Exploring Different Types of Chip Conveyors for Enhanced Manufacturing Efficiency and Productivity
Types of Chip Conveyors Optimizing Efficiency in Manufacturing
In modern manufacturing environments, the management and disposal of metal chips generated during machining processes are critical for operational efficiency and safety. Chip conveyors play an essential role in collecting and transporting these chips away from machines, preventing buildup that can lead to downtime and safety hazards. There are several types of chip conveyors, each designed to meet specific needs based on the type of machining process and materials being handled. Understanding these types can help manufacturers choose the most suitable system for their operations.
1. Drag Chain Conveyors
Drag chain conveyors are usually designed for heavy-duty applications where large metal chips and turnings are produced. These conveyors utilize a chain that runs through a series of tracks or rails, dragging the chips away from the source. The advantage of drag chain systems is their ability to handle large volumes of heavy material while maintaining a compact footprint. They are often made from robust materials to withstand harsh environments and ensure long-term durability.
2. Screw Conveyors
Screw conveyors are another common type used in chip management systems. They consist of a rotating helical screw that moves chips along a trough. This method is highly effective for moving small to medium-sized chips and is particularly useful in applications where space is limited, as screw conveyors can be installed at various angles. They are versatile, adaptable to different types of materials, and can be enclosed to prevent the spread of chips and improve safety.
3
. Enclosed Belt Conveyorschip conveyor types
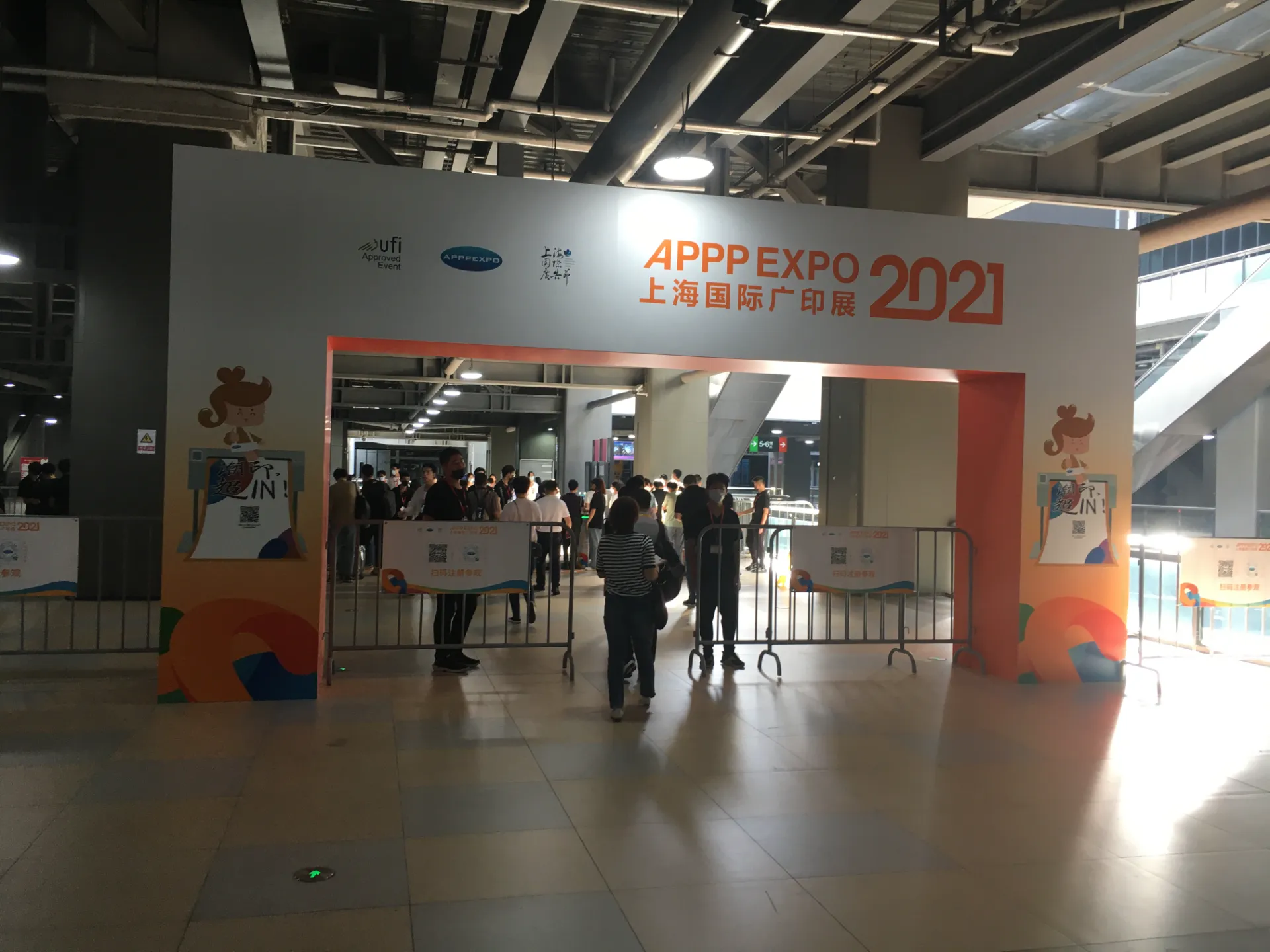
Enclosed belt conveyors feature a continuous belt that transports chips within a protective casing. These systems are ideal for dealing with fine particles and smaller chips, as they minimize dust and ensure chips are secured during transportation. The enclosed design also reduces the risk of accidental spillage, particularly in environments sensitive to cleanliness and safety. Enclosed belt conveyors can be customized in terms of size and capacity, making them suitable for various applications.
4. Magnetic Strip Conveyors
For operations involving ferrous materials, magnetic strip conveyors are highly effective. These conveyors utilize a magnetic surface to attract and hold metal chips, helping to efficiently move them away from the machining area. They are particularly beneficial for separating chips based on material types, allowing for easier recycling and disposal processes. Magnetic conveyors are ideal for processes that generate a significant quantity of small, ferrous chips.
5. Vibratory Chip Conveyors
Vibratory chip conveyors use controlled vibrations to move chips along a trough. This type of conveyor is often used to convey bulk materials efficiently and is particularly adept at handling chips that may stick together. The gentle movement reduces breakage of chips, which is critical for certain applications where chip integrity must be maintained. Vibratory systems are flexible and can be inclined to save space or fit specific layouts.
Conclusion
Selecting the right type of chip conveyor is crucial for optimizing production efficiency and maintaining a safe working environment. Manufacturers must consider the type of materials being processed, the volume of chips generated, and the space available when choosing a conveyor system. By investing in the appropriate chip conveyor technology, manufacturers can enhance their operational workflow, reduce costs associated with downtime and waste management, and ultimately lead to a more productive and sustainable manufacturing process. Through continuous innovation and tailored solutions, chip conveyors remain a crucial component in the manufacturing landscape, driving efficiency and reliability in machining operations.