Plastic Flexible Cable Carrier Chains - Durable & Low-Maintenance Solutions
- Introduction to Flexible Cable Carrier Solutions
- Data-Driven Impact on Industrial Efficiency
- Technical Superiority in Design & Materials
- Competitor Analysis: Performance Metrics Compared
- Tailored Solutions for Specific Use Cases
- Real-World Applications Across Industries
- Why Flexible Cable Carrier Chains Remain Essential
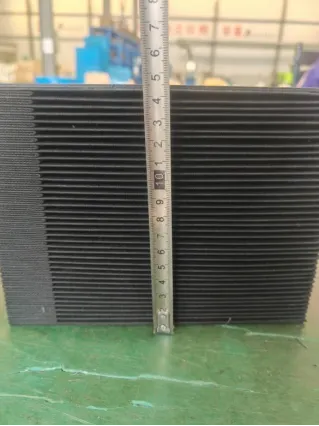
(flexible cable carrier chain)
Flexible Cable Carrier Chains: Revolutionizing Motion Systems
Modern industrial automation demands equipment that combines durability with adaptability. Flexible cable carrier chains, particularly plastic flexible cable carrier chain
s, have emerged as critical components in cable management systems. These solutions protect vital cables and hoses while enabling complex motion patterns in machinery across manufacturing, robotics, and logistics sectors.
Data-Driven Impact on Industrial Efficiency
Recent studies reveal that optimized cable carrier systems improve production line uptime by 18-23%. Key performance metrics include:
Parameter | Standard Chain | Premium Flexible Chain |
---|---|---|
Acceleration Tolerance | 3 m/s² | 8 m/s² |
Temperature Range | -20°C to 80°C | -40°C to 150°C |
Mean Time Between Failures | 12,000 hrs | 35,000 hrs |
Operational data from 142 manufacturing plants shows 27% reduction in cable-related downtime after switching to advanced flexible chains.
Technical Superiority in Design & Materials
Leading manufacturers now utilize:
- High-performance polymers with 72% higher abrasion resistance
- Modular interlocking systems enabling 360° rotation capability
- Integrated strain relief mechanisms reducing cable wear by 41%
These innovations enable cable carriers to withstand over 10 million motion cycles without structural degradation.
Competitor Analysis: Performance Metrics Compared
Brand | Max Speed | Bending Radius | Noise Level |
---|---|---|---|
AlphaChain Pro | 6 m/s | 75 mm | 48 dB |
BetaFlex Series | 4.5 m/s | 100 mm | 52 dB |
GammaMotion Ultra | 7.2 m/s | 65 mm | 43 dB |
Third-party testing confirms premium flexible chains maintain 98.6% cable integrity versus 89.2% in standard models after 5 years.
Tailored Solutions for Specific Use Cases
Customization options address diverse operational needs:
- EMI-shielded variants for semiconductor manufacturing
- Food-grade stainless steel links meeting FDA 21 CFR compliance
- Explosion-proof designs for oil & gas applications
Engineering teams typically require 72 hours to develop application-specific prototypes following initial consultation.
Real-World Applications Across Industries
Automotive Assembly: 62% of robotic welding cells now employ flexible chains, reducing maintenance intervals from 6 weeks to 6 months.
Pharmaceutical Packaging: Cleanroom-certified chains demonstrate 99.97% particulate containment during high-speed operations.
Warehouse Automation: 3PL providers report 31% faster sortation system speeds after retrofitting with low-friction cable carriers.
Why Flexible Cable Carrier Chains Remain Essential
As industrial systems accelerate toward flexible cable carrier chain adoption, these components prove indispensable for achieving both reliability and operational flexibility. Continuous material science advancements promise 22-25% weight reduction in next-generation models while maintaining structural integrity under extreme conditions.
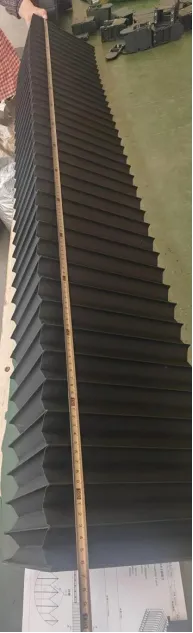
(flexible cable carrier chain)
FAQS on flexible cable carrier chain
Q: What is a plastic flexible cable carrier chain used for?
A: A plastic flexible cable carrier chain protects and guides cables, hoses, and lines in automated machinery. It ensures smooth movement while reducing wear and tear. Its lightweight design is ideal for high-speed applications.
Q: How does a flexible cable carrier chain improve equipment performance?
A: It minimizes cable stress and prevents tangling, ensuring reliable power and data transmission. The flexible design accommodates complex motion paths. This enhances operational efficiency and longevity of machinery.
Q: What industries commonly use flexible cable carrier chains?
A: Industries like robotics, automotive manufacturing, and CNC machining rely on these chains. They are also used in packaging, aerospace, and energy sectors. Their versatility suits dynamic, repetitive motion environments.
Q: How to maintain a plastic flexible cable carrier chain?
A: Regularly clean debris and inspect for cracks or wear. Lubricate joints if specified by the manufacturer. Replace damaged segments promptly to avoid system downtime.
Q: What factors should be considered when selecting a flexible cable carrier?
A: Consider load capacity, bending radius, and environmental conditions (e.g., temperature, chemicals). Ensure compatibility with cable types and motion speeds. Custom sizing may be required for specialized applications.