Exploring the Importance and Functionality of Timing Belts in Automotive Engineering and Maintenance
Understanding the Importance of Sync Belts in Modern Machinery
In the world of mechanical engineering and machinery, numerous components play a critical role in ensuring optimal performance and efficiency. Among these components, the sync belt (also known as a synchronous belt) stands out due to its unique design and functionality. This article explores the significance of sync belts, their applications, advantages, and maintenance considerations.
What is a Sync Belt?
A sync belt is a type of timing belt designed with teeth along its length, which interlock with corresponding teeth on pulleys. This tooth engagement allows for precise timing and synchronization between rotating shafts, making sync belts essential in various machines. Unlike standard V-belts, which rely on friction to operate, sync belts maintain a positive drive, ensuring that there is no slippage and that the drive remains consistent under varying loads.
Applications of Sync Belts
Sync belts are widely used in various applications across numerous industries. Their primary applications include
1. Automobiles In internal combustion engines, sync belts are critical in synchronizing the rotation of the crankshaft and camshaft. This synchronization is vital for ensuring that the valves open and close at the appropriate times, preventing engine damage and optimizing performance.
2. Industrial Machinery Many manufacturing processes rely on sync belts to drive equipment such as conveyor systems, printing presses, and injection molding machines. Their ability to maintain precise timing contributes to the overall efficiency and output of production systems.
3. Robotics In robotic applications, sync belts facilitate accurate movement and positioning. Their ability to transmit power without slipping allows for precise control in automated systems, enhancing productivity in manufacturing and assembly lines.
4. Home Appliances Sync belts find their way into everyday appliances, such as washing machines and food processors, where they help in driving various components with precision.
Advantages of Sync Belts
The use of sync belts in machinery offers several advantages
sync belt
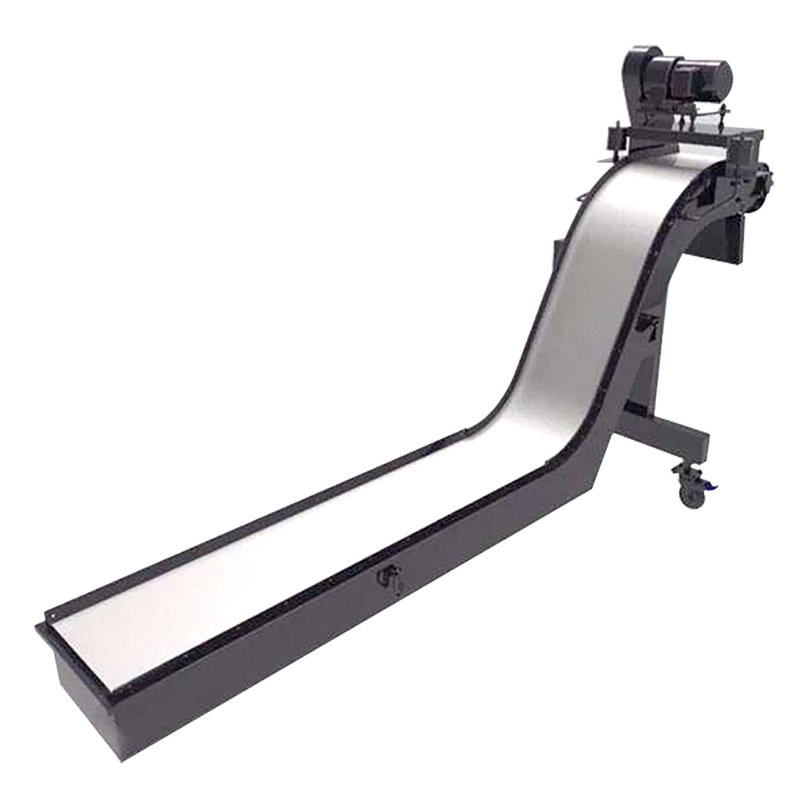
1. High Efficiency Sync belts provide a high level of efficiency by transferring power without slippage. This means that energy losses are minimized, resulting in better performance and reduced operational costs.
2. Precision Timing The design of sync belts ensures that components operate in perfect harmony. This precision reduces wear and tear on machine parts, extending their lifespan and reliability.
3. Low Maintenance Compared to other types of belts, sync belts require less maintenance. Their construction from durable materials, such as neoprene or polyurethane, enhances their longevity and resistance to wear.
4. Reduced Noise Sync belts operate more quietly than traditional V-belts, leading to a more pleasant working environment, particularly in industrial settings.
Maintenance Considerations
To ensure the longevity and optimal performance of sync belts, regular maintenance is essential. Key maintenance practices include
- Inspection Regularly check for signs of wear, such as fraying or missing teeth. Any visible damage should be addressed immediately to prevent further issues.
- Tension Adjustment Proper tension is critical for the efficient operation of sync belts. Over time, belts may stretch, leading to decreased performance. Regular tension checks and adjustments should be performed as necessary.
- Cleaning Dust and debris can accumulate on sync belts and pulleys, leading to reduced efficiency. Keeping these components clean will help maintain optimal performance.
Conclusion
Sync belts are a fundamental component in various mechanical systems, offering precision, efficiency, and reliability. Understanding their function and application is crucial for anyone involved in the design, maintenance, or operation of machinery. By investing in quality sync belts and adhering to proper maintenance protocols, industries can enhance productivity, minimize downtime, and ensure the smooth operation of their equipment.