Exploring the Applications and Benefits of Telescopic Bellows in Modern Engineering Solutions
Understanding Telescopic Bellows Design, Applications, and Benefits
Telescopic bellows are innovative mechanical components used in various industries to protect moving parts, maintain system integrity, and enhance the longevity of equipment. These versatile structures are designed to expand and contract in a telescopic manner, allowing them to accommodate different stroke lengths while safeguarding internal components from debris, liquids, and environmental conditions. This article explores the design, applications, and benefits of telescopic bellows, highlighting their crucial role in modern engineering.
Design Features
Telescopic bellows are typically constructed from durable materials such as rubber, polyurethane, or PVC, which provide flexibility and resilience against wear and tear. Their design consists of multiple overlapping layers or sections that allow for extension and retraction. The bellows can be tailored to specific requirements, including diameter, length, and stiffness, making them adaptable for various applications.
The sectioned design not only facilitates movement but also minimizes friction and ensures smooth operation. Furthermore, the flexibility of the material allows for compensation of misalignment in shafts or rods, reducing stress on connected components and enhancing the overall reliability of the machinery.
Applications
Telescopic bellows find applications in a wide range of industries, including manufacturing, automotive, aerospace, and robotics.
1. Manufacturing Equipment In machine tools and conveyors, telescopic bellows protect moving parts like spindles and linear guides from dust, chips, and lubricants. This protective function ensures efficient operation and reduces maintenance needs.
2. Automotive Industry In vehicles, these bellows are often used in steering columns and suspension systems as dust covers. They help keep contaminants out, thereby prolonging the life of critical components such as joints and bearings.
3. Aerospace In the aerospace sector, telescopic bellows serve to seal and protect actuators and other components from harsh environmental conditions. They ensure the functionality of equipment that operates under extreme pressure and temperature variations.
telescopic bellow
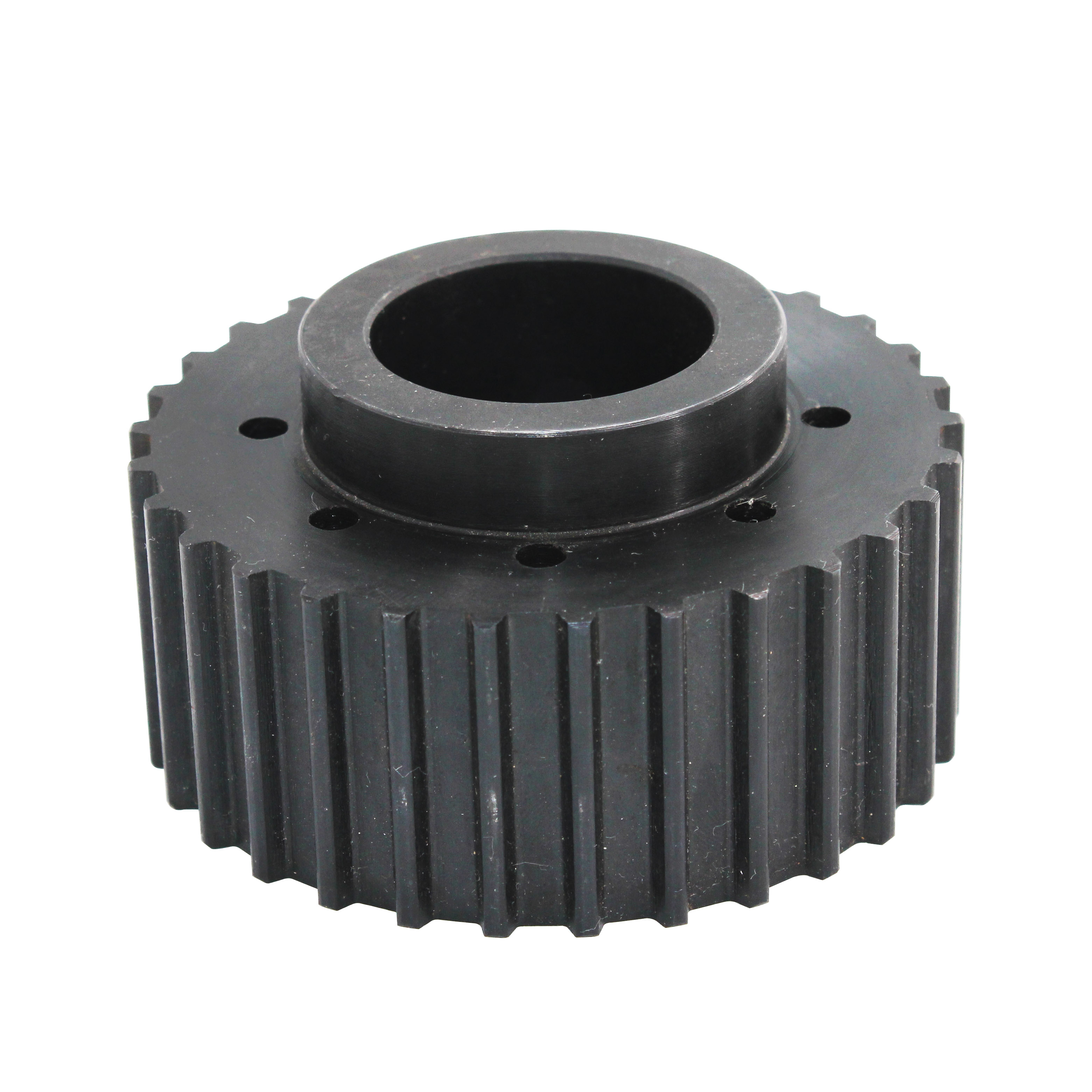
4. Robotics In robotic arms, telescopic bellows enable smooth movement while safeguarding sensitive parts from debris and abrasion. This feature is crucial for maintaining precision in robotic applications.
Benefits
The benefits of using telescopic bellows are manifold.
- Protection One of the primary advantages is their ability to protect moving parts from contaminants, thus reducing wear and prolonging the lifespan of machinery. This protection leads to decreased downtime and lower maintenance costs.
- Flexibility Telescopic bellows can accommodate various stroke lengths and movements, making them ideal for dynamic applications. Their flexibility ensures that systems function smoothly even under varying operational conditions.
- Cost-efficiency While the initial investment in telescopic bellows may be higher than traditional protective methods, the long-term savings in maintenance and replacement parts often outweigh initial costs. Their durability reduces the frequency of part replacement, contributing to overall cost savings.
- Customization The ability to customize size, shape, and material composition allows engineers to design bellows that meet specific operational demands. This customization is essential for specialized applications where standard components cannot provide the necessary protection or fit.
Conclusion
In conclusion, telescopic bellows play a vital role in modern engineering by providing protection, flexibility, and cost efficiency across various industries. Their unique design and functionality cater to the needs of complex machinery and equipment, ensuring smooth operation and enhanced durability. As technology advances, the applications for telescopic bellows will continue to expand, solidifying their position as essential components in the design and maintenance of innovative mechanical systems.