Flexible corrugated split sleeve tubing solution for optimal cable management and protection in various applications
The Versatility of Corrugated Split Sleeve Tubing in Modern Applications
In the ever-evolving landscape of industries, from telecommunications to aerospace, the demand for efficient, durable, and flexible solutions has never been greater. One such solution that has gained significant attention is corrugated split sleeve tubing. This innovative product stands out due to its unique design and multitude of applications, effectively addressing various needs across different sectors.
Understanding Corrugated Split Sleeve Tubing
Corrugated split sleeve tubing consists of a flexible, corrugated exterior that allows it to expand and contract, providing protection for wires and cables in a way that rigid tubing cannot. The split design facilitates easy installation and maintenance, as it can be opened and closed around existing cables without the need for disassembly. This not only saves time during installation but also enhances the adaptability of the tubing in situations where accessibility is crucial.
One of the key features of corrugated split sleeve tubing is its ability to resist environmental stressors. Made from high-quality materials such as polyethylene, PVC, or similar substances, it offers protection against moisture, UV rays, chemicals, and physical abrasions. Industries that operate in harsh environments, including construction, automotive, and oil and gas, have found this tubing to be invaluable in safeguarding their critical infrastructure.
Applications Across Diverse Industries
The versatility of corrugated split sleeve tubing allows it to be utilized in various applications
. In the telecommunications sector, for instance, it serves to protect cables from damage caused by weather conditions and mechanical wear. The tubing’s flexibility means it can accommodate the dynamic movements that cables endure, ensuring longevity and reliability.In the automotive industry, this type of tubing is often employed for harnessing and protecting critical wiring systems. The protective qualities of corrugated split sleeves help prevent short circuits caused by moisture intrusion or physical abrasion, ultimately enhancing the safety and performance of vehicles.
corrugated split sleeve tubing
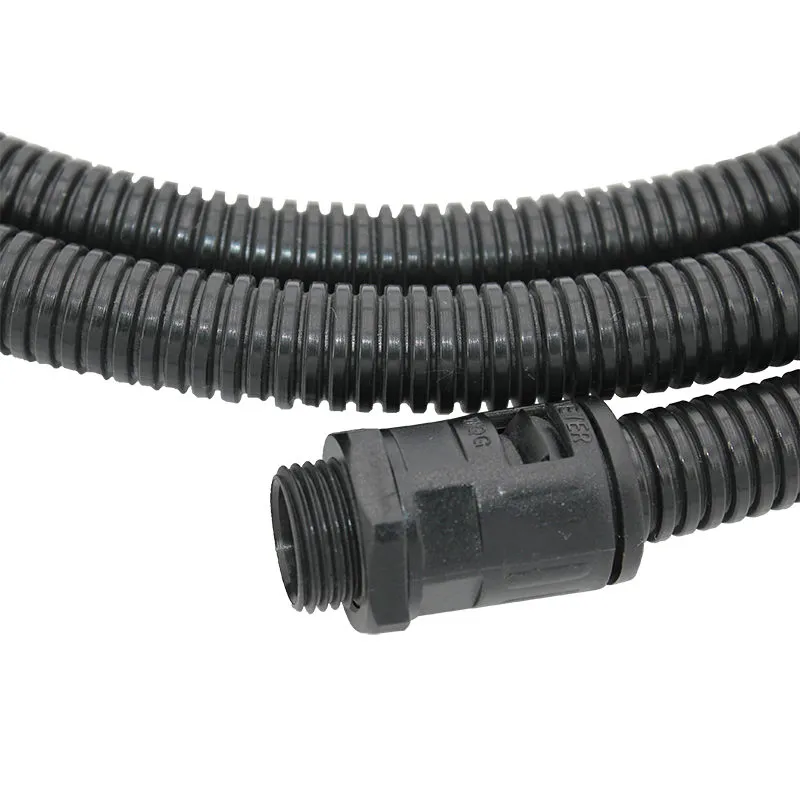
Moreover, in the aerospace sector, where weight and space are at a premium, corrugated split sleeve tubing offers an effective solution for cable management. Its lightweight design doesn't compromise on durability, providing essential protection for flight-critical wiring while maintaining the overall efficiency of the aircraft.
Benefits of Using Corrugated Split Sleeve Tubing
The benefits of integrating corrugated split sleeve tubing into projects are manifold. First and foremost is its ease of installation. The split design eliminates the need for extensive disassembly, allowing for quick replacements or upgrades. This characteristic is particularly beneficial for maintenance teams who need to perform their work efficiently and effectively without lengthy downtimes.
Additionally, the tubing’s ability to withstand various environmental challenges contributes to reduced maintenance costs over time. By preventing damage to cables and wires, businesses can avoid the significant expenses associated with repairs and replacements.
Another advantage is the enhanced cable organization it provides. In environments where multiple wires are routed together, corrugated split sleeve tubing can neatly bundle and protect these cables, reducing clutter and minimizing the risk of tangles or snags.
Conclusion
In summary, corrugated split sleeve tubing has emerged as a crucial component in modern industrial applications. Its unique properties of flexibility, durability, and resilience make it an ideal choice for protecting cables in a variety of environments. As industries continue to innovate and expand, the role of effective cable management solutions, such as corrugated split sleeve tubing, will undoubtedly become more pronounced, ensuring that operational efficiency and safety remain top priorities.