Exploring Various Types of Chip Conveyors for Efficient Material Handling Solutions in Industries
Understanding Chip Conveyor Types A Key Component in Manufacturing
In the realm of manufacturing, particularly in machining, the efficient removal of metal chips and swarf is crucial for maintaining productivity and ensuring a clean operational environment. Chip conveyors are integral to this process, providing a streamlined method for handling and transporting waste materials away from machinery. This article explores the various types of chip conveyors utilized in the industry, highlighting their functionalities, benefits, and applications.
1. Belt Chip Conveyors
Belt chip conveyors are one of the most common forms of chip handling systems. They consist of a continuous belt that moves horizontally or at an incline to transport chips from the machining area to a disposal point. These conveyors are versatile and can handle different types of chips, including large and small metal pieces. They are especially advantageous in environments where heavy chips need to be transported over longer distances. The simplicity of design and ease of maintenance make belt conveyors a popular choice among manufacturers.
2. Screw Chip Conveyors
Screw chip conveyors operate using a rotating helical screw blade within a tube to move chips along the conveyor. This type is particularly effective for handling wet or sticky materials, as the enclosed design limits spillage and contamination. Screw conveyors can be configured in various orientations, allowing for flexibility in design and layout. They are often used in applications where space is limited and where there is a need to transport chips vertically or at steep angles.
chip conveyor types
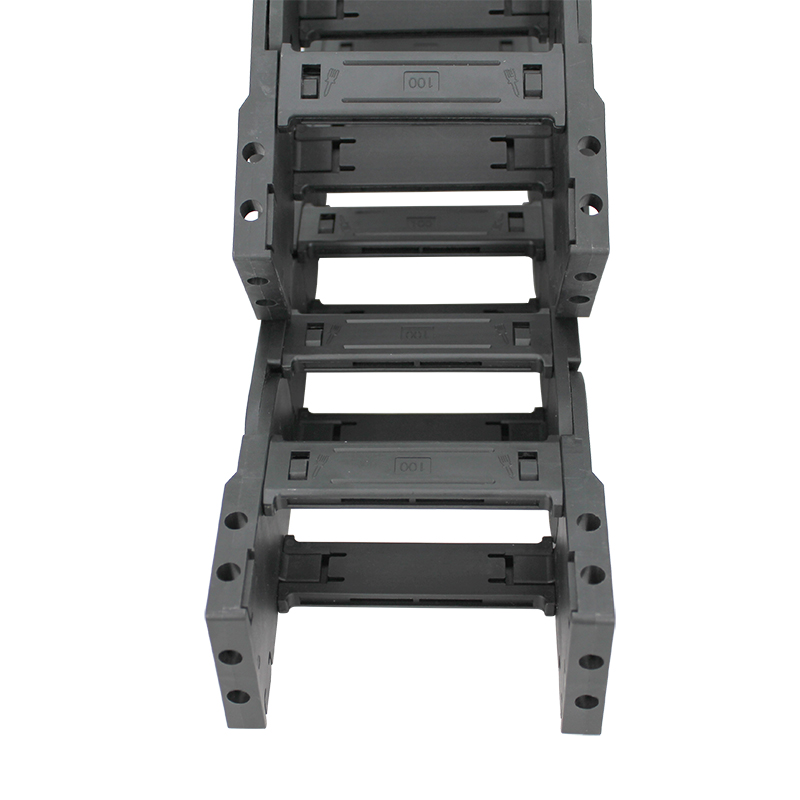
Drag chain conveyors employ a chain mechanism to drag the chips along a trough. This type of conveyor is designed for handling larger volumes of bulk materials and is exceptionally durable. Drag chain systems can transport heavier materials and are ideal for high-volume machining operations. They are also commonly used when the chips have a mix of sizes and shapes. One of the key advantages of drag chain conveyors is their ability to navigate tight spaces due to their compact design.
4. Magnetic Chip Conveyors
For operations that involve ferrous materials, magnetic chip conveyors are an excellent solution. These systems utilize magnetic forces to lift and transport chips away from the machine. They provide a clean and efficient method for chip handling, minimizing the risk of contamination and ensuring the chips are collected from cutting tools effectively. Magnetic conveyors are particularly beneficial in environments where cleanliness is vital, such as in the aerospace or medical device manufacturing sectors.
5. Other Specialized Chip Conveyors
Beyond the conventional types, there are specialized chip conveyors tailored for specific applications. For instance, filtration chip conveyors not only transport chips but also filter coolant and oil from the chips, ensuring that the recycled fluids are clean and usable. Additionally, elevating chip conveyors can move chips from lower levels to higher levels, optimizing space in facilities where vertical movement is essential.
Conclusion
Choosing the right type of chip conveyor is critical for enhancing operational efficiency in manufacturing. Factors such as the type of materials being handled, the volume of chips produced, and the layout of the production area all play a role in determining the most suitable system. Understanding the distinct functionalities and advantages of each conveyor type allows manufacturers to make informed decisions that can streamline their chip handling processes and improve overall productivity. As industries continue to evolve, the importance of innovative chip conveyor systems will undoubtedly grow, contributing to cleaner, more efficient manufacturing environments.