Exploring the Benefits of 1% to 4% Wire Loom for Effective Cable Management Solutions
Wire Loom A Comprehensive Guide on 1% 201% 4% Wire Loom
In the world of electrical wiring and cable management, wire looms play a crucial role in ensuring safety, organization, and efficiency. The term “wire loom” refers to a protective covering for wires that helps in bundling them together, shielding them from damage, and preventing various hazards. Understanding the significance of wire looms, particularly in contexts like 1% 201% 4% wire loom, can help in making informed choices for various applications.
What is Wire Loom?
Wire loom is typically made from materials such as plastic, nylon, or polyethylene, which provide flexibility, heat resistance, and durability. These materials are designed to withstand various environmental factors, including temperature fluctuations, chemical exposure, and physical abrasion. Wire looms come in different sizes, shapes, and configurations to accommodate various wire bundles, making them versatile for numerous applications ranging from automotive wiring to industrial machinery.
Understanding 1% 201% 4% Wire Loom
When discussing wire loom specifications, terms like 1%, 201%, and 4% may refer to various designations or standards that can be associated with the material properties, manufacturing tolerances, or dimensions. For instance, the “1%” could indicate the tolerance level in material thickness, while “201%” might refer to a specific adaptability feature in the wire loom design, and “4%” could denote a certain percentage of flexibility or stretch under various stresses.
Applications of Wire Loom
Wire looms are employed in numerous industries
1. Automotive Industry In vehicles, wire looms protect essential wiring harnesses from heat, moisture, and mechanical wear. Effective cable management is vital in ensuring the reliability of electrical systems in cars, trucks, and other vehicles. For example, 1% 201% 4% wire loom might be used in regions where wires are more susceptible to wear and tear, ensuring longevity and performance.
1 1 4 wire loom
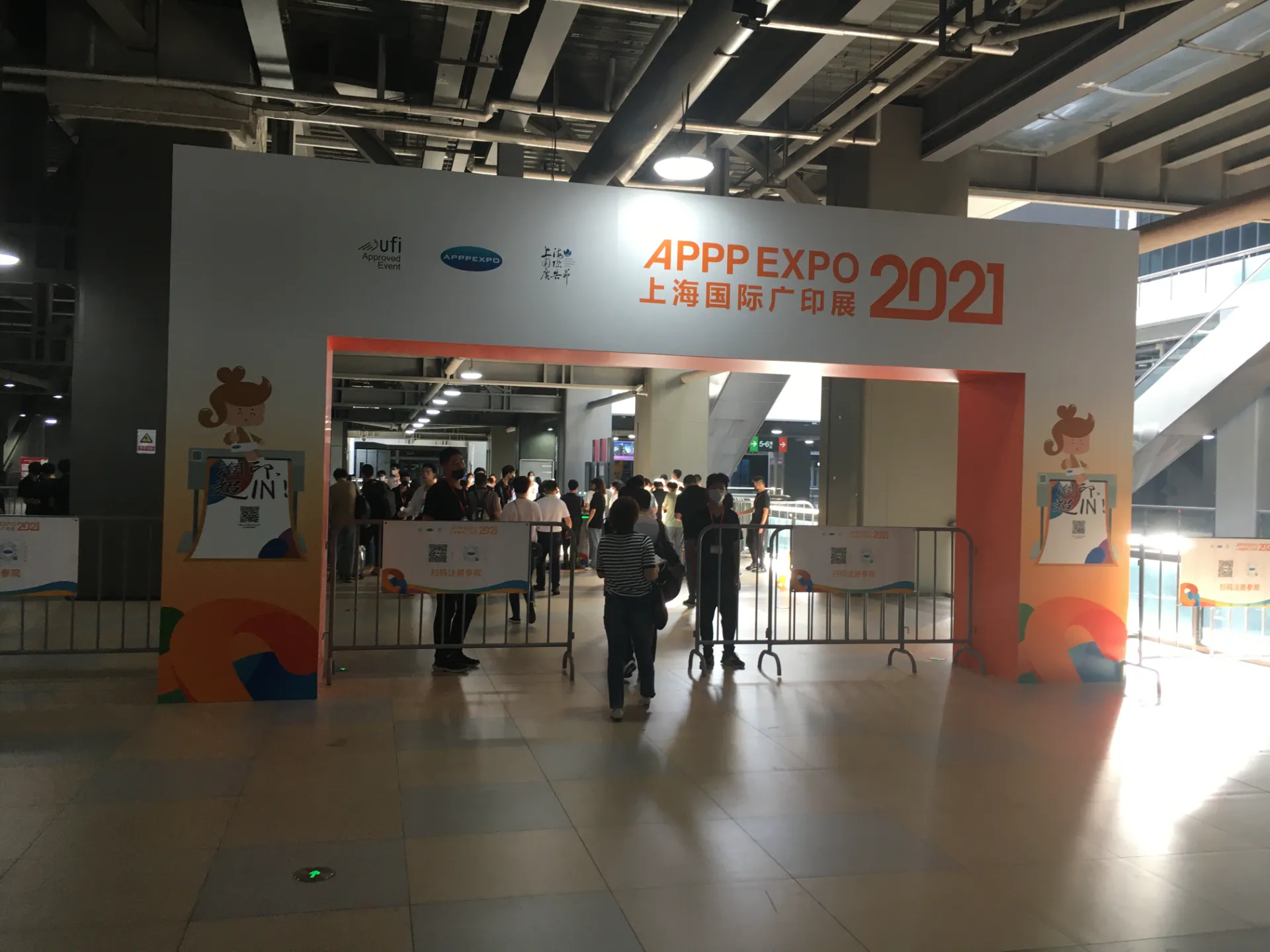
2. Industrial Machinery In manufacturing settings, wire looms help keep control panels and machinery wiring organized, reducing the risk of faults caused by loose or damaged wires. By utilizing specific standards like 1% 201% 4%, manufacturers can ensure that their machinery operates efficiently within the required parameters.
3. Home and Commercial Electrical Installations For both residential and commercial buildings, wire looms are essential in maintaining neat and safe wiring. They prevent tangling, reduce the risk of electric shocks, and aid in easy identification of circuits during maintenance.
Benefits of Using Wire Loom
The advantages of using wire loom are manifold
- Protection They shield wires and cables from environmental hazards such as moisture, dust, chemicals, and physical damage. This improves the durability and lifespan of electrical installations.
- Organization By bundling wires, wire looms facilitate easier maintenance and troubleshooting. This organization is critical in complex setups, ensuring that technicians can quickly locate and address issues.
- Safety Wire looms help to avoid short circuits caused by frayed or exposed wires. This intrinsic safety feature can significantly reduce the risk of electrical fires.
Conclusion
In summary, wire looms are an integral part of effective electrical management in various industries, ensuring safety, organization, and protection for wiring systems. The specifications like 1% 201% 4% provide important guidance in selecting the right loom for specific applications, helping users to meet their needs effectively. Understanding these elements can aid electricians, engineers, and consumers in making informed decisions, leading to more reliable and efficient electrical systems. Whether in automotive applications or industrial settings, the adoption of wire looms remains a best practice for anyone involved in wiring and electrical design.