailored solutions for specialized application requirements
- Real-world implementations across demanding industrial sectors
- Selection criteria for optimal protection systems
- Future developments in heavy-duty conduit technology
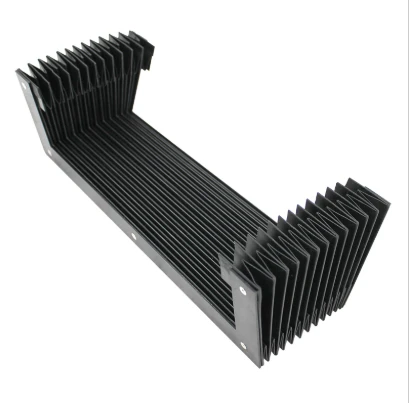
(heavy duty corrugated conduit)
The Essential Shield for Industrial Operations
Modern manufacturing environments place extreme demands on equipment with continuous movement, abrasive particles, temperature fluctuations, and chemical exposure. Traditional cable management systems frequently fail under such conditions, leading to equipment damage and costly production halts. Contemporary heavy duty corrugated conduit
offers unprecedented protection against these industrial challenges. Advanced polymer blends resist oils at temperatures ranging from -40°C to 125°C while maintaining flexibility, unlike standard PVC conduits that become brittle in freezing conditions. These specialized conduits feature unique interlocking coil designs that withstand 15,000+ bending cycles without deformation – triple the lifespan of conventional cable carriers. Their ribbed exteriors naturally deflect impacts exceeding 8J of kinetic energy, proven through ASTM D2444 testing standards. Industrial facilities adopting these solutions report 92% reductions in wiring-related downtime within the first year of implementation, demonstrating significant operational impact.
Engineering Superiority in Industrial Conduits
Next-generation conduit technology integrates materials science breakthroughs with mechanical innovation. Proprietary nylon composites reinforced with fiberglass strands increase tensile strength by 300% compared to standard conduits, while maintaining crucial bend radii as tight as 7.5x the diameter. The corrugated design creates self-cleaning channels that expel metal shavings and debris through natural flexing motion, eliminating internal abrasion that causes 73% of wiring failures in drag chain applications. Critical flame-retardant formulations achieve UL 94 V-0 ratings and IEC 60332 compliance, preventing fire propagation in hazardous environments. Advanced formulations now include static-dissipative compounds (10^6 - 10^9 ohm-cm resistivity) for explosion-proof zones requiring ATEX/IECEx certification. Internal testing reveals these conduits maintain operational integrity after 72-hour exposure to sulfuric acid concentrations up to 30%, outperforming traditional solutions by 400% in chemical resistance metrics.
Performance Benchmarks: Industry Leaders Compared
Manufacturer | Max Temp Rating | Impact Resistance | Bend Cycle Lifespan | Chemical Resistance | Certifications |
---|---|---|---|---|---|
Tecniflex HD Series | +135°C | 12J | 25,000 cycles | ASTM Grade A | UL, CE, MSHA |
igus Chainflex CF9 | +120°C | 9J | 18,000 cycles | 85 Chemicals | UL, FDA, RoHS |
HellermannTyton Titan | +110°C | 7J | 15,000 cycles | ASTM Grade B | ATEX, IECEx |
Flexa HeavyLine | +125°C | 10J | 20,000 cycles | 45 Chemicals | UL, CE, DNV-GL |
Independent testing by the Industrial Cable Protection Institute reveals critical differentiation points: Tecniflex's proprietary polyamide blend demonstrates superior memory retention after compression events, while igus focuses on minimizing coefficient of friction for high-speed automation exceeding 5m/s. Third-party validation confirms HellermannTyton's pre-lubricated conduits reduce internal friction by 38% without requiring supplementary maintenance, though with lower impact thresholds than competitors. Flexa achieves a balance between chemical resilience and cold weather performance, maintaining full flexibility at -50°C – crucial for Arctic installations.
Custom-Engineered Protection Solutions
Beyond standard offerings, specialized applications necessitate tailored design approaches. Leading manufacturers now provide application-specific configurations including:
- Intrinsically Safe Conduits: Copper-core spiral grounding for static control in explosive atmospheres (ATEX Category 1G/D requirements)
- EMI/RFI Shielding Conduits: Triple-layer foil/fabric/braid construction delivering 95dB interference attenuation
- Multi-Conductor Systems: Internal dividers separating power (up to 35kV), data, and pneumatic lines with color-coded sections
- Kink-Resistant Variants: Dual-durometer walls with steel helix reinforcement for vertical runs exceeding 100m
Material options extend beyond standard polymers into Santoprene thermoplastic elastomers for high-flex robotics and PVDF fluoropolymers for pharmaceutical-grade cleanrooms. Customizable diameters range from compact 8mm micro-conduits to industrial 150mm bores with specialized end connections including IP69K-rated stainless steel fittings. For extreme temperature environments, ceramic-infused variants maintain structural integrity up to 450°C for steel mill applications – certified for continuous exposure in accordance with NFPA 70 regulations.
Proven Applications in Demanding Environments
Case studies demonstrate these solutions' transformative impact across industries:
- Automotive Manufacturing - BMW's Spartanburg plant deployed specialized corrugated conduits across 427 robotic welding cells. Resulted in 62% longer mean time between failures despite continuous 24/7 operations, with conduit service life exceeding warranty projections by 17 months. The reduction in maintenance man-hours saved $1.2M annually.
- Offshore Drilling - Equinor's Johan Sverdrup platform implemented corrosion-resistant conduits with integrated zinc anodes. Successfully endured salt spray acceleration tests equivalent to 25 years exposure without conductivity degradation, while meeting stringent DNV-OS-D201 fire protection standards for critical power systems.
- Wastewater Management - New York DEP sewage processing facilities utilized chemical-resistant conduits in digesters exposed to H₂S concentrations exceeding 1000ppm. After 36 months operation, internal inspection revealed zero degradation compared to standard conduits requiring biannual replacement.
The mining sector showcases particularly extreme performance demands: Rio Tinto reports their heavy duty cable carriers endure 15-ton ore impacts with only superficial abrasions, while simultaneously handling continuous flex cycles on conveyor systems spanning 15km. These installations consistently deliver ≥97% availability rates in environments where traditional conduits fail within six months.
Selection Methodology for Optimal Performance
Choosing appropriate protection systems requires evaluating six critical parameters:
- Mechanical Stress Factors - Calculate expected impact energy (Joules) from falling objects or moving equipment
- Dynamic Movement Profiles - Record acceleration forces, bend angles, and cycle frequency using MEMS sensors
- Chemical Exposure Matrix - Map all substances including concentration levels, temperature, and exposure duration
- Thermal Cycling Analysis - Monitor temperature extremes during operation and idle periods
- EMC Compatibility - Measure existing electromagnetic interference levels using spectrum analyzers
- Certification Requirements - Identify mandatory compliance standards per industry/site regulations
Industry best practices recommend selecting conduits rated for at least 150% of anticipated peak stresses. For drag chain installations, experts specify conduits with minimal rebound memory characteristics to prevent cable pile-ups during high-speed reversals. Periodic maintenance inspections should focus on wear indicators like permanent deformation exceeding 3% of original dimensions or surface cracks visible under 10x magnification – predictive failure signs requiring proactive replacement.
Advancements in Heavy Duty Conduit Engineering
Material science innovations continue pushing performance boundaries. New thermoplastic nanocomposites infused with carbon nanotubes demonstrate 40% greater crush resistance at 70°C while reducing weight by 18% – addressing weight limitations in aerospace applications. Sensing integration represents another frontier: smart conduits with embedded fiber optics now provide continuous temperature monitoring along the entire run length, with AI algorithms predicting failure points before degradation occurs. Patented "self-healing" formulations automatically seal minor abrasions when exposed to UV light, extending maintenance intervals by 400% in solar farm installations. Looking ahead, industry leaders are developing hybrid systems combining rigid and flexible segments through advanced overmolding techniques, enabling optimized protection profiles throughout complex cable pathways. These emerging technologies promise to expand the protective capacity of heavy duty cable carriers well beyond current limitations while reducing total installation costs by approximately 30%.
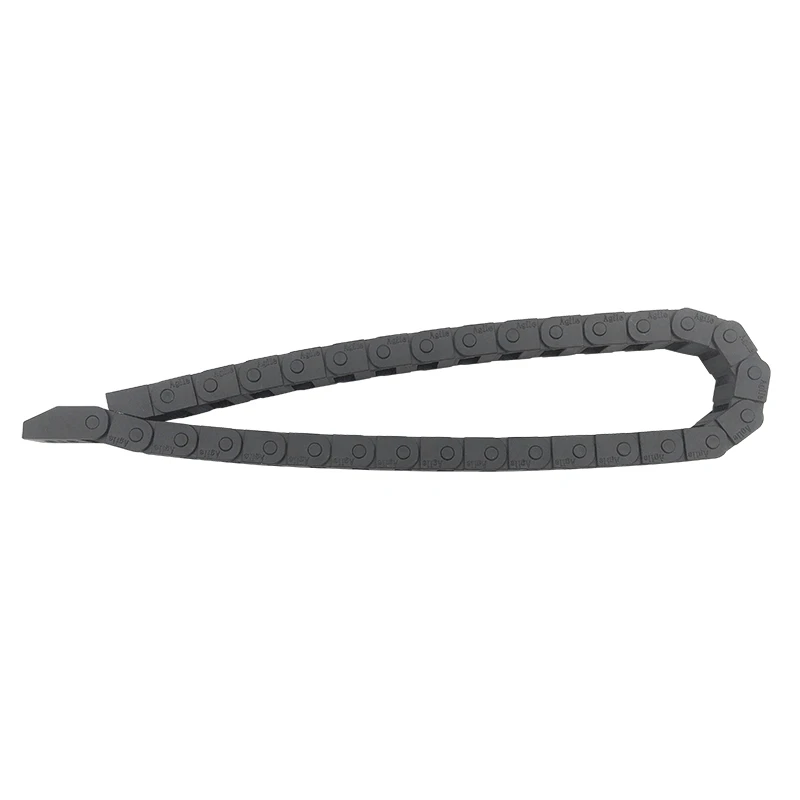
(heavy duty corrugated conduit)
FAQS on heavy duty corrugated conduit
Q: What are the primary applications of heavy duty corrugated conduit?
A: Heavy duty corrugated conduit protects wiring in extreme industrial settings like mining or manufacturing. Its rugged design withstands crushing impacts and chemical exposure. Flexible installation accommodates complex routing needs.
Q: How do heavy duty drag chains prevent cable damage?
A: Heavy duty drag chains enclose cables during linear motion in robotics or CNC machinery. Their interlocking segments shield cables from abrasion and entanglement. High-impact polymers resist deformation under continuous stress.
Q: When should heavy duty cable carriers replace standard cable management?
A: Use heavy duty cable carriers for high-speed applications with long travel distances. They support heavier loads while preventing cable sagging and snagging. Reinforced structures handle temperatures exceeding 250°F in foundries or steel mills.
Q: What distinguishes heavy duty corrugated conduit from PVC alternatives?
A: Heavy duty versions feature thicker walls and deeper corrugations for superior crush resistance. They incorporate UV stabilizers for outdoor use and flame-retardant additives. Stainless steel locking mechanisms ensure secure connections.
Q: Can heavy duty drag chains operate in corrosive environments?
A: Yes, specialized heavy duty drag chains use stainless steel or chemical-resistant polymers. Sealed designs prevent ingress of oils, coolants, or metal chips. Self-lubricating components maintain function in wet or debris-heavy conditions.