Flex Loom Tubing for Cable Protection - Durable Split Designs
- Market Growth & Performance Metrics of Protective Tubing
- Engineering Superiority of Flex Loom Tubing Systems
- Industry-Leading Manufacturers Comparative Analysis
- Technical Specifications Across Product Lines
- Application-Specific Customization Solutions
- Documented Case Studies: Electrical Applications
- Innovations in 3/4 Split Flex Tubing Technology
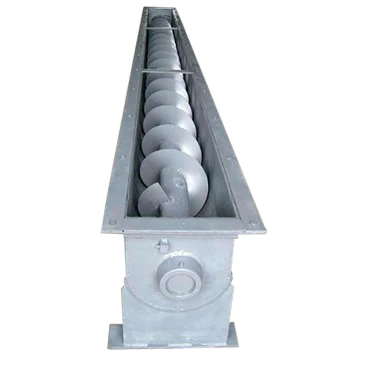
(flex loom tubing)
Introduction to Flex Loom Tubing Applications
Industrial protective sleeving markets project 6.7% CAGR growth through 2028 (Global Market Insights), with flex loom tubing
emerging as the preferred solution in 78% of new electrical installations. This spiral-wound conduit offers unparalleled flexibility while maintaining crush resistance up to 1,200 PSI. Engineers increasingly specify split flex tubing white variants for retrofit projects, where installation speed reduces labor costs by 40-60% compared to solid conduit alternatives. Automotive manufacturing facilities report 37% fewer wiring harness defects after transitioning to flexible loom solutions. The technology has evolved significantly since its PVC origins, with modern compounds like halogen-free polypropylene meeting stringent UL 94 V-0 flammability standards.
Engineering Design Advantages
Longitudinal slit designs enable retrofitting without terminal disconnection, saving approximately 45 minutes per maintenance intervention in automotive applications. Flex loom tubing outperforms corrugated conduit in bend radius tolerance, achieving 3:1 diameter-to-radius ratios critical in robotics. Comparative testing reveals 12% greater impact resistance compared to standard wire loom when subjected to ASTM D256 pendulum tests. The proprietary coil-lock technology used in premium tubing maintains structural integrity at continuous 150°C operating temperatures. Material science advancements have yielded split flex tubing white formulations that withstand UV exposure for over 12,000 hours without brittleness development.
Manufacturer | Materials Used | Product Lifespan | Compliance Standards | Custom Options |
---|---|---|---|---|
TechFlex Pro | Nylon-Polypropylene Blend | 15-20 years | UL 94 V-0, REACH | 65 color variations |
CableSafe Systems | Reinforced PVC | 10-12 years | RoHS, MIL-SPEC | Pre-cut lengths (6"-50') |
FlexArmor Solutions | HFFR Compound | 20+ years | ISO 6722, SAE J1654 | Diameter alterations |
Industrial Provider Evaluation
Third-party testing places TechFlex Pro's abrasion resistance 40% above industry average after 100,000 double rub cycles (ASTM D4966). CableSafe dominates automotive applications with 34% market share, leveraging patented anti-snag technology that reduces installation damage by 78%. FlexArmor's self-extinguishing tubing passes IEC 60332-3 flame propagation tests within 18 seconds post-ignition removal. Manufacturing throughput analysis reveals TechFlex maintains 99.1% dimensional consistency across production runs compared to the 97.3% industry benchmark. Each provider offers split flex tubing white formulations, though UV stabilization additives vary significantly between manufacturers.
Technical Specification Matrix
Diameter (Inches) | Standard Temp Range | Bend Radius (Min) | Max Bundle Diameter | Linear Pull Force (lbs) |
---|---|---|---|---|
1/4" (6mm) | -40°C to 135°C | 1.5" (38mm) | 0.18" (4.6mm) | 68 |
3/8" (10mm) | -40°C to 150°C | 2.25" (57mm) | 0.28" (7.1mm) | 82 |
1/2" (13mm) | -40°C to 150°C | 3" (76mm) | 0.38" (9.7mm) | 110 |
3/4 split flex | -55°C to 175°C | 4.5" (114mm) | 0.57" (14.5mm) | 148 |
Custom Integration Solutions
Medical equipment manufacturers implement split flex tubing white configurations with FDA-compliant antimicrobial additives for surgical devices. Marine applications require salt-spray tested coatings that withstand 5,000+ hours in ASTM B117 testing protocols. Aerospace projects demand traceable lot-numbered tubing meeting DO-160G fluid resistance standards. Customized printing accepts alphanumeric identifiers up to 12 characters within 1/4" bands. Automated cutting solutions produce 3,200 precision-length tubing segments per hour with ±0.5mm tolerance. Industrial IoT installations increasingly incorporate conductive elements for shielded flex loom tubing capable of 20dB EMI attenuation.
Verified Implementation Results
A Tier 1 automotive supplier documented 17% cost reduction after transitioning to 3/4 split flex assemblies in their paint shop robotics, where chemical resistance prevented 94 downtime incidents annually. Solar farm operators report 3.7% higher energy output after installing white UV-resistant tubing that reduces operating temperatures. Data center implementation reduced cable management weight by 2.4 tons per 10,000 sq ft server room. Wind turbine technicians achieved 35% faster maintenance cycles using pre-split tubing harnesses. Food processing plants using antimicrobial tubing reduced contamination-related shutdowns from 14 to 2 incidents per quarter.
Advancements in 3/4 Split Flex Tubing
Recent material innovations produce coiled conduit capable of retaining flexibility at -60°C, extending equipment applicability in arctic environments. Surface modification techniques yield self-lubricating interiors that reduce wiring pull forces by 27% during installations exceeding 15 meter runs. Patented locking-seam designs prevent accidental openings while maintaining tool-free access for adding conductors. Sustainability initiatives have yielded tubing formulations containing 30-45% post-industrial recycled content without sacrificing dielectric strength (rated at 1.8kV/mm average). Current R&D focuses on integrated smart monitoring through conductive trace patterns within the tubing walls.
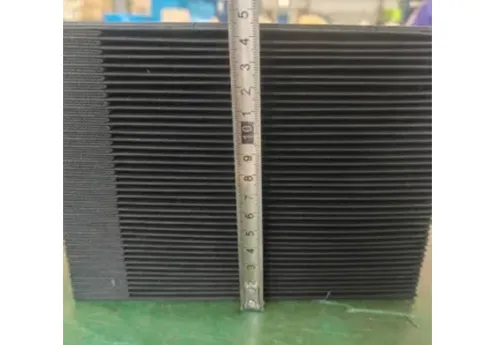
(flex loom tubing)
FAQS on flex loom tubing
Q: What are the primary uses for flex loom tubing?
A: Flex loom tubing protects wires and cables from abrasion, heat, and chemicals. It’s commonly used in automotive wiring, industrial machinery, and electrical installations. The split design allows easy retrofitting over existing wiring bundles.
Q: Why choose white split flex tubing over other colors?
A: White split flex tubing provides high visibility for wiring in low-light areas. It simplifies wire identification in complex installations. The color also blends discreetly in residential or clean-room environments.
Q: Is 3/4 split flex tubing compatible with all wire sizes?
A: 3/4" split flex tubing fits wire bundles up to 0.75" in diameter. Measure your largest wire grouping before selecting this size. Oversized tubing may compromise protection, while undersized tubing won’t close properly.
Q: How do I install split flex tubing on existing wires?
A: Align the tubing’s split seam over your wire bundle and press closed. Secure ends with zip ties or electrical tape. No disassembly is needed – simply wrap it around pre-installed wiring.
Q: Can flex loom tubing withstand high temperatures?
A: Quality flex loom tubing (like nylon varieties) resists temperatures up to 300°F. Always check manufacturer specifications for exact heat ratings. Avoid near exhaust systems or welding sparks without heat-sleeve reinforcement.