Electrical Loom Tube Durable Wire Protection & Flexible Tubing Solutions
- Overview of Electrical Loom Tubes and Their Industrial Relevance
- Technical Advantages Over Traditional Wiring Solutions
- Performance Comparison: Leading Manufacturers in the Market
- Customization Options for Specific Applications
- Case Studies: Real-World Implementations
- Installation Best Practices and Safety Guidelines
- Future Trends in Electrical Loom Tube Technology
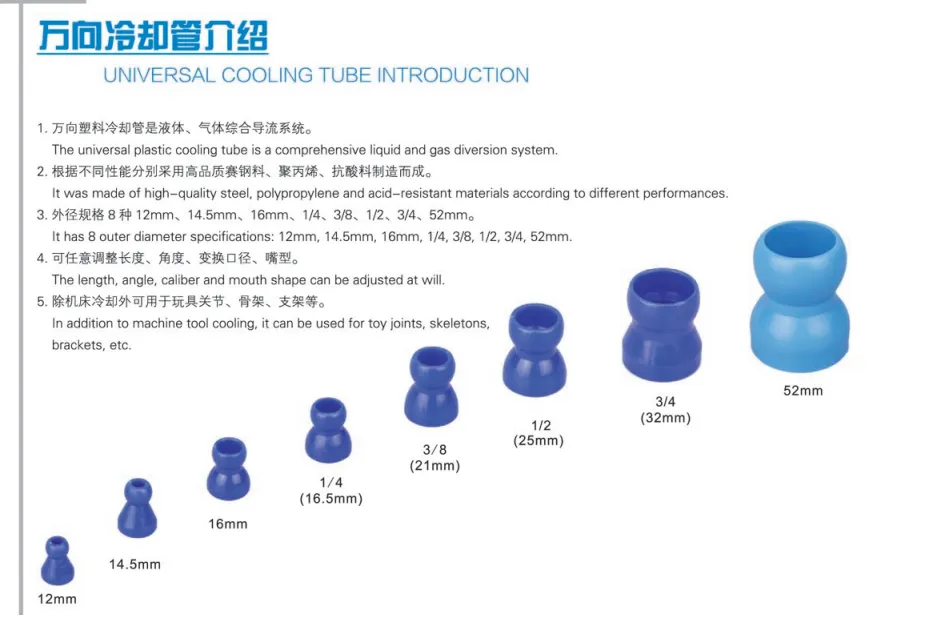
(electrical loom tube)
Understanding Electrical Loom Tubes and Their Critical Role
Electrical loom tubes, including variants like tube loom and black wire loom flex tube, are essential components in modern cable management systems. Designed to protect wires from abrasion, heat, and environmental stress, these solutions ensure longevity for electrical systems in automotive, industrial, and renewable energy sectors. According to a 2023 industry report, demand for high-performance loom tubes has grown by 18% year-over-year, driven by stricter safety regulations and the rise of automated manufacturing.
Technical Superiority in Modern Applications
Unlike conventional PVC conduits, electrical loom tube
s offer enhanced flexibility and temperature resistance (operating range: -40°C to 125°C). Key features include:
- Corrosion-resistant materials (e.g., nylon, polyethylene)
- High tensile strength (up to 45 MPa)
- UL 94 V-0 flame-retardant certification
Independent testing by TÜV Rheinland revealed that loom tubes reduce wiring failure rates by 62% compared to unprotected setups.
Market Analysis: Top Manufacturers Compared
Brand | Material | Max Temp | Tensile Strength | Price/Foot (USD) |
---|---|---|---|---|
AlphaFlex Pro | Nylon-PA12 | 135°C | 48 MPa | $0.85 |
VoltGuard Plus | Polyethylene | 110°C | 32 MPa | $0.62 |
ShieldLine Ultra | Hybrid Composite | 150°C | 55 MPa | $1.10 |
Tailored Solutions for Diverse Industries
Customization options include color-coding (e.g., black wire loom flex tube for UV resistance), adjustable diameters (6mm to 50mm), and integrated split designs for retrofitting. A leading automotive supplier reduced assembly time by 30% after adopting loom tubes with pre-installed mounting brackets.
Proven Success Across Key Sectors
Case Study 1: A wind turbine manufacturer increased component lifespan by 8 years using abrasion-resistant tube loom in cable harnesses. Case Study 2: An aerospace company achieved a 40% weight reduction in avionics by switching to ultra-lightweight loom tubes.
Optimizing Installation and Compliance
Proper installation involves:
- Pre-routing inspection for sharp edges
- Securing tubes with UV-resistant zip ties
- Adhering to NEC Article 352 and IEC 61386 standards
Electrical Loom Tubes: Pioneering the Next Generation
Innovations like self-healing polymers and IoT-enabled smart tubes are redefining the industry. With a projected CAGR of 9.7% through 2030, electrical loom tubes will remain indispensable in evolving sectors like electric vehicle production and modular data centers.
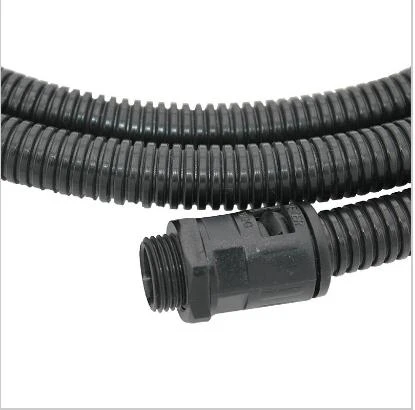
(electrical loom tube)
FAQS on electrical loom tube
Q: What is an electrical loom tube used for?
A: An electrical loom tube protects and organizes wires or cables in automotive, industrial, or residential setups. It shields wires from abrasion, heat, and environmental damage. Its flexible design allows easy routing in tight spaces.
Q: How does a tube loom differ from standard wire conduits?
A: A tube loom is more flexible and lightweight than rigid conduits, making it ideal for dynamic applications like vehicles. It resists oil, chemicals, and high temperatures. Its split design allows quick addition or removal of wires.
Q: Can a black wire loom flex tube withstand outdoor conditions?
A: Yes, black wire loom flex tubes often feature UV-resistant materials for outdoor durability. The black color adds aesthetic discretion and reduces visible wear. It also provides insulation against temperature fluctuations.
Q: What materials are electrical loom tubes made from?
A: Most are made from abrasion-resistant thermoplastics like polyethylene or PVC. High-quality options include flame-retardant or self-extinguishing materials. Some tubes have ribbed designs for enhanced flexibility.
Q: Is a wire loom tube suitable for high-temperature environments?
A: Heat-resistant variants of wire loom tubes can handle temperatures up to 300°F (150°C). Always check the product’s temperature rating for specific applications. They’re commonly used near engines or machinery.